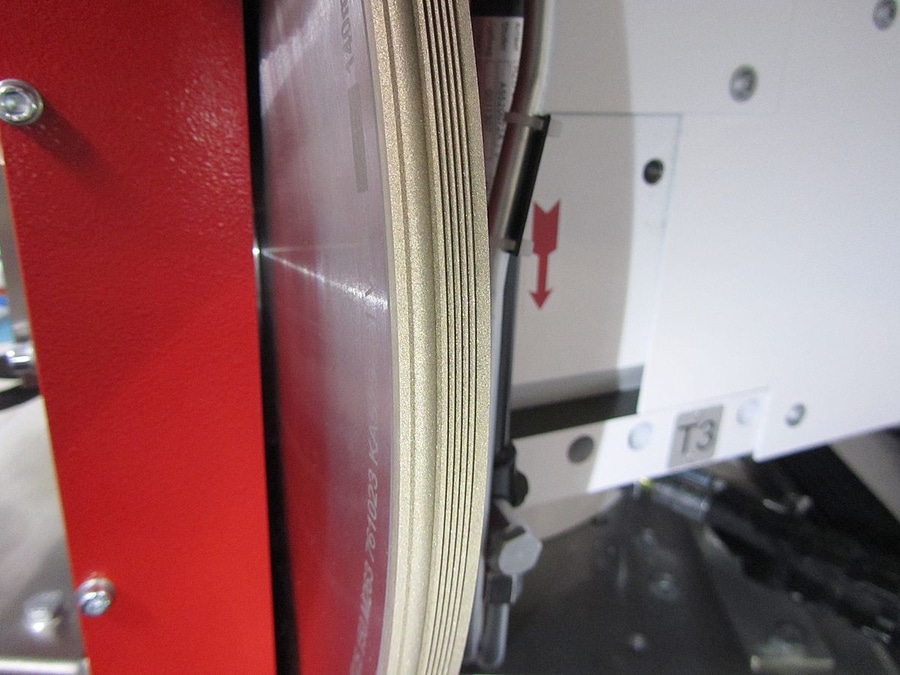
#Product Trends
Dressing metal-bonded grinding wheels efficiently in the grinding machine
The integrated electro-discharge dressing technology WireDress® opens up brand new possibilities for grinding with metal-bonded grinding wheels and drastically cuts auxiliary times. According to Fritz Studer AG, it has been possible to increase grinding power in the grinding process by 30% and reduce grinding wheel wear by 70% in comparison with ceramic and resin bonds. Grinding wheels with very intricate contours can also be dressed.
Metal-bonded grinding wheels offer particular benefits when machining difficult-to-machine materials such as high-alloy, hardened steels, tungsten carbides and ceramics. Such wheels offer superior dimensional and thermal stability and dissipate the heat produced by grinding more quickly. The grinding wheels consist of a sintered metal matrix with embedded diamond or CBN grains (CBN = Cubic Crystalline Boron Nitride). They achieve very high removal rates, because the metal bond holds the abrasive grains very well.
Particularly effective: electro-discharge dressing
However, in addition to the advantages of metal bonds there are also disadvantages, as dressing these wheels involves greater expense and effort. Dressing with silicon carbide wheels, for example, often does not achieve satisfactory results, and intricate profiles are not possible. In addition, the grains are difficult to mechanically extract from the metal matrix and are sometimes damaged in the process. It is also not possible to create the high grain protrusion heights necessary to achieve the full efficiency of such grinding wheels. The extremely hard abrasive grains of metal-bonded grinding wheels also lead to heavy wear of the dressing wheels, which results in certain limitations in terms of geometrical precision.
Experts see alternatives in electrochemical (ECM) and electro-discharge (EDM) dressing processes, for example. Both create grains with high protrusion heights and operate without contact. However, electrical discharge dressing processes do not require any chemically active liquid to remove the metal bond.
Electrical discharge dressing processes use the basic principle of EDM electrical discharge machines (EDM = electrical discharge machining), which have been used for precision machining for many years. As with these machines, the material is removed without contact by extremely short direct current pulses following each other in quick succession, which generate a discharge in the gap between electrode and workpiece in the dielectric. During the discharge tiny areas of the metal bond of the grinding wheel are melted and flushed out of the gap as small particles by the dielectric medium.
