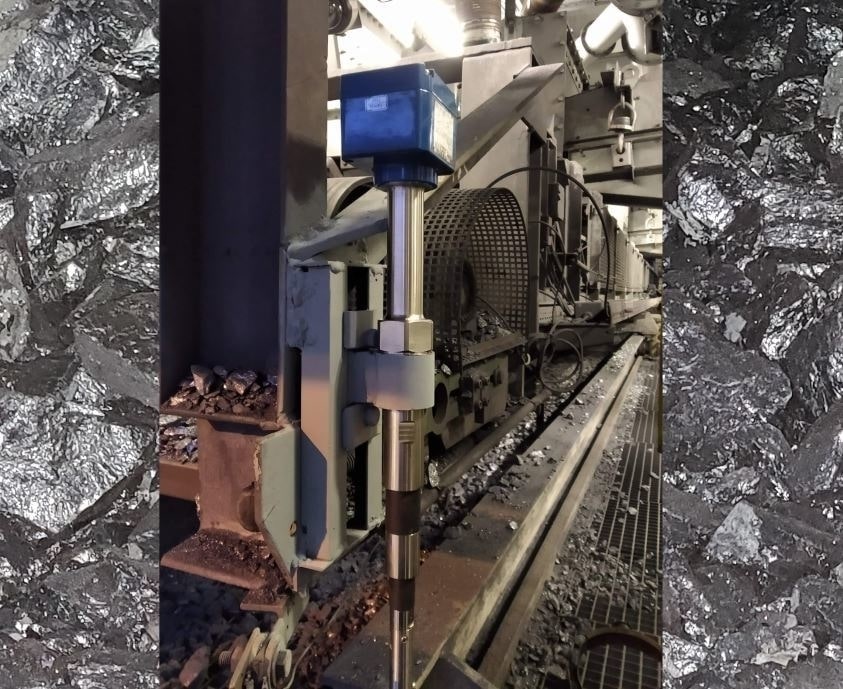
#Product Trends
Capacitance measurement technology for conveying process optimization for a silicon metal manufacturer
A silicon metal production facility in Iceland was looking for a suitable level measurement technology to coordinate the filling of sea containers with silicate rock.
Due to the very abrasive material, a heavy-duty capacitive probe should be used. With the project planning of a proven point level switch from UWT with the innovative RF technology, a compatible solution, which is robust and delivers reliable results, could be found.
Resistant RF level limit switch with dust-proof design for efficient full detection
Silicon metal is used in a variety of applications in the chemical industry, e.g. in the manufacture of siloxane and silicones, as well as in the production of high-strength aluminum alloys for the automotive industry. It is also often a primary raw material in the manufacture of photovoltaic modules. In the production processes of a manufacturer in Iceland, an above-average sustainability balance is strived for, which includes equipping its system with modern and efficient component technology. Therefore, the implementation of innovative measurement technology for the optimization of various processes was initiated. In this context it was particularly challenging to find a suitable sensor system for measuring the contents when filling the sea container with silicon metal rock.
Liquid silicon metal is regularly drawn from the furnace into crucibles and transferred to the foundry, where it is refined and cast into bars. After cooling, the bars are pre-crushed and temporarily stored in the furnace building. The product is further crushed later. The material is then sorted, packed and taken to the warehouse, where it awaits transport by sea. A conveyor belt moves completely in a sea container and fills it with the silicon metal rock, which has different dimensions up to 100 mm (3.937 in) and a DK value between 2.0 and 3.0. The point level sensor is intended to detect when the material has reached the maximum level. Then the conveyor belt is moved back until the fill level is no longer detected. The process continues until the end of the container is reached. The sensor to be used should be dust-proof and very resilient and guarantee the constancy of the measurements even in limited spaces.
