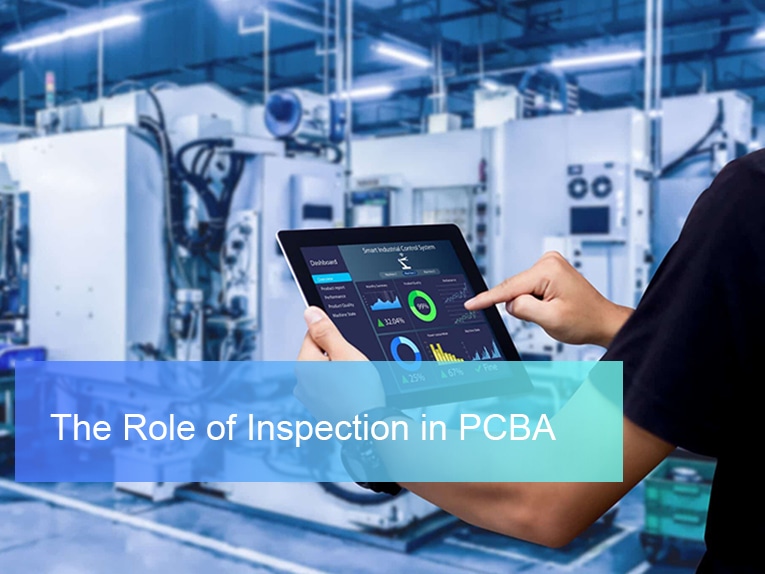
#Industry News
The Role of Inspection in PCBA
The Role of Inspection in Printed Circuit Board Assembly
In the PCBA (Printed Circuit Board Assembly) manufacturing process, inspection is crucial. It not only ensures product quality but also enhances production efficiency, preventing defective products from progressing to subsequent stages and causing unnecessary rework or waste. As a professional electronic service provider, Tecoo strictly manages each inspection stage in the PCB manufacturing process to ensure high quality and reliability. Here are the main inspection stages and their roles in PCB manufacturing:
1. Incoming Material Inspection
Tecoo conducts rigorous incoming material inspections for all raw materials and components to ensure they meet design and production requirements. This effectively prevents defective materials from entering the production line, reduces defects in subsequent processes, and improves overall production stability, ensuring that each PCB is of high quality from the very start.
2. Solder Paste Inspection
Solder paste is one of the key materials in SMT (Surface Mount Technology) processing. Through solder paste inspection equipment, the thickness, volume, and coverage of the solder paste are precisely measured. This step ensures soldering reliability, prevents issues like cold solder joints or short circuits, and better ensures the stability and efficiency of the soldering process.
3. Pre-Reflow AOI (Automated Optical Inspection)
After component placement and before reflow soldering, pre-reflow AOI is used to inspect the PCB. Pre-reflow AOI can detect issues such as component misalignment, reversal, or missing components, ensuring that all components are in the correct position before soldering.
4. Post-Reflow AOI
After reflow soldering, post-reflow AOI is used for further inspection to confirm soldering quality. Post-reflow AOI can detect defects such as cold solder joints, short circuits, or insufficient solder, while also ensuring the accuracy of component placement. Comprehensive checks with post-reflow AOI significantly reduce the defect rate during soldering, ensuring product consistency and reliability.
5. First Article Inspection (FAI)
First Article Inspection (FAI) is a key step in ensuring that products meet design requirements during production. For each new batch, Tecoo performs a comprehensive inspection of the first item produced, checking dimensions, solder joints, and component placement. The results of FAI set the foundation for subsequent mass production, preventing problems in large-scale manufacturing.
6. X-Ray Inspection
X-Ray inspection technology is primarily used to detect soldering defects that are difficult to spot with the naked eye or other equipment. X-Ray can clearly reveal internal structures and soldering conditions without damaging the components, effectively detecting defects that occur during soldering to ensure quality. X-Ray inspection technology is divided into 2D, 2.5D, and 3D types based on imaging methods:
2D Inspection: The basic form of X-Ray inspection, providing a single-angle image to check solder joints and internal structures. 2D X-Ray is fast and cost-effective, but as the image is flat, it cannot provide more information about the depth of the solder joints.
2.5D Inspection: Provides partial three-dimensional information from multiple angles. While 2.5D imaging does not achieve full 3D detail, it can show part of the solder joint's structure, helping to detect additional soldering issues.
3D Inspection: Generates three-dimensional images that can identify tiny defects not detected by other methods, such as voids inside solder joints, micro-bridges, or insufficient solder.
In the PCB manufacturing process, inspection spans the entire production flow, covering every stage from raw materials to finished products. Tecoo rigorously controls incoming material inspection, solder paste inspection, pre-reflow AOI, post-reflow AOI, first article inspection, and X-Ray inspection, creating a comprehensive quality control system that ensures the reliability and consistency of Tecoo's products and provides customers with high-quality, reliable electronic manufacturing services.