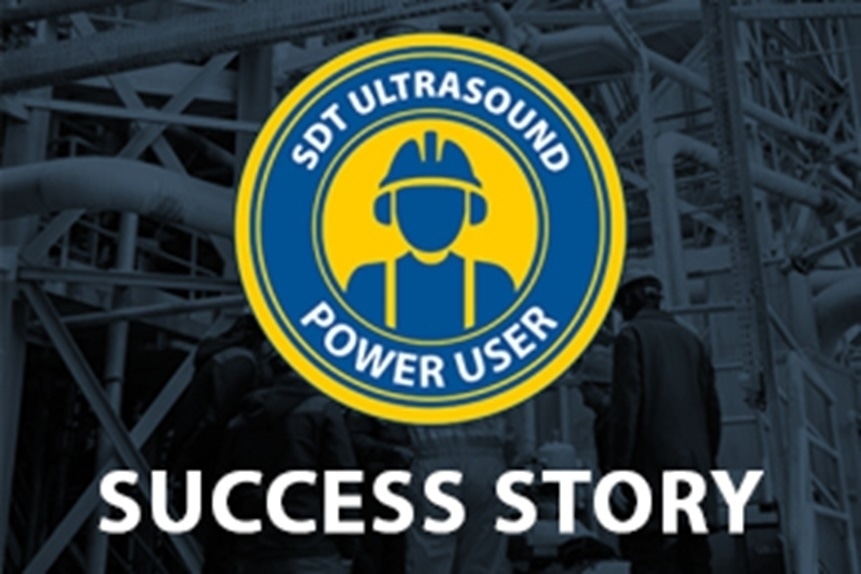
#Industry News
Transforming Bearing Reliability in a Greek Paper Mill
For one paper mill in Greece, frequent bearing failures were causing significant disruptions, leading to unexpected downtime, increased maintenance costs, and declining production efficiency.
Despite multiple attempts to address the issue, including advice from third-party service providers, the problem persisted. It wasn’t until the maintenance team adopted a new approach using ultrasound technology that they finally resolved the issue, leading to remarkable improvements in their operations.
The challenge: Unexplained bearing failures
The maintenance department at the paper mill was grappling with a perplexing problem. Bearings that should have lasted much longer were failing after just one month of operation. This frequent need for replacements was not only costly in terms of materials and labor but also caused substantial downtime, which disrupted production and threatened the company’s bottom line.
Initially, the team suspected that the type of bearings used might be the issue. They followed advice from external service providers and switched to bearings with less internal clearance. However, this change did not solve the problem. With failures continuing at the same rate, it became clear that the root cause lay elsewhere.
The discovery: Over-lubrication identified as the culprit
The breakthrough came after a presentation by REA Hellas, which introduced the maintenance team to the potential of ultrasound technology for monitoring bearing lubrication and condition. Curious to explore this further, the paper mill decided to invest in an ultrasound device called the LUBEChecker and invited REA Hellas to conduct an on-site assessment of their lubrication practices.
The assessment revealed a critical issue: every bearing was being over-lubricated, causing premature failures. This discovery was a turning point. The team now had a clear path forward—by optimizing lubrication through precise monitoring, they could significantly extend the life of their bearings and reduce the associated costs.
Strategic implementation: A new approach to maintenance
With this newfound knowledge, the maintenance team implemented a more strategic approach to their work. They recognized that the bearing failures were a result of a time-based failure mode directly linked to over-lubrication. By addressing this specific issue, they could not only increase bearing longevity but also reduce grease consumption and associated costs.
The use of ultrasound technology became central to their maintenance strategy. By continuously monitoring bearing conditions and adjusting lubrication practices accordingly, they were able to prevent over-lubrication and the premature failures it caused. This proactive approach marked a significant shift from their previous reactive maintenance practices.
Expanding the impact: Beyond bearings
Encouraged by the success in resolving the bearing issue, the maintenance team decided to explore the possibility of expanding their use of ultrasound technology to other areas of the plant. They considered acquiring more advanced ultrasound equipment, such as the SDT340, which could be used for a wide range of applications including electrical inspections, valve and steam trap monitoring, and gas leak detection.
To fully capitalize on these tools, the team understood that continuous learning and skill development were essential. They aimed to build a comprehensive internal monitoring network, enabling them to collect and analyze data across various aspects of plant operations. This data-driven approach would allow them to take maintenance actions only when necessary, further increasing efficiency and reducing unnecessary costs.
Overcoming challenges: Seeking management buy-In
While the technical benefits of ultrasound technology are clear to the maintenance team, securing management’s approval for further investment in these tools and practices remains a challenge. To demonstrate the potential benefits, the head of the monitoring department should propose a trial period. By setting up a framework for monitoring and comparing the results after six months, they would be able to build a compelling case for continued investment.
The team recognizes the importance of translating technical improvements into financial metrics that would resonate with management. They plan to consistently report on the cost savings and efficiency gains achieved, showing how the new approach could directly contribute to the company’s profitability. However, the final decision from management is still pending.
The potential outcome: A sustainable shift in reliability
If fully implemented, the adoption of ultrasound technology could lead to a profound change in the paper mill’s operations. By reducing bearing failures, the mill would experience less downtime, lower maintenance costs, and improved production efficiency. The potential success of this initiative could also foster a culture of proactive maintenance and continuous improvement within the organization.
The paper mill’s journey from frequent bearing failures to potentially reliable and efficient operations is a testament to the power of innovative thinking and the right tools. By addressing the root cause of their problem and considering a strategic, data-driven approach to maintenance, they have the opportunity to achieve results that could transform their business. The success lies not just in solving a technical issue but in creating a sustainable, long-term improvement in how they operate—if management gives the green light.