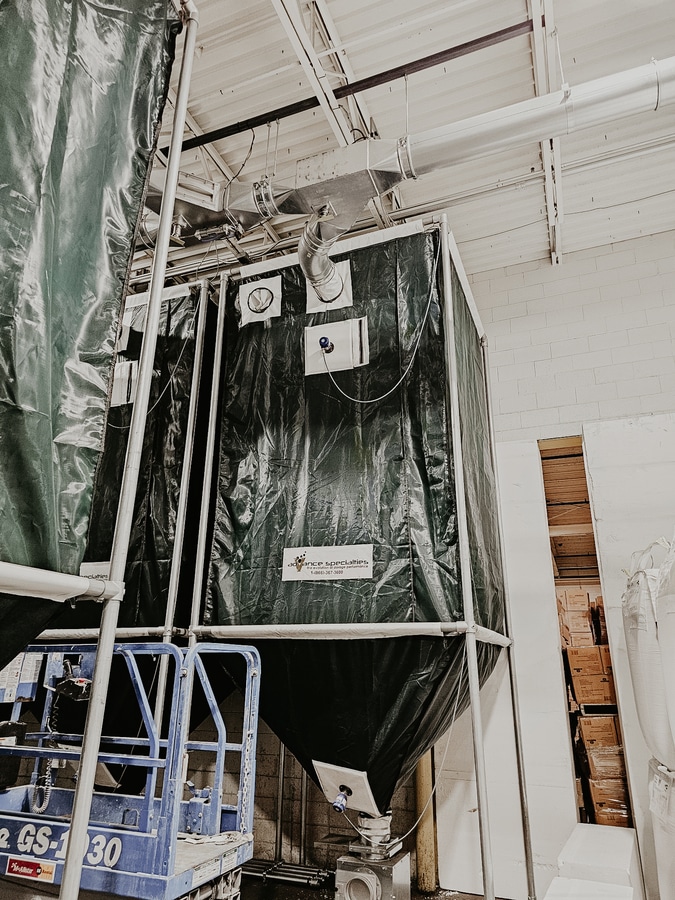
#Product Trends
Customized Dual-Sensor Solution for Low-Density Bulk Material
UWT Sensor Combination for Efficient Level Control in the EPS Industry
A prominent expanded polystyrene (EPS) manufacturer from the USA was faced with major challenges when it came to fill level measurement due to the special properties of the material. The very low bulk density and the particular storage conditions made it difficult for conventional sensors to accurately recognise and detect the fill levels.
UWT offered an effective solution by installing two different level sensors: a rotary paddle level switch and a vibrating fork in combination.
The challenge: Material properties and storage conditions
Two major challenges had to be overcome in the EPS production plant in order to ensure effective and reliable operation:
• Low bulk density:
Due to the very low bulk density, EPS materials settle at the bottom of the silos and compact there. This compaction can create a more dense material layer, which facilitates the operation of level sensors. However, as the material level increases, the density and compression decreases, meaning that sensors with high contact sensitivity are required.
• Storage conditions:
EPS products are stored in fabric silos, which makes the installation of conventional level sensors difficult, as their own weight can cause instability and measurement errors.
The solution: Combined technologies of the rotary paddle level switch and the vibration fork
To overcome these challenges, UWT Level Controls implemented a unique and effective solution by installing two types of level sensors:
• Empty detector:
The Rotonivo® 4001 with its sensitive rotating paddle works effectively at low bulk densities. The sensitivity can be adapted to light materials by adjusting the return spring. Its weight-reduced design, including a plastic housing and a special rubber paddle, reduces sagging in fabric silos.
• Full detector:
The Vibranivo® 6020 sensor ensures accurate and reliable level measurement in the upper area of the silo, where the material density is even lower. The vibrating level switch has been equipped with a Vibrasil 90. The extended vibration fork increases the sensitivity even further. As a result, this sensor recognises EPS bulk materials with a bulk density of less than 1 lb/ft³ (~16 g/l). This results in faster response times and optimises production efficiency for full level messages in the silo.
Tailored solutions for diverse applications
By integrating the Rotonivo® 4001 and Vibranivo® 6020 sensor combination, UWT addresses the unique characteristics of EPS materials and the complexities of fabric silos. This customised solution ensures precise monitoring and control of material levels and increases reliability and accuracy in different operating conditions. The dual sensor approach emphasises UWT's commitment to advanced technologies and effective industrial solutions.
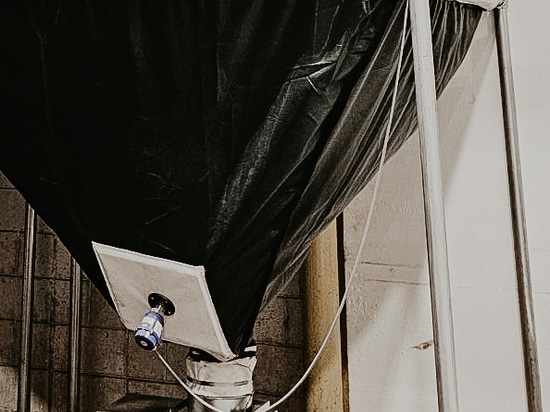
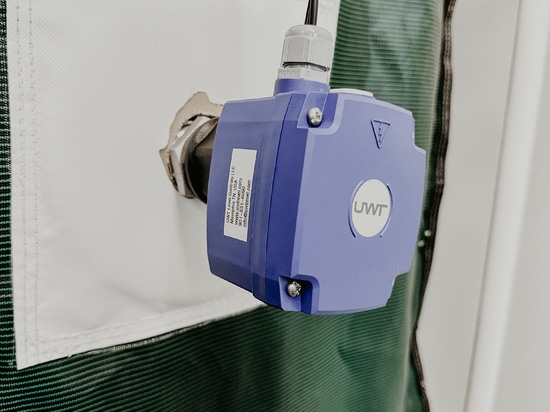
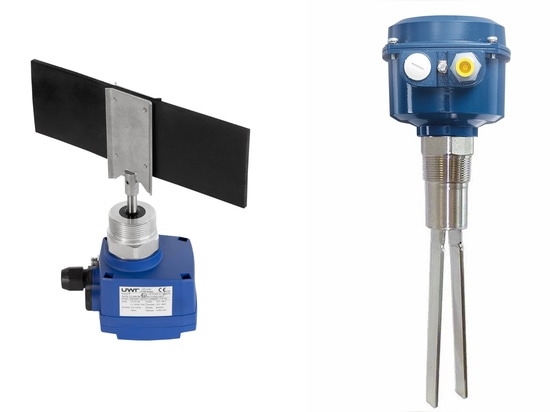