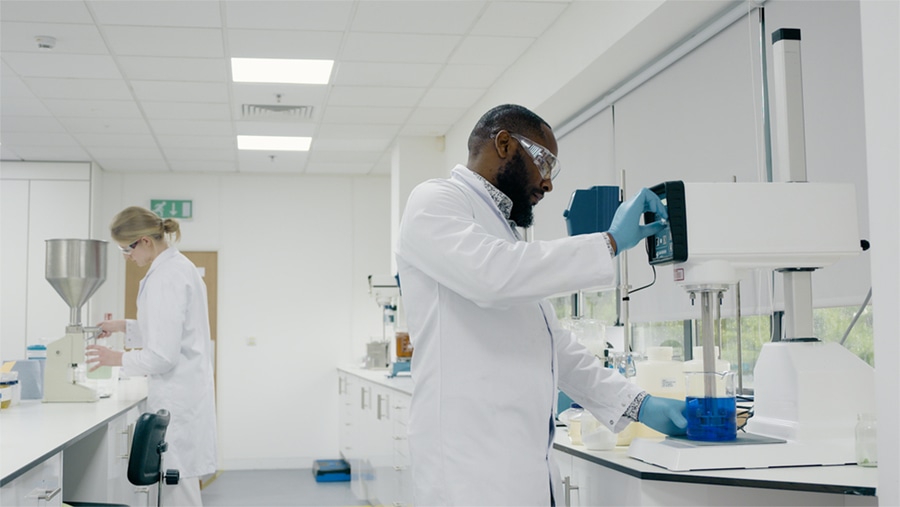
#Industry News
Manufacture of Shampoo & Personal Care Products using Silverson High Shear Mixers - with DCS Group
In the latest video on their YouTube channel, viewers can see how Silverson High Shear Mixers are used from the laboratory to the production floor at DCS Group.
The DCS group specialises in the manufacture of personal care products such as shampoos, shower gels, body lotions, body mists, and colognes on behalf of clients all over the world. At their manufacturing facility in the UK, they currently have a range of Silverson mixing equipment such as Silverson L5M-A Laboratory Mixers, which are used every day for their research and development work. Whilst on the production floor they have scaled up their applications and processes using Silverson In-Line mixers, Bottom Entry Mixers and Flashmix powder/liquid mixers.
The advantages of using high shear mixing equipment in their processes have enabled the DCS group to reduce mixing times, eliminate aeration, create stable suspensions and emulsions, achieve high viscosity mixes and increase capacity to up to 800,000 kilos per week. In this article, we explain how Silverson mixers have been able to achieve these results.
Eliminating Aeration
The high shear mixing/shearing action of the Silverson rotor/stator workhead sets up a circulatory pattern of mixing that is all below the liquid surface, minimising aeration. For completely aeration-free mixing, a Silverson In-Line mixer, along with the pipework and vessel form a closed system, and the flooded suction provided by the self-pumping In-Line mixer cannot introduce air into the product. This makes it ideal for the processing of aeration-sensitive products such as shampoos and detergents.
Using Silverson In-Line mixers and the set up detailed above has helped to mitigate an issue that the DCS group had been struggling with for a long time. Justice Manjowo, Process Development Lead at DCS, explains in the video the benefits of their Silverson system: "the time taken for mixing has been drastically shortened and we've seen a drastic decrease in aeration. We don't have to wait for product to de-aerate, it goes straight to the packaging lines" - saving time and helping to increase turnover and their manufacturing capacity.
Creating Stable Suspensions and Emulsions
When forming an emulsion, it is crucial to add the dispersed phase to the continuous phase correctly. While this might be less critical at laboratory scale, it becomes essential when dealing with larger volumes, a common problem when scaling up.
As explained in the video by Alexandra Jones, Technical Manager, at DCS, the DCS group have Silverson Laboratory mixers in their lab which they are used for the "preparation of difficult suspensions, [and] emulsions". On the production floor, as explained earlier, DCS use a number of Silverson In-Line mixers. As all Silverson mixers are built to the same tolerances, this simplifies the scale up process. Products can go from the lab to production without the need for reformulating. This is evident in the DCS groups processes, as Justice explains: "In terms of scale up, we found that it's actually quite flawless. The results that we get in the lab are similar, or very much similar, to those that we get when we actually do the [production scale] blending and mixing of our products."
Silverson In-Line mixers are ideal for the preparation of emulsions, including water-in-oil (W/O), oil-in-water (O/W), and water-in-oil-in-water (W/O/W) emulsions. Adding the dispersed phase just prior to the In-Line mixer will ensure an instant emulsion, maintaining uniformity and stability throughout the process.
Achieving High Viscosity Mixes
Silverson In-Line mixers are also capable of handling high viscosity products, such as creams and lotions, gels and SLES-surfactant based products. Alexandra explains: "Any kind of product that has really high viscosity, we're able to use these homogenisers to build really high viscosity and a fantastic appearance for our customers." The self-pumping In-Line mixers are able to do this without the need for additional processing equipment, such as centrifugal pumps.
Increasing Production Capacity
Adding a Silverson In-Line mixer to an existing process can reduce mixing times by up to 90 percent, allowing users to substantially increase productivity without the need for additional vessels or other capital equipment. As explained earlier, DCS have obtained further savings by eliminating aeration; finished products can be sent straight from processing to the packaging lines, saving time. As Alexandra explains in the video: "We are currently manufacturing anywhere between 400,000 to 800,000 kilos a week. What we've been able to do with Silverson is increase our capacity to be able to achieve a really high quality cosmetic product, without that, we wouldn't be able to achieve the turnover."
You can watch the video on the Silverson YouTube channel. If you want to find out more about how Silverson has helped customers in the cosmetics, and other, industries, a range of Case Studies are available on the Silverson website.