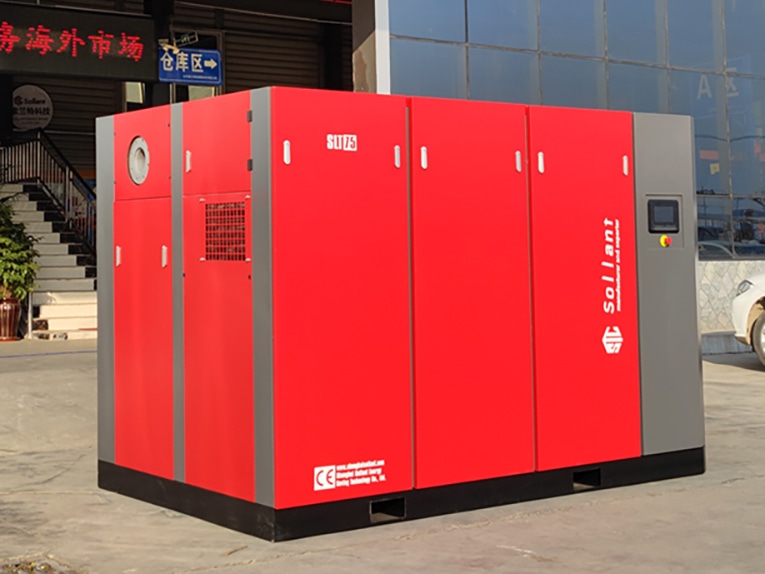
#Industry News
Air compressor maintenance and troubleshooting requirements
The requirements for finding the fault of the air compressor include:
① Make sure that the ground where the equipment is located is flat, and check whether the safety pin, block and parking brake are assembled in good condition.
②When two or more staff members operate together, they must strictly abide by the consensus and consistent signals, and keep unauthorized persons away.
③ Pay close attention not to touch any hot parts to avoid burns. Do not get caught by rotating parts.
④ When the wire is short-circuited, the negative terminal of the battery must be disassembled first.
⑤ When unscrewing the plug from the part under the pressure of oil, water or air, first remove the internal pressure and then remove it. When installing the measuring device, be sure to connect it properly.
⑥ The purpose of fault finding is to accurately find out the root cause of the fault, so as to deal with it quickly and prevent it from happening again.
In the process of finding the fault, the first thing is to understand its structure and function. But the simple and effective fault finding is to ask specific operators various questions, so as to know the possible causes of the fault.
1. In the process of finding the fault, do not rush to disassemble the parts
If the relevant parts are disassembled immediately after the failure is determined, the following problems may occur:
1) Parts that are not greatly related to the failure or other parts that do not need to be disassembled will be disassembled.
2) Cause new troubles to find out the cause of failure.
Random disassembly will also cause unnecessary waste of manpower and material resources, and it will also make users or operators lose confidence in identifying faults.
Therefore, it is necessary to conduct comprehensive research and analysis in advance when searching for faults, and then search for faults according to the prescribed procedures.
2. You can ask the user or operator the following questions
1) In addition to the problems mentioned in the report, have other problems occurred?
2) Before the fault occurs, is there any other abnormality in the air compressor?
3) Did the failure happen suddenly? Before that, was there any other problem with the operation of the air compressor?
4) Under what circumstances did the failure occur?
5) Was the fault repaired before? When was it repaired? How was it repaired?
6) Has a similar failure occurred before?
3. Checks that need to be carried out before finding the fault
1) Check all abnormal phenomena of the air compressor.
2) Refer to each item in "Inspection before start-up".
3) Other related inspection items.
4) Other maintenance items that can be checked from the outside and must be checked must be checked.
4. Confirm the fault
The maintenance personnel should confirm the scope of the fault, and judge whether to deal with it as an actual fault or as a problem of operation method.
Start the air compressor to allow the symptoms of failure to reappear, but do not perform any testing operations that may complicate the problem.
5. Troubleshooting
Use the analysis and inspection results of items 2 to 4 to narrow down the cause of the fault, and then use the fault lookup table (matrix) to determine and confirm the location of the fault.
Fault finding can refer to the following basic procedures:
1) Start relatively simple.
2) Start with the most frequent failure.
3) Analyze and study other related parts or information data.
6. Measures to eliminate the root cause of the failure
Even if the fault is fixed, the same problem will occur if the root cause of the fault is not removed. To prevent this from recurring, it is necessary to analyze why the problem occurred and then eliminate the root cause.