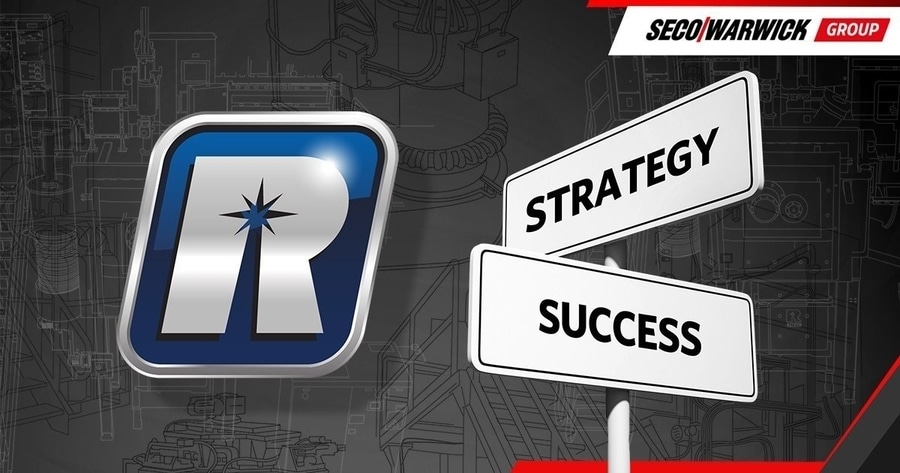
#Industry News
RETECH HAS BEEN PIONEERING NEW DOMAINS IN POWDER METALLURGY
Retech, a SECO/WARWICK company, has been a leader in vacuum metallurgy for over 60 years. Their recent successes are built on a foundation of strong leadership and long-established excellence in melting technology. Their latest innovation in Plasma Gas Atomization goes far beyond incremental improvement, positioning them to offer technology that substantially broadens the possibilities for industry leaders in manufacturing and enables large-scale production of additive manufacturing.
History, and the Success Strategy on Which Retech Was Built
Retech has been manufacturing melting equipment for reactive and refractory metals for over 60 years. Their solutions have always played a critical role in national defense strategies, and as such, these projects are seldom disclosed to the public domain and we rarely hear about the successes in those particular industries. The necessity of this discretion, combined with the nature of a business that produces large, complex melting equipment, requires that their business model, and their success, always prioritize a focus on the customer rather than the price. This practice seems to resonate with customers who value a partnership toward success rather than a more arms-length approach.
Recent Successes and Current Trends
Over the last few years, Retech has continued to grow along with its customers and has commissioned more furnaces each successive year. Between 2018 and 2021, Retech relocated all of their US-based manufacturing and most of their office space from Ukiah, California, to Buffalo, NY. During the move and subsequent upstaffing, it continued to meet orders through careful planning and a deep bench of dedicated employees, suppliers, and fabricators.
Prudent risk avoidance allowed them to continue to support their customers, most of whom were considered essential U.S. manufacturers, throughout the crisis.
Emerging from the global crisis, it became apparent that Retech’s business was strong enough that they required another new facility in Buffalo, in addition to the one they had just moved into three years prior. In 2021 Retech had a record sales year, despite the lingering ripple-effects of the crisis, and in 2022, they topped their 2021 numbers. Bookings for 2023 were even stronger than the prior year, allowing the company to post a third consecutive record year.
After a long search, the company was able to secure their second Buffalo facility just in time for their 60th anniversary celebration in the summer of 2023.
“When we moved into our new Buffalo headquarters, we anticipated an upward trajectory, but this really exceeds expectations. This move puts us at 113,000 total square feet of R&D, manufacturing, assembly, and storage space, which allows us to stay ahead of that growth instead of catching up to it,” said Earl Good, Retech Managing Director / President.
The upward trajectory Earl spoke of was largely coming from Retech’s strongest performing product categories in recent years, which include:
Electron Beam (EB) melters, ideal for melting and refining reactive and refractory metals that require a vacuum process.
