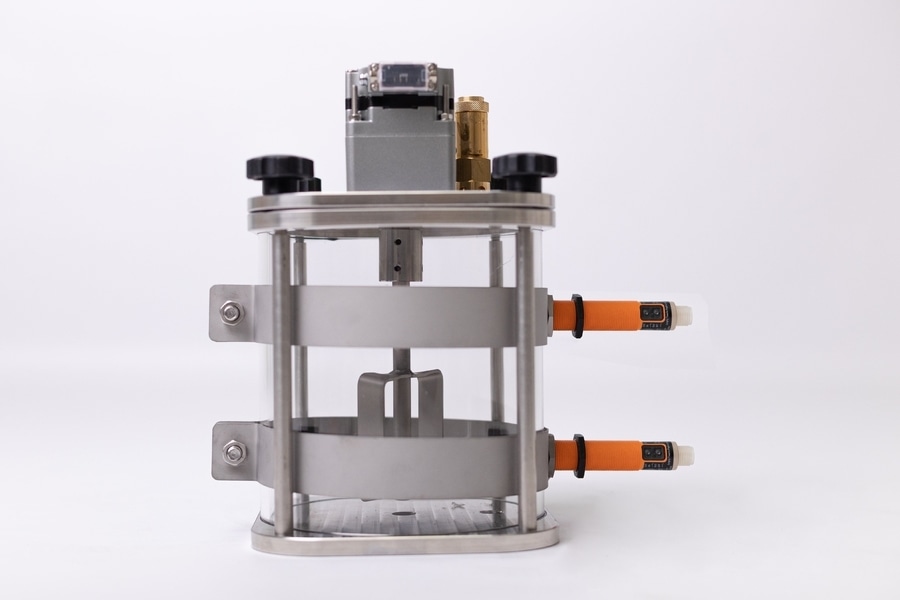
#Product Trends
Creating new production processes with Compagnons du Devoir
Cutting the cost of biomedical fluid production
The Compagnons du Devoir et du Tour de France is one of the world’s oldest craftsperson and artisan organisations. Similar to the German Wandergesellen, or journeymen, engineering apprentices are required to tour France learning from masters in their trade. Now expanded to include more than 49 countries across five continents, to take part apprentices need a Certificat d’aptitude professionelle, equivalent to an NVQ Level 2 or 3 in the UK.
We were tasked with helping engineering masters and apprentices to develop a full production system that would convert raw materials into a biomedical fluid. The system could be purchased from laboratory equipment suppliers or healthcare and pharmaceutical based businesses but would cost in excess of £30,000. The engineering challenge was to design the same system from scratch at a much lower cost, in order to produce the same if not better results.
To develop the production process from scratch the Compagnons du Devoir engineers needed to design the system, identify key hardware and liaise with suppliers and create the necessary automation and programming needed to create this highly complex biomedical fluid. The solution included a three stage mixing process, coupled with a heating stage and final holding stage during which the fluid is kept under constant motion to maintain consistency ready for dispensing.
Working with the Compagnons du Devoir engineers we identified that three 2000ML-CTEL transparent pressure vessels would be the best option for their application, as not only does it provide a controlled environment for the fluid, but also allows for visual checks that ensure any minute changes in the chemical composition can be identified and corrected quickly and effectively.
The raw chemicals are firstly fed into the first transparent pressure vessel which is equipped with an SR-TEK electric Motor & Controller and Anchor Blade Mixer. The automated process developed by the Compagnons du Devoir engineers enables the precise variation in mixing at different times to help produce the desired outcome. The flexibility offered by this kind of setup is particularly appreciated by R&D teams when trying to develop new polymers or fluids, as it allows for experimentation and knowledge of which of the variables need to be fixed to create the desired result.
Once fully mixed the fluid travels via piping to a second two-litre CTEL transparent pressure vessel, equipped with a Single Blade Mixer, designed to keep the fluid in motion to ensure that it stays homogenous. It’s at this stage that heat is applied to further the polymerisation of the materials.
Once processed the fluid is then sent to a final holding vessel equipped with another Anchor Blade Mixer from which it is dispensed. Interestingly all three tanks are equipped with two high and low Capacitive Level Sensors that when linked to the Programmable Logic Controller (PLC) ensures the whole process can be automated.
The level of control offered by this type of system is becoming increasingly popular with R&D departments as it means that variables determined and fixed in the lab can be scaled and replicated in production. Everything becomes a science, a recipe that can be take and applied to any company and environment in the world to produce the same result.
The total cost of the complete system was a third of the ready-made commercially available alternative. As an added benefit Compagnons du Devoir et du Tour de France engineers now have production quality components that can be reused and adapted for future research projects many times over, rather than a single purpose piece of machinery.
Transparent pressure vessels are becoming increasingly popular amongst university and research teams, as they allow for clear demonstration of the processes involved and complete control over the interior environment.
To find out more about working with SR-TEK or to discuss your latest application needs contact SR-TEK founder Loris Medart on 0044 (0) 20 8242 4853 / loris@sr-tek.com.