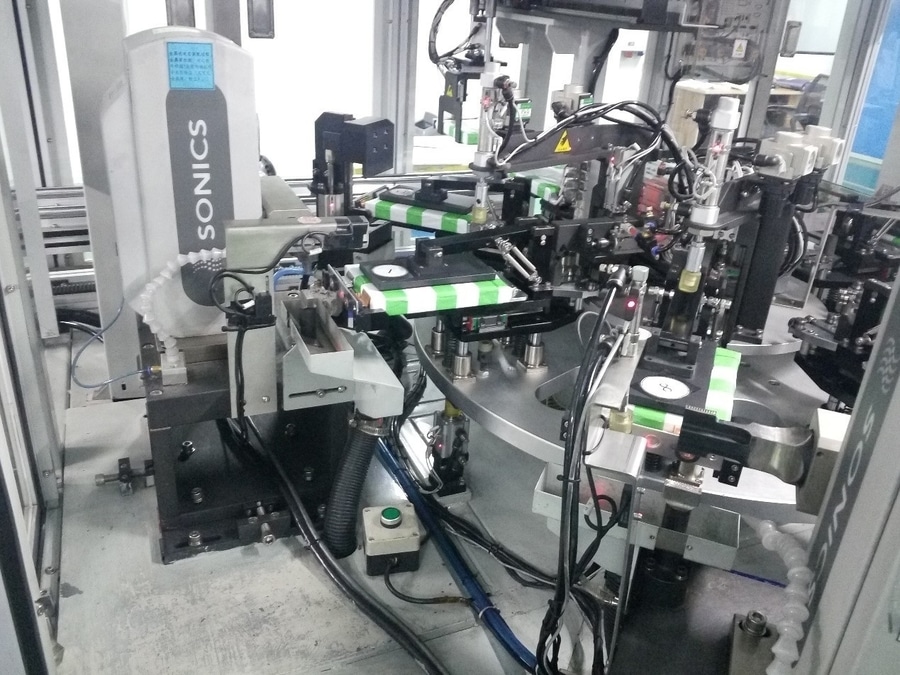
#Industry News
The Ultimate Guide of Dust Remover Machine for Li-ion Battery Industry
Dust Control Equipment & Solution of Li-ion Battery Manufacturing Process
Lithium-ion battery manufacturing has made significant progress in recent years and has become increasingly important in various emerging markets, such as renewable energy and electric or hybrid automobiles. Apart from the spike in manufacturing of Li-ion batteries in the past decade, some safety concerns have attracted attention recently. During battery manufacturing, many processes involve the production of airborne contaminants that can harm workers, machines, and product sustainability. These contaminants should be removed by a dust remover machine to avoid a negative impact on the production process.
Dust Removal in Li-ion Industry
The Li-ion manufacturing industry demands an extremely reliable and efficient dust removal system. Because of Lead, Cadmium, and other harmful materials, the battery manufacturing process becomes a potential safety risk. There are various solutions available to mitigate those risks. Industrial dust remover machines equipped with ultra-efficient filters (HEPA filters) are extensively used in Li-ion industry. This equipment is designed to effectively and efficiently extract the dust and airborne contaminants from the production process.
The lithium-ion battery cell production consists of a series of processes and steps, as mentioned in the block diagram.
The manufacturing process starts with the mixing process, which involves feeding and discharge of ingredients, which generates a serious amount of fine powder dust. The generated dust should be dealt with by a dust remover machine in a timely manner to avoid pollution in the production environment and to avoid adverse health effects on production personnel. The source of dust is concentrated in the mixing feed port and the discharge port.
2. During the rolling process, many small powders adhered to the surface of the rollers, which needs to be cleaned. The cleanliness of the rollers is necessary to prevent foreign particles from penetrating the substrate material. Roller brushes are generally used for this purpose. During the compaction process of the roller press, the surface of the upper and lower rollers is adhering with lots of fine powder, and the surface of the roller must be cleaned by a dust remover machine. Currently, the roller presses in the market use a scraper for this cleaning job.
3. The division process of a wide electrode coil (mother roll) into several smaller electrode coils (daughter coils) involveslaser cutting. The laser utilizes a strong beam of light to melt/vaporize and blow away the material. As a result, metallic dust and hazardous fumes are generated owing to oxidation, which can be seriously harmful if inhaled. In this case, a dust remover machine is essential.
4. The cutting process can also be carried out using a slitting machine (generally rolling knives are used for this purpose), which can produce residual waste (leftover material). These waste materials will stay on the slitting machine, affecting the service life of the equipment and the quality of the battery cells. The source of smoke/fumes and dust during slitting or laser cutting is at the position of the cutter and the position of the roller brush. Dust removal equipment can help the cutter and the roller brush to remove dust well.
5. During the Lamination process, dust is produced during the stacking of the individual electrode and the separator sheets onto each other. The dust should be removed immediately with dust removal equipment to avoid damage.
6. Additionally, to package the pouch cell, the current collector foils are contacted with cell tabs through laser or ultrasonic welding. The welding process also generates metallic oxides and fumes, which can cause serious damage to lungs. For the safety of the staff, it is necessary to have a dust remover machine.
7. Winding is required during the production of prismatic and cylindrical cells. During winding process, the dust generation point depends upon the shape of battery.
Square battery: During the winding process, the main dust generating points are the powder brush and the main shaft winding area. (that is, the pole piece cutting position)
Cylindrical battery: The main dust production points of the cylindrical battery are the powder (or blowing and suction) box, the welding point of the pole lug, and the winding area of the main shaft (that is, the position where the pole piece is cut off), which produces a certain amount of smoke and cutting chips or particles. The dust remover machine can help remove dust in places prone to dust, which is more convenient and cleaner than manual dust removal. A dust remover machine will be the best way to remove dust.
8. During the packaging process of cell assembly, the jelly roll’s edges are compressed, fixed, and ultrasonically welded to the contact terminals attached to the battery’s lid. An insulation foil protects the jelly roll during insertion into the prismatic housing. And the housing is often sealed by a laser welding process.
New technologies arising in the wake of a spike in lithium-ion battery manufacturing are subjected to meet special environmental protection requirements. A proper dust remover machine and extraction system are necessary to provide protection against harmful contaminants produced during the manufacturing of Li-ion batteries.
VILLO has been actively providing dust removal solutions for the Li-ion battery manufacturing industry for the past decade. The state of art dust removal equipment is equipped with a highly efficient filtration system. We propose an ideal solution by professionally modeling your facility to guarantee performance and productivity. Our dust removal equipment will be the best way to remove dust.
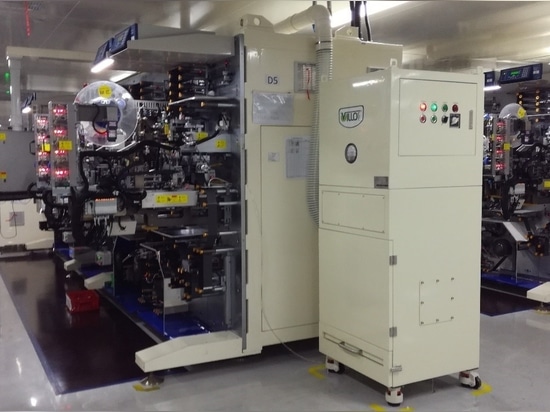