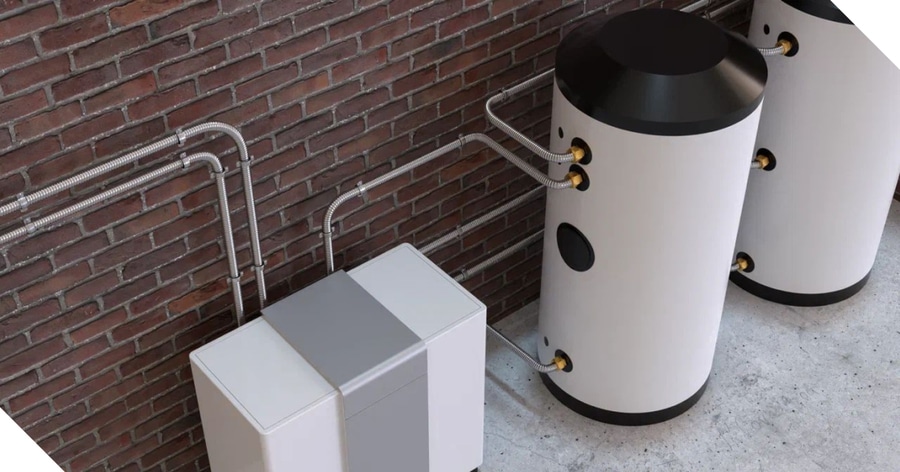
#Industry News
Stahlmann Corrugated Stainless Steel Tubes vs. Polyethylene Tubes
Comparing Characteristics and Determining the Leader for Use in Utility Systems
Quality, reliability and longevity are key considerations in the selection of components to be installed. Particular attention should be paid when purchasing tubes used for underfloor heating, hot and cold water supply, fire extinguishing, gas, electrical and communications networks.
In this article, we will review the advantages of common tube types for the above applications and identify the most versatile and reliable solution.
Tube types and their peculiar properties
1. Cross-linked polyethylene tubes (PE-X)
This high-tech material is made from an organic polymer of ethylene and is produced by molecular cross-linking.
There are four types of cross-linking: PE-Xa, PE-Xb, PE-Xc, PE-Xd, with PE-Xa being the most technologically advanced. These tubes are resistant to stress and have increased elasticity. When unwound, the coils straighten quickly and retain their shape well. They do not wrinkle when bent (within the permissible limits and in accordance with the technology).
2. Tubes of polyethylene of raised temperature resistance materials (PE-RT)
They are based on conventional polyethylene with high temperature additives. It has properties similar to those of PE-X. These tubes are inert to chemical reagents and are not susceptible to corrosion. Due to the lack of cross-linking, they have high temperature resistance, flexibility, plasticity and increased hydrostaticity.
3. Corrugated stainless steel tubes
Stahlmann tubes are made of 304 stainless steel. This metal has high corrosion resistance and is unaffected by a wide range of aggressive media. Harder and stronger than carbon steel, aluminium, brass and bronze, it is also highly flexible, bends well and has improved weldability.
Comparison of key thermophysical properties of the 3 tube types
To help you understand what characteristics to look for, below we describe the main indicators, explain what they are for, and provide data for three common tube types used in utility systems.
● Maximum operating temperature
This is extremely important to consider, as all tubes used in heating systems must be able to withstand the temperature of the fluid flowing through them without deformation.
For example, the average water temperature in a central heating system is 90°C. At the same time, the tubes must be able to withstand overheating above the standard 105°C.
Maximum operating temperature of the 3 tube types compared:
- PE-Xa tube Ø16 mm — 90 °С;
- PE-RT tube Ø16 mm — 70 °С;
- Corrugated tube Stahlmann — 150 °С.
Corrugated tube is therefore better suited to hot water, as it is not afraid of high temperatures, making it ideal for boilers and heating systems.
An important feature of corrugated tube systems is their ability to withstand freeze and thaw conditions. Installation can be carried out in temperatures as low as -10°C on sites without electrification. This reduces installation time by 40% and speeds up commissioning.
● Maximum short-term temperature
Short-term fluctuations in the temperature of the heat carrier will not cause tube failure in most cases. However, temperatures above 100°C will significantly reduce the service life of polyethylene tube, which has a melting point of 140°C.
Maximum short-term temperature of the 3 tube types compared:
- PE-Xa tube Ø16 mm — 100 °С;
- PE-RT tube Ø16 mm — 95 °С;
- Corrugated tube Stahlmann — 400 °С.
The corrugated steel tube exceeds the thermal resistance limit of polyethylene tubes by 4 times and can easily withstand any temperature of the heat carrier used in residential and industrial premises.
● Heat transfer coefficient
It shows how much heat is transferred per 1 meter of tube surface in 1 second. Obviously, the heat transfer rate of metal tubes is higher than that of polyethylene tubes, but they have their own advantages.
