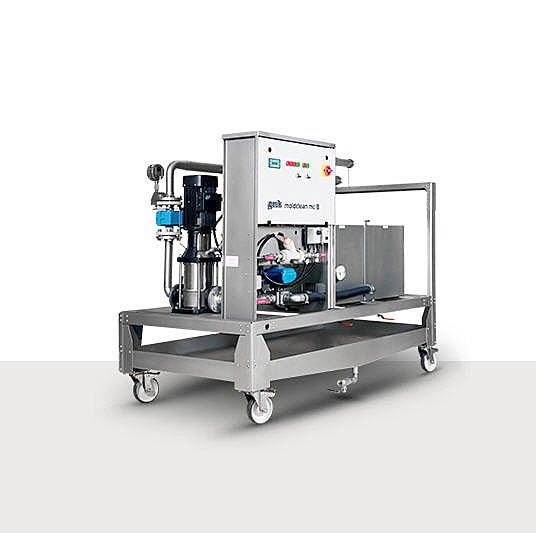
#Product Trends
moldclean - Cleaning and protection of cooling channels
Lime and corrosion are hidden cost factors. Inevitably, these two “enemies of temperature control channels” prolong the cooling time, reduce the process safety and have a negative influence on the parts'' quality. The problem occurs insidiously in each plastic processing company, because lime and corrosion gradually build an insulation layer in the cooling channels and are thus responsible for a deteriorating heat transfer. Often the problem is not recognized until the demanded parts'' quality cannot be achieved any longer or if the complete system breaks down.
The effect of cleaning the cooling channels of an injection mould is a reduction of cooling time up to 40 % (in individual cases even more), depending on the amount of deposits.
As a system supplier, gwk has been offering cleaning of components that have conducted water for a long time. The latest development, easy to use by the processor himself, is moldclean, a compact appliance which cleans polluted cooling channels in injection moulds and heat exchanger systems.
gwk moldclean mc 1:
The robust solution for the cleaning of temperature control circuits is available in two versions:
a low-cost entry-level model with one container and an alternative with two containers to optimize operating costs.The switch-over between the cleaning cycles can alternatively be made by automatic ball valves.
gwk moldclean mc 8:
The innovative solution to clean up to 8 temperature control circuits simultaneously.
The end for costs – the beginning of a margin
The cleaning process can be accelerated by jet cleaning with compressed air in order to further reduce the chemical consumption. The innovative cleaning procedure reduces the costs per cleaning cycle by up to 50%.
Cleaning
- Cleaning (cleaning agent + compressed air impulses)
- Flow measuring
- pH-value monitoring
- Neutralization
- Re-establishment of quality of molded parts