External dressing machines are sometimes used for dressing metal-bonded grinding wheels. The grinding wheels have to be removed from the grinding machine, transported to the dressing machine and, after return transport, mounted on the grinding machine and set up again. It is very difficult to achieve micron precision using this method. Moreover, the handling and logistics effort involved, with its time and cost disadvantages, makes machine-integrated dressing systems appear very advantageous.
Integrated dressing with wire erosion
With STUDER-WireDress® Fritz Studer AG brings a brand new dressing device to the market, which uses the wire erosion principle and is completely integrated into the grinding machine and its control system. The grinding wheel never has to be removed for dressing. Thanks to the high proportion of grain space, the wheel is very free cutting. This allows much more grinding oil to enter the grinding slot, enabling a high feed with less workpiece deflection. The dressing intervals can be longer. However, as the dressing process requires so little expense and effort, very complex contours can also be dressed at shorter intervals. As the user can fully utilize the advantages of metal-bonded grinding wheels during rough and fine grinding, the STUDER-WireDress® dressing system pays for itself in less than a year.
The dressing device is a small wire erosion machine in principle. The electrode is a wire, which is drawn with a small gap tangentially past the machining point at a constant speed of 100 millimeters per second. The opposite pole is the grinding wheel, which moves at peripheral speeds of 50 to 140 meters per second during dressing. It does not need any dielectric, as the grinding oil used during grinding fulfills this function. The dressing wire is guided in a groove on the circumference of a thin, circular ceramic disk. The ceramic disk has a notch at the point where the sparks jump between the wire and the grinding wheel.
Feeds of 15 to 25 mm/min can be achieved when dressing a typical metal bond. In this way largely free geometries and intricate contours with internal radii of 0.2 millimeters and external radii of 0.05 millimeters are generated on the grinding wheel. Removal rates of up to 80 mm3/min are achieved. The grain retains its original shape during this contactless dressing process.
No wear on the dressing tool
As the wire is continuously advanced during the dressing process, an electrode with precise geometry is always located at the dressing position.
The wire reel in the dressing unit contains ten kilometers of wire; this supply would allow dressing to be continued for approx. 16 hours without interruption. The used wire is cut into short pieces immediately after the dressing process and collected in a container. The ceramic disk which guides the electrode wire is very resistant and only wears after several hundred hours. The circumference of the disk has three of the abovementioned notches; if necessary it is simply turned further round by one of the three segments and an intact wire guide is available again.
Control unit integrated into the grinding machine control system
The STUDER-WireDress® control unit is integrated into the control system of the grinding machine. It has all necessary dressing functionalities and also contains a software program for intelligent profiling with path optimization (StuderDress integrated). The grinder does not need any special training for operating the dressing device, as he is guided by the clear and transparent guidelines on the screen of the control unit.
The new development also brings significant energy savings as part of the Blue Competence measures at STUDER: it only needs around 500 watts during dressing, and just 25 watts during the standby phases. For comparison: rotary dressing with diamond wheels uses 1.5 kilowatts; the energy required for the provision of sealing air, which is constantly necessary, is 1 kilowatt.
The development of the WireDress® technology from basic research through testing to industrial product in 7 years was also carried out on the S22. This is a production platform for the mass production of medium-sized workpieces. It enables machining operations such as cylindrical grinding, form and thread grinding, heavy-duty applications with 160 mm wide grinding wheels or high speed grinding (HSG) with cutting speeds up to 140 m/s. STUDER-WireDress® is also available on the S31 and S41 CNC universal cylindrical grinding machines.
In the Fritz Studer AG Technology Center all new developments are subjected to tests under rigorous production conditions, often over a number of years. Improvements and optimizations resulting from practical use are implemented on the new developments in this phase. So-called "teething troubles" are then eliminated, so that the customer is presented with sophisticated, fully operational machines at market launch.
New possibilities - higher productivity - highest precision with STUDER-WireDress®.