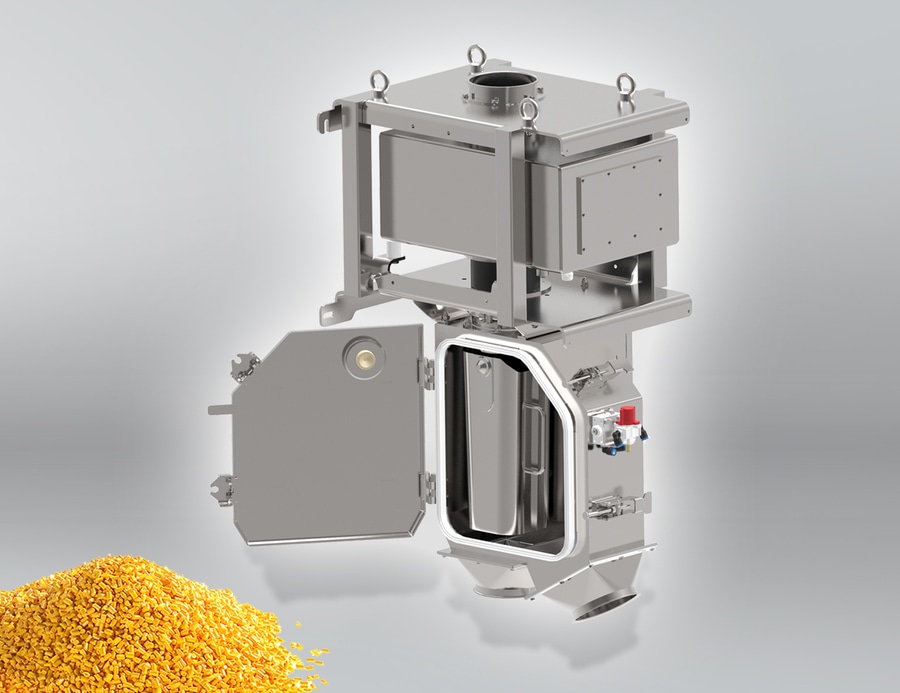
#White Papers
Keeping plastic compounds free of metallic contaminants
A new Whitepaper from Sesotec helps plastic manufactures choose a suitable metal separator
Schönberg, September 2020
When it comes to plastics compounding and masterbatch production, a certain degree of machine wear and tear is part of doing business. On a semi-regular basis, machines must be replaced, parts changed out, and facilities retrofitted. While some machine downtime is unavoidable, materials harboring metallic contaminants can lead to frequent, unplanned stops that incur costly repairs and quality assurance issues. Metal separators play a key role in keeping metallic contaminants out of product streams.
Granulate manufacturers and compounders have special requirements when it comes to protection against metallic contaminants. Not only must metal separators in this branch operate with high detection accuracy, but they must also guarantee short cleaning times. Reliable metal separators can increase line availability, ensure product quality, and prevent customer complaints. Particularly for compounding and masterbatch production lines, metal separators can improve profitability.
The Whitepaper “Keeping metallic contaminants out of plastic compounds” explores the challenges that metal contamination poses to compounding and masterbatch production and considers the key features that metal separators must have to provide an adequate solution.
The Whitepaper covers the following topics:
- Common sources of metal contaminants in compounding and masterbatch production
- The problems caused by metal contaminants
- Preventative measures against metallic contaminants
- What compounders expect from a metal separator