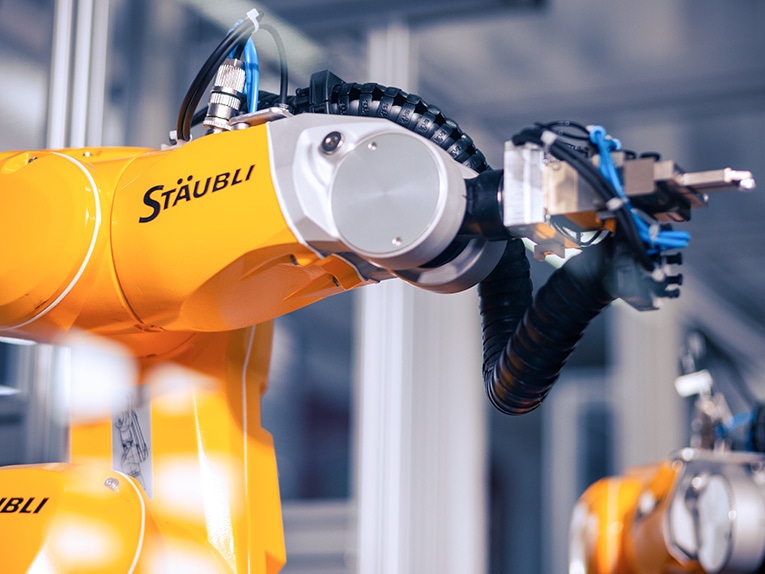
#Product Trends
Ultra-flexible high-precision assembly
Mobile robot modules for new levels of versatility
Zero-defect assembly of electrical connectors in the tolerance range of 20 to 30 mm places enormous demands on automation, especially when batch sizes can fluctuate between 20,000 and 2,000,000 units. The pioneering use of mobile robot modules offers the perfect solution.
CUSTOMER BENEFITS
Exceptional level of flexibility
Zero-defect assembly
Low maintenance
Rapid changeover
Future-proof investment
TASK
Highly flexible assembly of electrical connectors
At its factory in Weil am Rhein, Germany, Stäubli Electrical Connectors is demonstrating how unprecedented flexibility can be achieved in series production. The solution is a groundbreaking system in which mobile assembly modules equipped with robots can be docked onto the production line in less than a minute. And it doesn’t stop there.
Realizing such a novel assembly line called for considerable creativity and expertise. In it, sockets and plugs are fitted with Stäubli’s patented MULTILAM contact element in a multitude of variants. MULTILAM technology exemplifies the highest standards of quality and reliability in electrical connector manufacturing. In a production context, it means robot-supported zero-defect precision assembly in the tolerance range of 20 to 30 mm for widely fluctuating batch sizes of 20,000 to 2,000,000 units.
Identifying suitable robots for this high-precision assembly work was easy, as the most accurate machines on the market are made by Stäubli itself. Five of them (four six-axis TX2-40s and one TS2-40 SCARA) now operate in the assembly plant in Weil am Rhein.
Initially there was skepticism about docking mobile assembly modules with robots onto the line within a minute and starting assembly without calibrating the robot or making other adjustments. Many said it was impossible. Then Stäubli delivered proof. John Dallapiccola, Managing Director Stäubli Electrical Connectors Weil am Rhein: “The concept of this unique system is based on the use of synergies within the Stäubli Group. We have our own precision robots and innovative interface solutions, which in this case were key to realizing it. And, of course, we had a brilliant idea.”
SOLUTION
An advanced concept
Crucial to making this advanced concept a reality was the ability to dock the mobile modules onto the line with precision down to one hundredth of a millimeter. The time factor also played a pivotal role. The specification was to position the module manually, center it automatically, lock it in place, and set it to work. Within a few seconds, the power and compressed air supply for all components must start to flow.
This is where the CombiTac modular connector from Stäubli Electrical Connectors comes in, connecting all energy and media circuits in sync with the docking process. High-precision guides and a pneumatically actuated quick coupling from Stäubli Fluid Connectors ensure that the mobile module fits onto the assembly line correctly.