The RFnivo® 3200 sensor as heavy duty version with cable extension was configured for this application. The capacitance RFnivo® point level switches can be used universally in bulk solids, granulates, powders as well as liquids, pastes and highly viscous oils for full, demand or empty detection and as level switches for overfill protection in silos, tanks, process containers, funnels, pipes and downpipes. In various device versions, they meet extreme process conditions such as high pressure or extreme temperatures. Their very robust design is also particularly mechanically resistant and is installed as standard at process temperatures of up to +240 °C (464 °F) and a process overpressure of up to 25 bar (362.594 psi). The implemented “Active Shield” technology makes the device type insensitive to material caking, bridging or types of buildup. International approvals for areas at risk of gas and dust explosions ensure a wide range of applications. The RF point level switch was installed in the left corner of the conveyor. With a user-defined sensor add-on, the installation could be optimally adapted to the limited space conditions (very low height with approx. 20 cm (7.874 inch) below the belt). The flexible active rope probe also protects the sensor from damage when it is loaded from the side.
Plug & Play
The RFnivo® capacitance switch has electronics with automatic calibration. The setup is very simple and is carried out in a menu-guided quick start wizard. The sensor calibrated itself after installation and wiring in the container and after applying the voltage supply. The operator did not have to do anything else than set the signal output in the quick start menu according to its application.
With the installation of the corrosion-resistant minimum / maximum alarms, the processes of the system with regard to the coordination of the container filling could be optimized in an efficient and user-friendly manner.
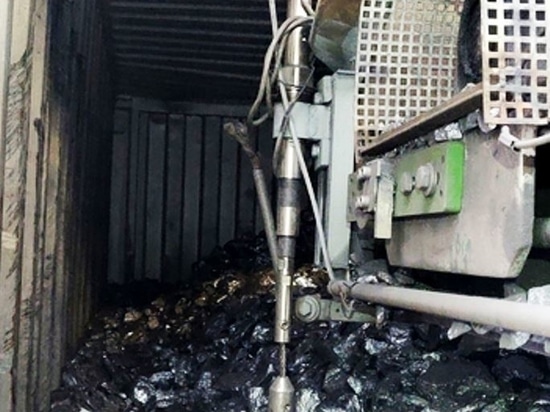
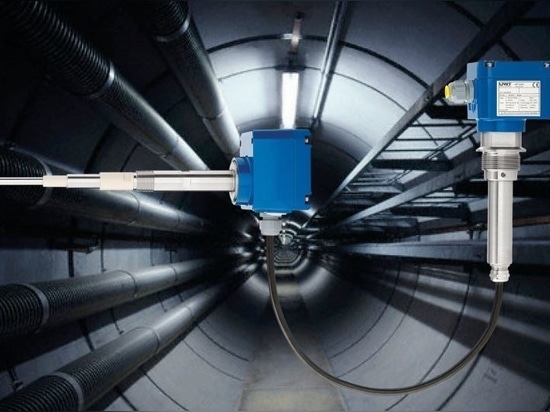
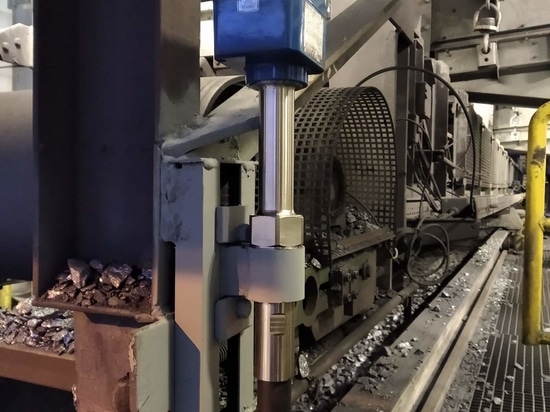

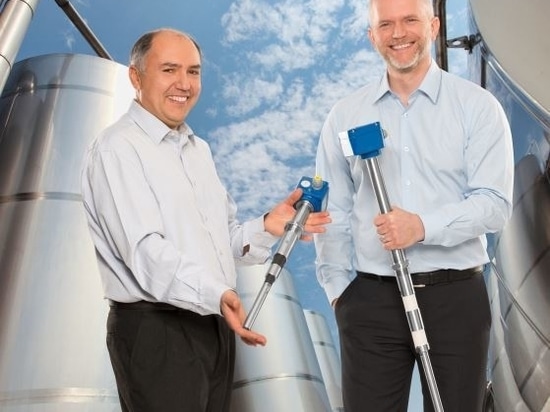