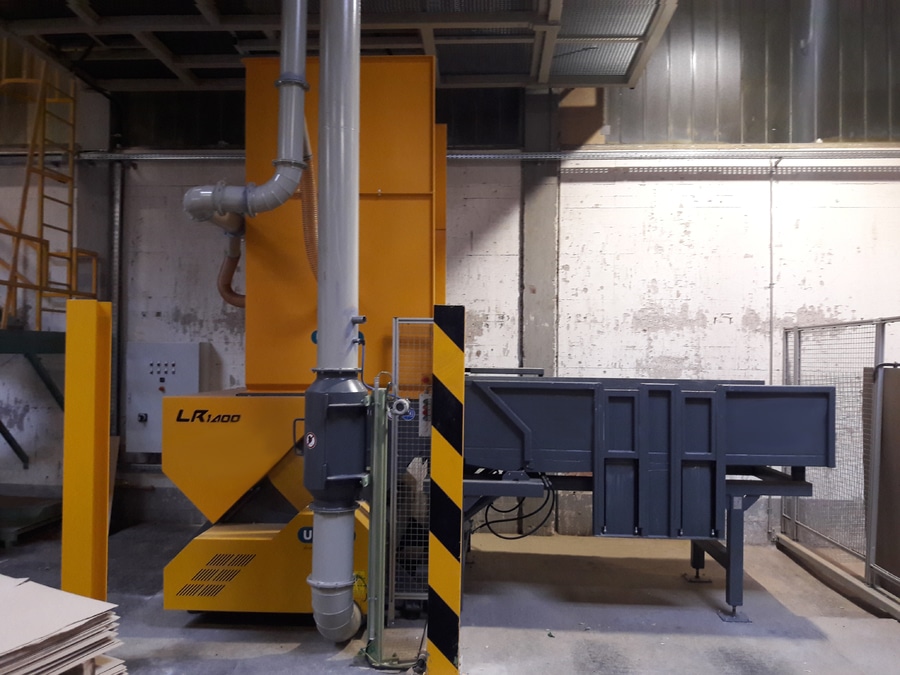
#Product Trends
LR1400 wood shredder completes closed-loop materials management at EGGER
UNTHA LR1400 for chipboard and bulky wooden parts
For EGGER, a globally active wood materials manufacturer headquartered in St. Johann in Tirol, saving resources and protecting the environment are essential parts of the company philosophy that are applied throughout its network of plants. At the Wörgl site, the LR1400 wood shredder made by UNTHA fulfils all the company requirements for environmentally robust and efficient closed-loop materials management. The unit was installed in 2018 and is running to the customer's complete satisfaction.
EGGER is a family-run business and the leading European brand when it comes to living and working with wood. This is the EGGER vision that all its activities are based upon – respect for wood as a material and for nature as a whole are key factors for the company. Sustainable growth and the careful use of resources are the cornerstones of EGGER's day-to-day business. The consistent recycling of wooden panels that are a by-product of in-house manufacturing processes is therefore an integral part of its closed-loop materials management. These wooden panels are used to manufacture new chipboard panels, and this requires shredders that comply with the stringent EGGER standards.
The solution: UNTHA LR1400 for chipboard and bulky wooden parts
Back in 2015, the UNTHA shredding technology sales team was first told that EGGER was looking for a new processing unit – a wood shredder capable of shredding thin chipboard made from soft wood into a homogeneous granulate that would then be re-fed into the manufacturing process of new thin chipboard panels. This reduces the amount of raw materials used and thus complies with the ecological principles held by EGGER.
UNTHA didn't hesitate in suggesting the LR1400, which fulfils the most stringent standards for the shredding of waste wood and is available as a customised unit. The shredder is reliable, energy-efficient and, like all UNTHA wood shredders, comes with a 3-year warranty. Among other benefits, the LR1400 is easy to operate and low in maintenance: exchanging cutters is a straightforward and rapid process, and, in case of damage resulting from foreign matter, cutter holders may also be replaced easily and quickly.
In addition, the LR1400 comes with two hydraulic cylinders that pull in the pusher simultaneously on both sides, ensuring its safe and stable functioning. The innovative cutter geometry is also a strong selling point of the LR1400, and is based on a "cut-as-you-pull" design that makes for particularly effective shredding. The screw thread was adapted to EGGER’s stringent requirements and now provides additional protection against warping. Loosening the cutter connection is also hassle-free.
Customising the LR1400 to fulfil specific requirements
The LR1400 is fully adaptable to special requirements. For wood materials manufacturer EGGER, a crucial prerequisite was that long board parts had to be brought from a horizontal to a vertical position prior to cutting, which made it necessary to install a tilting device. Arno Urbanek, UNTHA product manager, explains: "To do this, the chipboard panels are placed on the infeed table by a forklift and then tipped into the shredder hydraulically."
The control unit also had to be adapted especially for EGGER: in order to comply with the EGGER safety requirements, materials handling features were customised and fully integrated in the system. EGGER also had high expectations for throughput values, which had to be modified to achieve a performance of two tonnes per hour with the LR1400. Furthermore, the high product specifications of thin chipboard panels require a homogeneous, small-size granulate that is achieved with a 12mm perforated screen.
Decision in favour of UNTHA after a prolonged trial phase
This project did not represent a new relationship with UNTHA and EGGER, as UNTHA has already supplied a unit back in 2015. It is a testament to the intense preparation phase and numerous successful trial runs that EGGER once again opted for UNTHA when ordering a wood shredder in 2017. As EGGER has stringent requirements for safety, quality and sustainability, the decision in favour of UNTHA's LR1400 was preceded by many preliminary meetings and system tests. "During the run-up, we offered to test the input material directly at our plant. EGGER supplied us with the material and the results spoke for themselves", says product manager Arno Urbanek.
Following the positive outcome of this intensive trial period, the LR1400 has been installed by UNTHA in Wörgl and is fully operational. All relevant tests have been performed successfully, including the throughput tests which were particularly critical. In 2018, EGGER accepted the unit to their complete satisfaction. For UNTHA, however, the project doesn't end with the customer's acceptance. Martin Berger, production/technology plant manager at Wörgl, explains: "We really appreciate the high level of service provided by the team at UNTHA. Not only were they extremely helpful during the preliminary phase, when we held in-depth talks and performed thorough tests to facilitate the decision-making process, but they also provided outstanding after-sales service."