The complete assembly line consists of 12 modules linked to each other by means of a linear transport system. There are part-specific fixtures on 20 “movers,” which the first two Stäubli six-axis robots on modules 1 and 2 equip with a MULTILAM and, depending on the variant to be produced, a plug or socket.
The components then reach the processing station, where the MULTILAM is married to the socket or plug. Depending on the variant, further steps follow. If, for example, a socket ring has to be fitted, this task is performed by an ultra-compact Stäubli TS2-40 SCARA, which operates with impressive precision and dynamics.
CUSTOMER USAGE
A high level of versatility and quality
Ensuring product quality is one of this production line’s most important tasks. Each connector undergoes 100% quality control including a mating force test and camera-based final inspection. The handling of completed parts at this pass/fail station is the task of another Stäubli TX2-60 six-axis robot, whose high dynamics ensure compliance with the specified cycle time.
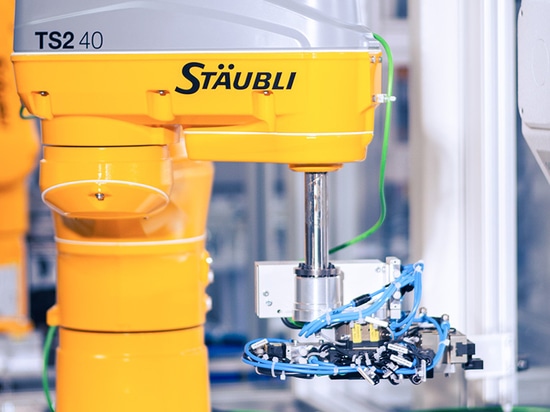
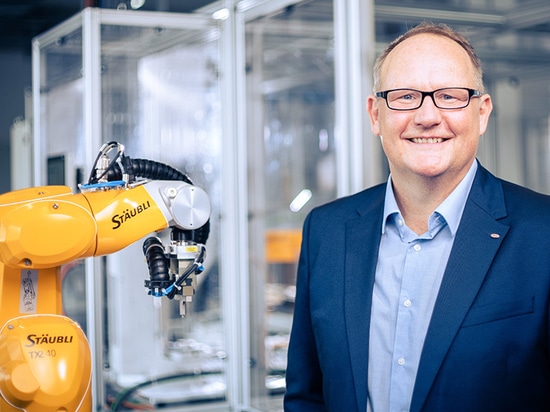

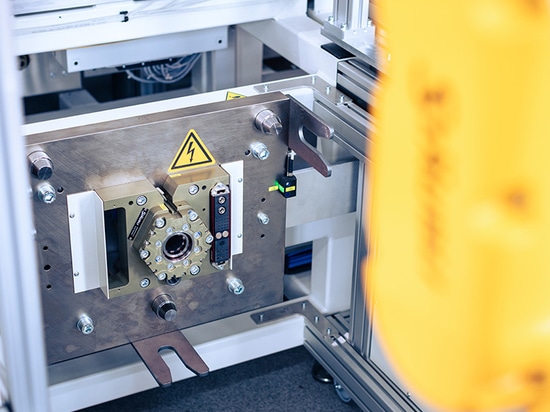
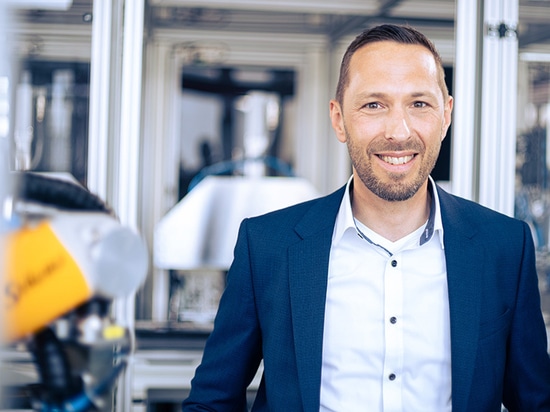