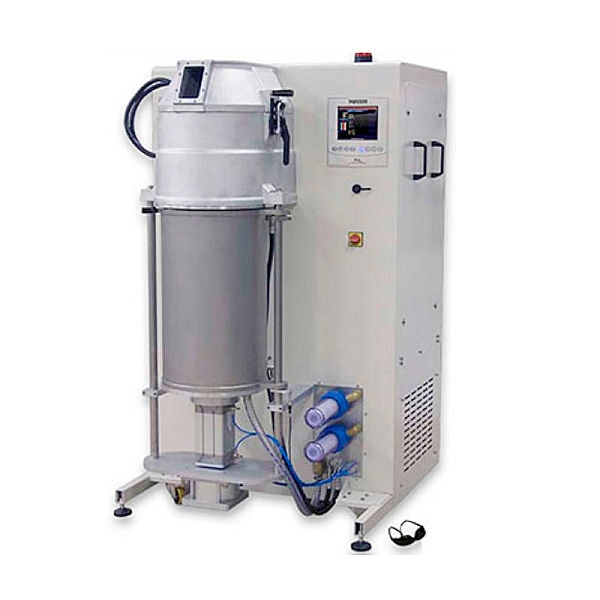
#Product Trends
Making gold and silver grains with a Topcast TVC-XL
The process starts with the insertion of the precious alloy into the crucible; then you may have a look at the monitoring system showing the process variables.
Then the alloy charge is heated and melt into the crucible by induction. Suddenly the stopper is raised and the liquid metal is poured into the water tank.
When the pouring phase is finished, a blinking lamp signals the operator that the cycle has ended, the grains can be removed and dried out.
In TVCd melting chamber and flask chamber are completely independent and at the moment of casting the machine can control the metal injection into the mold by applying a differential pressure during pouring.
This yields to a faster injection compared to the simply gravity pouring with the benefit to cast items at lower temperature. This will result in better surface finishing of the cast parts.
The casting cycle takes only few minutes and, while the previous flask is cooling down in protective gas for no oxidation, the next charge can be loaded into the crucible and melted, thus overlapping two cycles for no time waste.
The machine is fully automatic having also a PC based monitoring system for process parameters acquisition and production data management with easy editing of casting programs suitable for many kind of alloy.