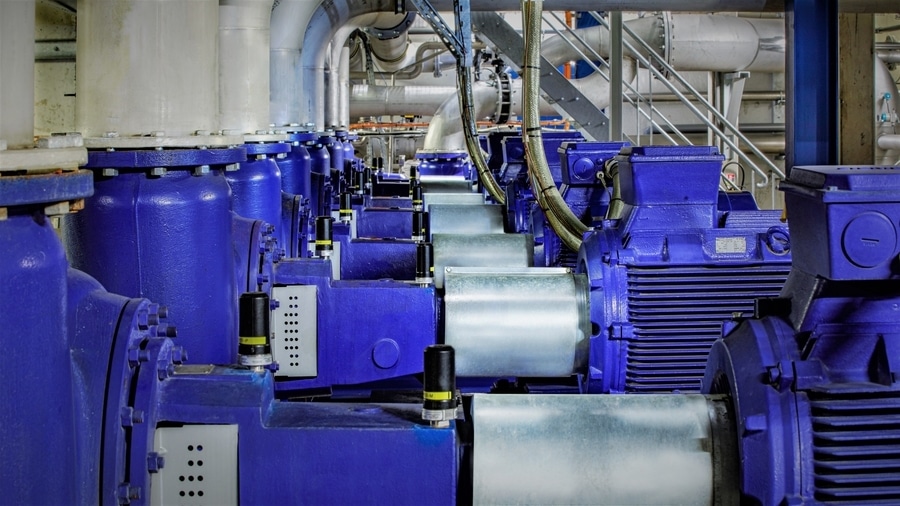
#Product Trends
Mechanical assets learn to speak
From Preventive to Predictive Maintenance
Continuous monitoring of machine condition can make operations safer and more efficient. Especially for critical components, condition-based or even predictive maintenance is the method of choice today: Modern, intelligent equipment transmits relevant condition parameters to higher-level maintenance management systems. But what about older assets without diagnostic capabilities? Here, a well-designed combination of IIoT sensors, gateway units and cloud services offers an ideal retrofit solution. In a process instrumentation and analytics manufacturing center, this package proves to be extremely cost-effective and versatile.
For decades, maintenance teams in process and manufacturing plants have strived to increase overall plant productivity. A key element of this effort is the development and implementation of effective maintenance strategies. The traditional approach of running equipment until it fails (known as "run to failure") has long been proven to be inefficient and costly. An important step in the development of more effective maintenance strategies has been the introduction of preventive maintenance (PM). This refers to routine maintenance and inspection activities that are performed according to defined schedules. However, while PM helps prevent unexpected failures, it also results in unnecessary maintenance when equipment is in good condition.
The next step in developing efficient maintenance strategies is Predictive Maintenance (PdM). This involves collecting and analyzing data on the condition of equipment to predict when maintenance may be required. The goal is to perform maintenance when it is needed, based on the actual condition of the equipment rather than on a set schedule. A key aspect of PdM is Condition-Based Monitoring (CBM), the continuous monitoring and analysis of the condition of equipment during normal operation. Successful implementation of condition-based maintenance requires a number of technologies and resources, including proper sensors, data transmission and processing systems, and specialized analysis software. Without these resources, it is impossible to perform maintenance based on current machine conditions. Retrofitting such technologies is now possible at low cost for rotating or vibrating equipment, as the following example illustrates.
Flowmeter manufacturing expertise
The Siemens factory in Haguenau, France, which celebrated its 50th anniversary in 2020, employs more than 800 people. Specializing in the production of pressure transmitters, flowmeters and gas analyzers, the plant has been recognized for its innovative approach to digital transformation: Since 2015, the facility has continuously optimized its production through automation, robotics and digitalization. Production processes can now be simulated in real time and made more efficient.
Here, Robert Gerber coordinates maintenance, while his colleague David Uhrig is responsible as a service planner. “In terms of maintenance, we have made great strides in recent years,” says Uhrig, who has worked at the Haguenau plant since 1995, first as a maintenance technician and then as a maintenance planner: “Our maintenance teams help ensure that the efficiency of the plants improves year after year. We monitor the production equipment around the clock and now benefit from diagnostic capabilities that the equipment did not have a few years ago. Maintenance strategies vary from plant section to plant section”, as Gerber reports: “I guess you could say, we are in the area of tension between wanting to do it and being able to do it on a daily basis: On the one hand, we know from criticality analyses which parts of the plant have which effects on operational performance in the event of a failure, and what we need to pay special attention to. On the other hand, we cannot develop predictive maintenance strategies for all assets because we lack the condition data.”
