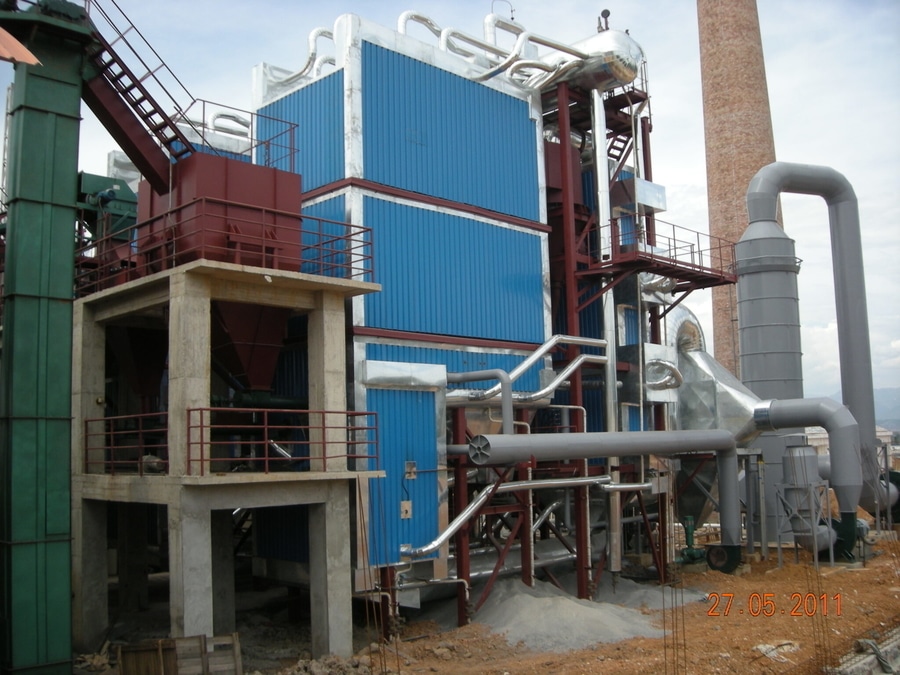
#Industry News
Biomass Fuel Boiler Operation and Monitoring: Ensuring Efficiency and Reliability
Best Practices for Operational Procedures, Maintenance, and Safety in Biomass Boiler Systems
Introduction to Biomass Boilers
Biomass fuel boilers, also known as biomass heating systems, are an eco-friendly solution that harness renewable biofuels to generate heat and hot water. These biofuels—such as wood pellets, chips, and logs—provide a cost-effective and sustainable alternative to fossil fuels like electricity, oil, and gas. Biomass boilers are widely recognized for their environmental benefits, including reducing carbon dioxide (CO₂) and nitrogen oxides (NOx) emissions. In addition to their environmental advantages, biomass boilers offer economic benefits by helping businesses lower energy costs and reduce dependence on conventional energy sources.
Types of Biomass Fuel
Biomass fuels come in a variety of forms, each suitable for different boiler systems. Common fuels include:
Wood Logs: Requires manual loading but offers a natural source of renewable energy.
Wood Chips: Can be automatically fed into the furnace, making it ideal for continuous operation.
Wood Pellets: Similar to wood chips but more compact and consistent in size, ensuring efficient combustion.
Agricultural Waste: Residues from crops such as straw, bagasse, and rice husks.
Animal Byproducts: Organic waste like poultry litter, which can be processed for fuel.
Household Waste: Recycled organic materials from homes and businesses.
While wood pellets and chips allow for automatic feeding, logs typically require manual handling, adding a labor component to the system.
Biomass is known for being environmentally friendly because it produces minimal pollution during combustion, making it a preferred choice for businesses and industries looking to reduce their carbon footprint.
Key Operational Procedures for Biomass Boilers
To ensure that biomass boilers operate at their optimal efficiency and safety, operators must follow a series of key operational procedures.
