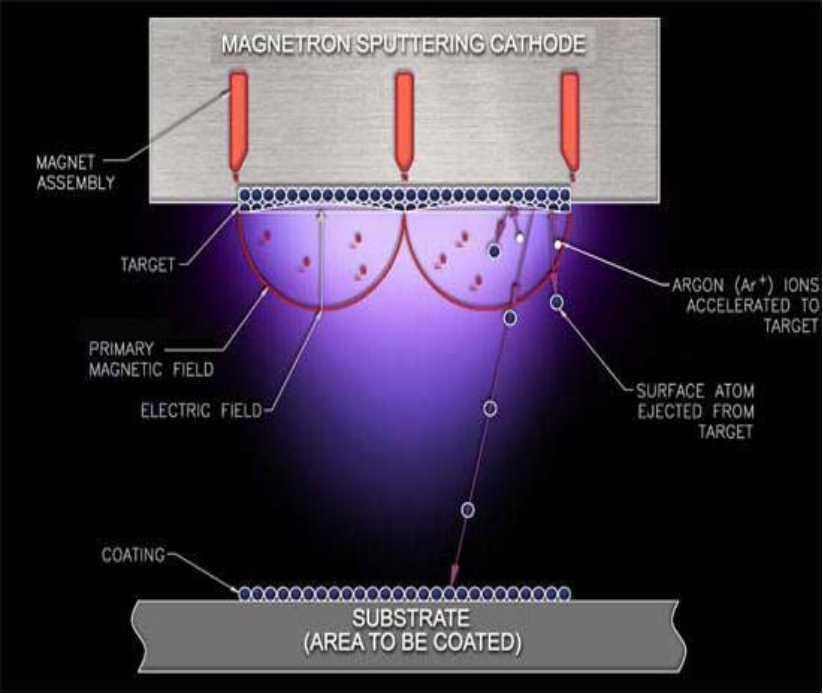
#Product Trends
Magnetron Sputtering Deposition Technology
PVD sputtering deposition
What is Vacuum Sputtering Deposition
1. Sputtering deposition is the deposition of particles vaporized from a surface, which is called the “sputtering target,” by the physical sputtering process.
2. Physical sputtering is a nonthermal vaporization process where surface atoms are physically ejected by momentum transfer from an energetic bombarding particle, which is usually a gaseous ion accelerated from a plasma.
3. Sputter deposition can be preformed in a vacuum or low-pressure gas (< 5 m Torr ) where the sputtered particles do not suffer gas phase collisions in the space between the target and the substrate or in a higher gas pressure ( 5- 30 m Torr ) where energetic particles sputtered or reflected from the sputtering target are “ thermalized ” by gas phase collisions before they reach the substrate surface.
Advantages of Sputter Deposition
1. Elements, alloys, and compounds can be sputtered and deposited.
2. The sputtering target provides a stable, long-lived vaporization source.
3. In some configurations the sputtering target provides a large area vaporization source that can be of any shape.
4. In some configurations the sputtering source can be a defined shape, such as a line or segment of a cone.
5. In some configurations reactive deposition can be easily accomplished using reactive gaseous species that are “activated” in a plasma ( i.e. “ reactive sputter deposition ”)
Disadvantages of Sputter Deposition
1. Sputtering rates are low compared to those that can be attained in thermal evaporation.
2. Film properties depend on the “ angle-of-incidence” of the flux of depositing material and at low pressures the amount of bombardment from high-energy neutrals reflected from the sputtering target.
3. In many configurations the deposition flux distribution is nonuniform, requiring fixturing to randomize the position of the substrates in order to obtain films of uniform thickness and properties.
4. Sputtering targets are often expensive, and material utilization may be poor.
5. In some configurations gaseous contamination is not easily removed from the system, and gaseous contaminations are “ activated” in the plasma, thus making film contamination more of a problem than in vacuum evaporation.
6. In some configurations radiation and bombardment from the plasma or sputtering target can degrade the substrate.
7. Sputter deposition is widely used to deposit thin-film metallization on semiconductor material, coatings on architectural glass, reflective coatings on compact discs, magnetic films, dry-film lubricants, and decorative coatings.
Sputtering Methods
DC Sputtering/MFSputtering
Balance Sputtering/Unbalaced Sputtering
Sputtering Coating System
Batch coaters and In-line sputtering coating system for Low-E, ITO film coatings on glass, PET film etc.
Royal Technology provides batch sputtering system, roll to roll sputtering metallization system, sputtering In-line system on glass etc. Please contact us with your demand.