Heat transfer coefficient of the 3 tube types compared:
- PE-Xa tube Ø16 mm — 0.41 W/m·K;
- PE-RT tube Ø16 mm — 0.4 W/m·K;
- Corrugated tube Stahlmann — 17 W/m·K.
The larger inner diameter of the corrugated tube, with a corrugated wall thickness of 0.3mm, provides a maximum heat transfer area that is 20% higher than that of polyethylene tubes. This means that the corrugated tube can be laid at greater intervals, which helps to save on both material and labour costs.
The heat output of corrugated tube is 20% higher than that of polyethylene tube, so it is possible to increase the tube spacing for underfloor heating from 0.15 m to 0.2 m. This saves 17 running meters of tube for 10 m2 and 170 running meters for 100 m2 with the same heat output.
The corrugated tube also heats the screed more quickly. This makes the system more responsive to set points when programmable thermostats are used.
● Coefficient of linear expansion of 100 m of tube at heat carrier temperature of 50°C
The coefficient is relevant to hot water piping and heating systems. It indicates how much the tube length increases when heated to 50°C and decreases when cooled.
● Coefficient of linear expansion of 100 m of tube at heat carrier temperature of 50°C of the 3 tube types compared:
- PE-Xa tube Ø16 mm — 1000 mm;
- PE-RT tube Ø16 mm — 1000 mm;
- Corrugated tube Stahlmann — 55 mm.
For corrugated tube, the coefficient is 18 times smaller: a 100-meter polyethylene tube can expand up to 1 m, whereas a corrugated steel tube only expands 5.5 cm.
This parameter is particularly important in screed installations, where the significant expansion of the tube and friction against the screed will break its oxygen barrier. There have been real cases of PEX being fixed to steel grids with ties, causing holes in the tube.
Comparison of the main physical properties of the 3 tube types
● Maximum working pressure
It depends directly on the heat carrier temperature: the higher the temperature, the lower the pressure in the tube.
There is another dependency here: the larger the internal diameter of the tube, the lower the resulting pressure. At the point where the tube narrows, there is a sudden spike in pressure as the same volume of water starts to flow through the smaller diameter.
Maximum working pressure of the 3 types of tubes compared:
- PE-Xa tube Ø16 mm with 2.2 mm wall thickness — 10 bar at 90 °C;
- PE-RT tube Ø16 mm with 2.2 mm wall thickness — 12.5 bar at 20 °C and 5.4 bar at 95 °C;
- Corrugated tube Stahlmann — 15 bar.
We can see that the working pressure of corrugated tubes is 50% higher than that of polyethylene tubes. This provides a huge safety margin in operation and protects against sudden leaks.
● Oxygen permeability
This is important because oxygen easily penetrates the walls of polyethylene tubes, saturating the hot water inside. Oxygen causes rusting when it comes into contact with metal parts. This reduces the life of connected equipment and assemblies by up to 3-5 years.
The EVOH anti-diffusion layer reduces the oxygen permeability of polyethylene tubes. This prevents the ingress of oxygen into the water and therefore prevents corrosion.
PE-Xa and PE-RT tubes are also available with an oxygen barrier, but PE-RT tubes are more common without one. In this case, some manufacturers state the following: "If there are no restrictions on the content of dissolved oxygen in the heat carrier, it is possible to use it in water underfloor heating systems..." But remember: This is just a marketing ploy.
According to international standards, the oxygen permeability of tubes designed for service classes 4 and 5 should not exceed 0.1 g/m3*day.
Oxygen permeability of the 3 tube types compared:
- PE-Xa tube Ø16 mm — <0.1 g/m3*day for tube with oxygen barrier, 9 g/m3*day without oxygen barrier;
- PE-RT tube Ø16 mm — <0.1 g/m3*day for tube with oxygen barrier, >0.1 g/m3*day for tube without oxygen barrier;
- Corrugated tube Stahlmann — complete oxygen impermeability.
All three samples meet the standard. However, the zero oxygen permeability of the corrugated tube prevents corrosion. Additional corrosion protection is provided by a chromium oxide film. This combination of properties significantly increases the service life of the entire system, including steel radiators and other components.
● Minimum bending radius for Ø16 mm
Installing complex pipework often involves bending the tube. In underfloor heating systems that are laid in a ‘serpentine’ or ‘snail’ pattern, the ability of the tubes to bend is extremely important.
The most common way to bend the tubes is to either bend them or to fit an elbow fitting. The second method saves space but has more connections that increases the risk of leaks.
Therefore, the smaller the minimum bending radius, the more options you have to install utilities in a convenient and compact way.
Minimum bending radius of the 3 tube types compared:
- PE-Xa tube Ø16 mm — 80 mm;
- PE-RT tube Ø16 mm — 80 mm;
- Corrugated tube Stahlmann — 40 mm.