1. Boiler Operation Adjustment
Evaporation Rate: Monitor the evaporation rate to align with the steam turbine’s requirements.
Steam Pressure & Temperature: Ensure stable steam pressure, temperature, and water levels, adjusting as necessary for efficient operation.
Combustion Optimization: Adjust combustion parameters for improved fuel efficiency and lower emissions.
2. Water Level Control
Washing the Water Gauge: Open the blowdown valve and clean the steam and water pipes to ensure accurate water level readings. Perform this process carefully to prevent any risk of injury.
Water Level Adjustment: Maintain the water level within acceptable limits, adjusting to ensure stability and avoid overfilling.
3. Steam Pressure and Temperature Management
Steam Pressure: Maintain the rated steam pressure at 4.1 MPa, with fluctuations not exceeding ±0.05 MPa.
Steam Temperature: Ensure the steam temperature remains at 385°C, with a tolerance range of ±5-10°C.
Combustion Intensity: Adjust combustion intensity gradually to stabilize steam parameters, avoiding abrupt changes.
4. Combustion Adjustment
Regulate fuel input and air supply based on changes in load. Ensure the fire spreads uniformly across the furnace and that oxygen levels are kept between 4-6%. This ensures efficient combustion and minimizes risks of coking.
5. Boiler Blowdown Process
The blowdown process helps to manage the concentration of salts and other impurities in the boiler water.
Continuous Blowdown: Removes high-salinity water to prevent scaling.
Intermittent Blowdown: Removes sediment to maintain water wall cleanliness.
Ensure blowdown is done with caution to avoid sudden pressure changes or water hammer. Perform blowdown only when the water level is at a safe level.
6. Rotating Machinery Maintenance
Vibration and Noise Monitoring: Check for abnormal vibrations or sounds in rotating machinery.
Lubrication: Ensure regular lubrication of bearings and check oil levels frequently.
Temperature Monitoring: Keep bearings under 80°C and check for adequate cooling water flow.
7. Operating and Maintenance of Slag Conveyor
Ensure proper maintenance of the slag conveyor, such as checking motor temperature and oil levels. Avoid any reverse operation to prevent malfunctioning.
8. Maintenance of Slag Belt Conveyor
Ensure the rollers are aligned, lubricate moving parts, and ensure smooth rotation. Check temperature and condition of motors and bearings, and monitor the transmission belt for wear.
9. Operating and Maintenance of Biomass Fuel Boiler
Biomass fuel boilers require regular inspections of pressurized parts, valves, explosion-proof doors, and other structural components. Operators should follow the maintenance schedule for regular testing and inspections, ensuring logs are accurately recorded. The operation area should remain clean to ensure safety and operational efficiency.
Conclusion
Proper operation and maintenance of biomass fuel boilers are essential to ensure their longevity, safety, and efficiency. Regular monitoring of key parameters such as water levels, steam pressure, and combustion efficiency allows operators to optimize boiler performance and reduce operational costs. By following the outlined procedures, businesses can achieve a reliable, cost-effective, and environmentally friendly energy solution. As biomass boilers continue to play a crucial role in sustainable energy production, adopting best practices in their operation and maintenance is key to maximizing their benefits.
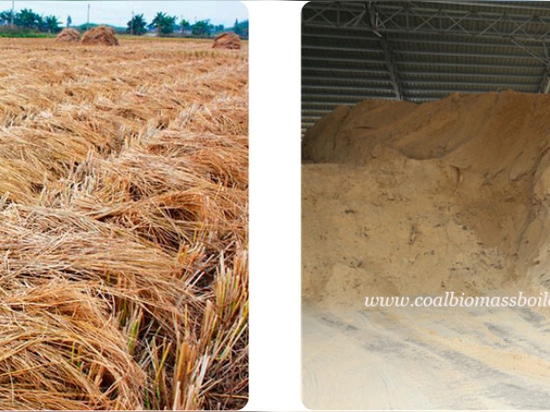