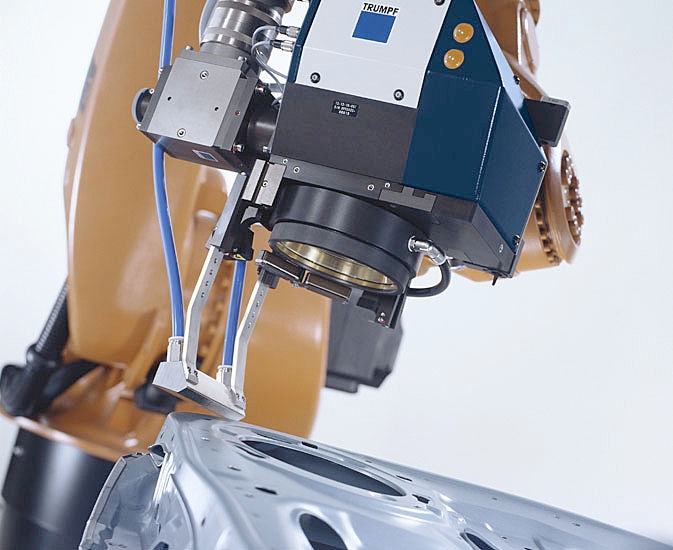
#Product Trends
Automotive Industry: Speed! - welding-on-the-fly technology
Tested for a long time - and now making its way to volume production: In 2007, Daimler introduced into production a new laser welding process using scanner optics. The improved beam guidance will help this technology capture additional market share for car body construction.
From a distance
The welding-on-the-fly technology seems to be an inspired discovery - faster, more precise, and more economical. The laser beam is generated far from the welding cell and can be directed into as many as six different exits, based on need. The light bundle is then guided through a laser light cable (up to 100 meters long) to the individual welding robots. In principle, the robot holds the flexible laser light cable in its "hand." However, instead of always positioning the "laser tool" at the end of the laser light cable precisely above the welding spot, the robot continuously moves at a relatively high distance over the workpiece.
The Highlight: A scanner head is installed at the exit end of the laser light cable. From there, two adjustable mirrors direct the bundled light to the work site in a flash. The laser beam jumps from one welding spot to the other in fractions of a second. There is no need for the robot arm to start and stop at every welding spot, a comparatively slow process which happens in spot welding. The laser beam is precisely diverted using scanner optics.
Faster and more economical
In addition to the processing speed, which is up to ten times faster, the designers and production specialists particularly value the greater flexibility in body construction. Welding patterns are possible in any shape - for example, as a circle or a staple, in an S-shape or an interrupted seam. The welding patterns, precisely adapted to the load, do not require flanges as large as are necessary for conventional spot welding. The components are therefore smaller, lighter, and more cost-effective.
Accessibility from only one side is adequate for laser scanner welding. Traditional welding guns always had to make the welding spot from both sides. Thus the laser offers an opportunity to employ profiles and tubes, which are due to the closed cross-section more rigid than formed sheets and also more cost effective. This provides designers with new ways to create even lighter and more rigid vehicles. But it presumes that they construct the bodies from the bottom up using laser technology.