We can see that the corrugated tube has the smallest bending radius without changing the cross section. This makes it possible to install complex pipelines of any configuration without worrying about damage or bursting during operation.
Stahlmann corrugated tubes are easy to bend by hand, without changing the cross-section of the bore, so that complex tube layouts can be created with a minimum number of fittings.
● Plasticity when bending below minimum bend radius
Sometimes it is necessary to bend the tube tighter than the minimum bending radius. This is where the plasticity of the tube provided by the manufacturer comes in useful.
Bending plasticity of 3 tube types compared below the minimum bending radius:
- PE-Xa tube Ø16 mm — bending causes buckling, the shape of the tube can be restored by heating with a heat gun;
- PE-RT tube Ø16 mm — flattening and buckling of the tube are not allowed;
- Corrugated tube Stahlmann — can withstand up to 40 bends with no change in tightness or cross section (for annealed tube).
Unlike polyethylene tubes, corrugated tubes hold their shape and are easy to install. It is almost impossible to damage them during installation and installation errors are impossible. In comparison, a PE-Xa tube will break under heavy bending.
Manufacturer's warranty, service life and applications
● Service life of the 3 tube types compared when operating conditions are met:
- PE-Xa tube Ø16 mm — 50 years in total (grade 5): 14 years at 20 °C, 25 years at 60 °C, 10 years at 80 °C, 1 year at 90 °C, 100 hours at 100 °C;
- PE-RT tube Ø16 mm — 50 years in total (grade 5): 14 years at 20 °C, 25 years at 60 °C, 10 years at 80 °C, 1 year at 90 °C, 100 hours at 100 °C;
- Corrugated tube Stahlmann — minimum 30 years.
At first glance, a 50-year service life for polyethylene tubes is good, but there is a nuance. The total service life of the tubes is significantly reduced when the temperature or pressure increases. The actual service life of corrugated tubes is therefore 2 times longer than that of polyethylene tubes.
● Manufacturer's warranty for 3 tube types compared:
- PE-Xa tube Ø16 mm — 10 years (Valtec), 5 years (Rehau);
- PE-RT tube Ø16 mm — 10 years (Valtec);
- Corrugated tube Stahlmann — lifetime warranty.
To make the comparison most objective, we considered the maximum warranty periods of the polyethylene tubes on the market. As Stahlmann corrugated tubes have a service life of 30 years and longer, the manufacturer offers a corresponding warranty.
● Application area of the 3 tube types compared:
- PE-Xa tube Ø16 mm — water underfloor heating, radiator heating, hot and cold water supply;
- PE-RT tube Ø16 mm — water underfloor heating, hot and cold water supply;
- Corrugated tube Stahlmann — water underfloor heating, radiator heating, hot and cold water supply, solar systems, fire extinguishing, gas supply, cable conduits, ventilation.
Water underfloor heating, radiator heating, hot and cold water supply, solar systems, fire extinguishing, gas systems, cable conduits, air conditioning and ventilation — it would be hard to imagine a more diverse range of applications for steel tubes. Stahlmann corrugated tubes perform equally well in each of these areas.
Steel corrugated tubes are not only resistant to corrosion and water hammer. They are also not exposed to the formation of deposits! Compared to smooth wall tubes, corrugated tubes create a swirling flow that prevents biofilm from building up on the walls.
Unlike polyethylene tubes, Stahlmann corrugated tubes are available in coils of 10, 20, 30, 50 and 100 meters. Maximum length coils allow underfloor heating loops, extended pipework or cable conduits to be installed without a single joint.
In conclusion
Having compared all the key characteristics of cross-linked polyethylene, high temperature polyethylene and stainless steel corrugated tubes, we can confidently say that steel tubes are superior to polyethylene tubes in almost every respect.
Functionality, reliability, versatility and a lifetime warranty make them the market leader in the field of technical installation solutions. For the complete range of Stahlmann corrugated tubes and accessories, please visit http://www.warm-on.com
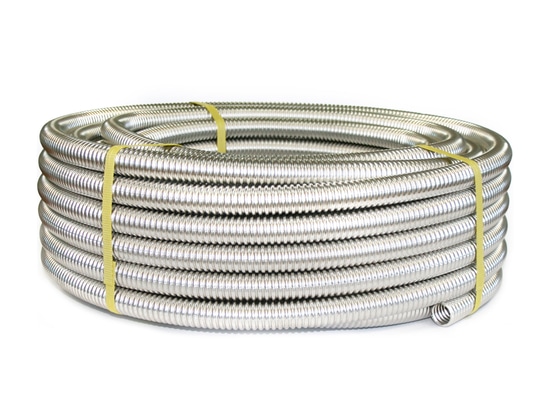