Plasma Arc Remelt (PAM), best suited for melting reactive or refractory metals being alloyed with lighter, lower vaporization temperature metals than the primary alloying metal. As Retech’s highest power furnace, many customers have ordered multiple units and come back for repeat orders.
Vacuum Arc Remelt (VAR) systems, the workhorse of reactive/refractory metal ingot production for later rework in mills.
Vacuum Induction Melting (VIM), used in the mass production high-value materials.
Niche sales in small scale atomizers and other custom specialty equipment with lower sales volume, but still of critical importance for certain metallurgical processes.
Powder Metal and Ribbon production equipment.
What’s next for Retech?
Retech will continue as a global leader of controlled atmosphere melting technology for their traditional markets like aerospace, automotive, energy, and biotech, including many projects already in development. In addition to that, Retech is also about to turbocharge the Powder Metallurgy (PM) sector with their latest breakthrough in Plasma Gas Atomization (PGA), and the timing couldn’t be better.
Earl points out that, “At Retech, we are too busy commissioning new furnaces, and trusted by customers with too many trade secrets and defense clearances, to be able to boast of our accomplishments much, so it is a delight to have a new innovation in PGA that we can shout from the rooftops!”
Plasma Gas Atomization is not new for Retech. What is new is the development of an integrated system, informed by our customers, that maximizes versatility in nearly every metric allowing for:
Scalability, achieving atomization rates greater than 10 times the rate of currently available technologies
Atomization of any metal or alloy suitable for plasma arc melting (PAM)
Utilization of most feedstock format, including sponge, compacts, recycled scrap, ingots
Ultra-pure inclusion-free powders
Continuous processing enabled by air-lock style feeder system that does not interrupt melting to recharge
Elimination of clog-prone nozzles, improving reliability and simplifying cleaning and product changeover
While Retech’s suite of melting technologies is capable of melting a wide range of reactive and refractory elemental metals and alloys, titanium melting in particular serves as a reliable bellwether.
Companies are finding more and more uses for titanium in their products, even consumer grade products, but in addition to finding use, they are finding appeal. It certainly helps titanium producers when titanium is perceived as a prestige product, with that prestige even spilling over into products that are not even particularly reliant on titanium, like cell phone cases or fancy camping gear. But now titanium is used as a product name for car models, and even as a luxury signifier for the credit card tier above platinum.
Put more simply, titanium is cool now. And not just with consumers, but in the investor class too.
Which means big titanium producers and small titanium additive manufacturers alike can now attract more investment dollars more easily.
So, just when investors are more eager to invest in titanium, and additive manufacturers are more eager to get their hands on titanium powder, Retech’s PGA is about to take the cost of Titanium Atomization and move the decimal point to the left.
Talk about turbocharging!
Kicking off this chain of investment, and serving as further validation of Retech’s success, is a recent investment in Retech itself — secured by their parent company, SECO/WARWICK – in the form of a $10 Million subsidized loan awarded to Retech for the expansion of their PGA equipment manufacturing capabilities and other advanced technologies so that they can meet the growing demand for their new PGA systems. The $10 million loan comes from the Foreign Expansion Fund 2 FIZ AN managed by PFR TFI, which offers companies co-financing of their foreign investment projects through financial instruments tailored to the scale of the project and the capabilities and needs of the Polish investor.
“This dovetails perfectly with our recent membership in America Makes, the National Additive Manufacturing Innovation Institute . Sure, I look forward to what the big players will do with the less expensive powder metals Retech will enable, but they already have access to the material and technology,” Earl continues, “but what really excites me is the opportunity to see what creative young minds can do with this once Retech makes it accessible enough that they can afford to have fun with Ti AM in a garage-tech sense. Take bold steps without fear of mistakes. It is not so much about making the existing tech less costly, the excitement is in the fields where titanium will become a feasible option, where it was not before.”
Sławomir Woźniak, CEO, SECO/WARWICK Group goes on to conclude, “I’m confident our proudest success will be something beyond my imagination that one of these young innovators will create in the next five or ten years. If we can offer them the materials, our bottom line will take care of itself.”