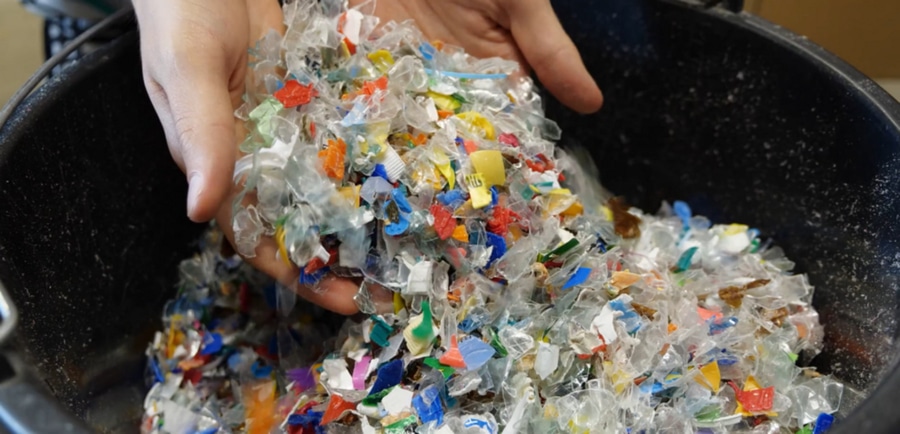
#Industry News
How Material Pre-treatment Enhances Quality and Reduces Production Costs in Plastic Processing
Want to cut production costs and boost product quality in plastic processing? The secret lies in material pre-treatment—a game-changer for efficiency, consistency, and profitability. Here's how it works!
Inconsistent quality and high defect rates are a nightmare for any plastic manufacturer. What if a simple pre-treatment step could drastically reduce defects and save costs? One critical factor that often determines success is the effective pre-treatment and drying of raw materials. These processes are essential for eliminating contaminants, controlling moisture levels, and ensuring consistent production quality.
-
-
What is material pre-treatment?
-
-
Material pre-treatment involves preparing raw materials for processing by removing impurities and moisture. As mentioned in Plastics Technology, proper drying is essential for achieving high-quality plastic parts. This step is crucial to avoid defects, inconsistencies, and inefficiencies in manufacturing. Particles and impurities can compromise material integrity and appearance. Excess moisture can lead to bubbling, cracking, and reduced strength in finished products.
-
-
Types of Dryers in Plastic Processing
Technical drawing of a drying hopper system used for efficient moisture removal in material pre-treatment.
-
Desiccant Dryers: Precision Drying for Moisture-Sensitive Materials
Desiccant dryers are essential for removing moisture from hygroscopic resins—materials that naturally absorb moisture from the air. These dryers use hygroscopic beads to extract moisture from the airflow, ensuring resins remain dry before processing.
-
A desiccant drying system typically consists of two or more drying beds, allowing for continuous operation. While one bed is actively drying material, the other undergoes regeneration—a process that heats the desiccant to high temperatures (up to 500°F) to release stored moisture before cooling it for reuse.
-
The type of desiccant used, such as molecular sieves, silica gel, or lithium chloride, determines the drying efficiency. Among these, molecular sieves are preferred in plastic processing due to their ability to achieve exceptionally low dewpoints, handle high moisture loads, and ensure consistent material drying.
-
-
Why Choose TSM Desiccant Dryers?
Prevents over-drying and resin degradation
Ensures 100% dried material enters production
Real-time air temperature monitoring for process control
Preset & programmable drying parameters for consistency
Energy-saving design with minimal resource consumption
No need for compressed air or cooling water
Adjustable airflow controls for different material needs
-
-
Types of Desiccant Dryers:
Hopper Dryer: Ideal for small-scale operations.
Wheel Dryer: Provides continuous drying for large-scale needs.
Plastic Dryer and Resin Dryer: Specialized solutions for various resin types.
-
-
-
Hot Air Dryers:
-
A hot air-drying system is a machine that removes moisture from plastic materials using heated air. It has four main parts:
-
Heater – Warms up the air.
Blower – Pushes the hot air through the system.
Temperature Controller – Keeps the air at the right temperature.
Filter – Cleans the air before it is used.
This system is mainly used with a drying hopper to dry plastics that do not easily absorb moisture (non-hygroscopic resins). It can also help with drying plastics that do absorb moisture (hygroscopic resins) before or after they go through a more powerful drying process called desiccant dehumidifier drying.
-
-
-
The advantages of using TSM Hot air dryers.
✔ Protection from overheating
✔ Accurate temperature control
✔ Automatic timer keeps drying constant
✔ Easy to use controls
✔ Energy saving technology
-
-
-
Key Applications of Hot Air Dryers
Injection Molding – Prevents bubbles and warping in moisture-sensitive plastics
Extrusion Processes – Ensures uniform material quality by eliminating excess moisture
Blow Molding – Prepares resins for hollow plastic parts like bottles & containers
Recycling – Dries recycled plastic granules for reprocessing, supporting sustainability efforts
General Manufacturing – A cost-effective solution for high-volume plastic production
Technical drawing of a drying hopper system used for efficient moisture removal in material pre-treatment.
-
-
-
The Benefits of Proper Material Pre-Treatment
Implementing effective pre-treatment and drying systems is essential for plastic processors aiming to reduce costs and improve quality. TSM’s advanced drying solutions help manufacturers:
-
-
✔ Enhance product quality – Prevents defects, cracking, and warping
✔ Reduce material waste – Minimizes scrap and rework costs
✔ Increase production efficiency – Cuts cycle times and improves throughput
✔ Lower energy consumption – Optimized drying technology saves resources
-
-
-
TSM offers high-performance drying solutions tailored to different material requirements, from small batch operations to large-scale production lines.
-
-
-
Ready to optimize your plastic processing?
-
-
Join us for a quick 20-minute discovery call
-
Discuss your project requirements and explore the best solutions tailored to your needs.
-
-
-
Want to read more?
-
Here are some useful articles on this topic.
-
Plastic News – Dryer maintenance: Don’t err with air
-
Plastics Technology – Follow These Seven Management Tips for More Consistent Resin Drying