Spare parts are available for most critical equipment, but that is not enough to prevent downtime: “Take our autoclave, for example,” Gerber explains: “All flowmeters have a special inner lining that is vulcanized in the autoclave. If it fails, production stops. The motor for the autoclave blower is critical, so we keep it in stock. The problem with a sudden failure is that the fan wheel is mounted on the motor shaft without a coupling. It takes two days of work and the use of specialists, even though we have the spare part on stock.”
Condition-based monitoring for retrofitting
The two maintenance specialists wanted a condition-based monitoring option for this motor and found what they were looking for in-house: Sitrans Smart Condition Monitoring IQ (SCM IQ), developed by Siemens AG, is an intelligent system for continuous monitoring and maintenance of rotating or vibrating machine components. It uses a combination of IIoT sensors and artificial intelligence to continuously record and analyze vibration and temperature data.
Sitrans MS200 multisensors are mounted directly on the relevant plant components. They are rugged and have an IP 69 protected housing, ensuring safe operation under industrial conditions. There is no need to wire the battery-powered sensors, as the data is transmitted via Bluetooth Low Energy (BLE) to Sitrans CC220 gateways. These gateways collect the data from the multisensors and forward it to the cloud application. They are part of the deep internal system security measures that include end-to-end encryption from the sensor to the application level.
Sitrans SCM IQ App is the top-level cloud application. It uses artificial neural networks to continuously analyze the collected data and identify possible deviations from normal values. If such an anomaly is detected, indicating an impending failure, the system issues a warning. This early detection enables condition-based predictive maintenance, which ultimately leads to a significant improvement in plant performance.
“We are thrilled with the user-friendliness of the system,” says Uhrig, “it takes no more than an hour to install and commission the hardware.” His colleague Gerber adds: “Once that is done, the system takes care of itself: Within two to four weeks of operation, Sitrans SCM IQ learns the typical operating states of the monitored plant components. It uses this knowledge to detect anomalies and issue warnings. When an anomaly is detected, the responsible maintenance specialist receives a notification." In most cases, the anomaly is an early sign of a problem that is gradually becoming more serious. With this information, Uhrig, the service planner, can schedule his team and maintenance activities in advance: “Now I can book the right specialist to replace the fan motor for our autoclave and plan the replacement for a weekend. This means that production is not interrupted in any way.”
Calibration stands with integrated pump monitoring
Sitrans SCM IQ also plays a crucial role at another critical point in Haguenau's production, as Gerber explains: “Calibrating our flowmeters is an essential part of quality assurance during production and before delivery to the customer. This ensures that each instrument takes accurate measurements.” This step is done on highly specialized calibration stands designed to create accurate and repeatable conditions under which the flowmeters' measurement capabilities can be tested.
“Eight pumps for different flow rates play a crucial role for us,” Uhrig explains: “They are responsible for ensuring that the liquid flows through the meter at the specified rate. Since the accuracy of the calibration process depends heavily on the precision of the pump, we use highly exact and very reliable pumps, some of which cost as much as a mid-range car - we don't keep anything like that in stock. His colleague Gerber knows this from painful experience: “With such special pumps and prices, an unplanned failure is unfortunately a matter of several weeks, because even the pump manufacturers do not have these units in stock. Until they can deliver, a large part of our production is at a complete standstill, because we cannot deliver our equipment without calibration. In a situation like this, you're in the worst possible negotiating position.”
Until now, continuous condition-based or even predictive monitoring of the pumps was not possible. With great effort, the units were only checked once a year using mobile sensors. With Sitrans SCM IQ, this is now easily possible around the clock: “For example, by analyzing the vibration data, we can now detect an imbalance on the motor shaft or rotor at an early stage,” explains Maintenance Coordinator Gerber: “Over time, imbalances lead to increased vibrations and uneven running, which in turn lead to increased wear and ultimately motor failure. Today, our retrofitted condition-based maintenance system gives us very accurate information and notifies us of these signs of wear in a timely manner. This has taken our maintenance, spare parts management, and overall planning to a whole new, more efficient level.”
Sitrans SCM IQ is a complete solution that supplies an efficient, effective, and safe method of monitoring rotating or vibrating machine components, from data acquisition and analysis to prompt notification of maintenance actions. It gives the otherwise silent plant components a voice that can provide accurate information about their current condition.