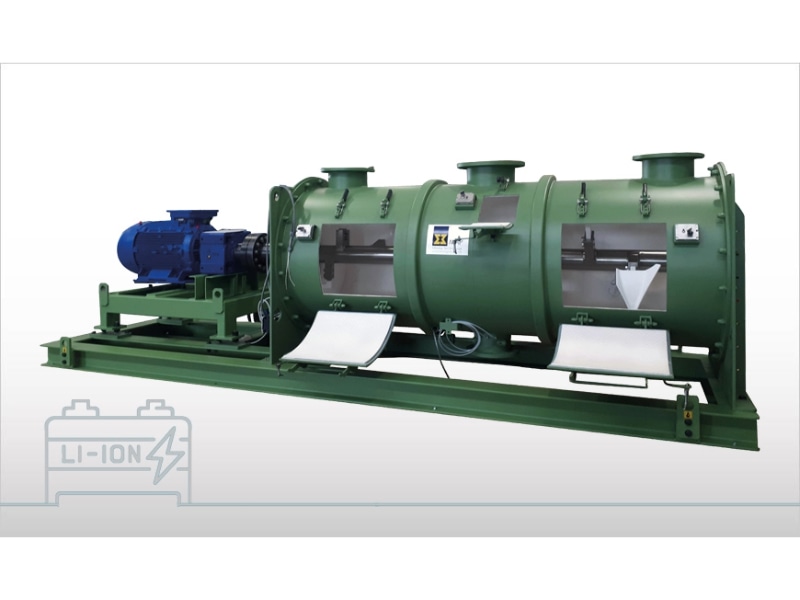
#Industry News
Manufacturers of Lithium-Ion Batteries Rely on Specialised Mixing Technology from MAP
MAP's WBH battery mixer, designed for lithium-ion battery production, ensures quality, efficiency, and contamination prevention, satisfying global industry demands.
In the production of lithium-ion batteries, the highest quality demands are placed on production facilities. When mixing the cathode material, contamination must be avoided under all circumstances, whereby abrasion and corrosion on the mixing tools must be prevented and at the same time a high demand for homogeneity has to be ensured.
In addition, when mixing cathode material, the aim is to produce the mixture in a short time with the lowest possible energy input. MAP, a division of WAMGROUP for industrial mixing technology, therefore developed the WBH battery horizontal single-shaft mixer several years ago, a machine specialised for battery mass production. Since the quality of the preparation of the cathode raw materials is the basis for high-performance lithium-ion batteries, mixing quality and efficiency are the most important criteria that MAP has taken into account in the specialisation of the WBH battery, in addition to the avoidance of impurities.
The result is convincing customers in the industry all over the world. To date, more than 1,200 MAP mixers for battery mass production have been put into operation. The mixers are manufactured from stainless steel to prevent contamination from outside and inside the machine. MAP guarantees that all components manufactured and used by the company are free of impurities and approved for secondary battery production. Inside the mixers are equipped with a special ceramic lining. The main shaft as well as the mixing tools and chopper blades are provided with a ceramic coating too. Depending on process requirements, alternative coatings and linings can be applied. Both the seals on the main shaft and the design of the discharge flaps are adapted to the high demands of battery mass production and offer the customer maximum process reliability. Short mixing time and a high reproducible mixing quality are further criteria with which the WBH battery convinces customers.
The many years of experience with a wide variety of recipes in cathode production and WAMGROUP's worldwide network with over 60 subsidiaries and more than ten of its own test laboratories spread all over the globe make MAP the ideal partner for plant manufacturers and producers in this field.
Editor’s question:
If you look at the number of mixers delivered for the battery industry, you can say with certainty that you are the leader in this industry. How did you achieve this?
Answer:
Unlike others, we do not just supply a mixing machine, but offer the customer a solution. Before we submit a quotation, we analyse the requirements together with the customer and search for the most suitable technology. If a part of those requirements cannot be solved with existing options, we develop these further in a targeted manner.
We do not see our role in this area as that of a pure manufacturer, but as a partnership with our customer to achieve optimal results together. In this respect, the best result is not only the mixer as such - there would be plenty of manufacturers for this - but we offer the customer the solution with which he can achieve excellent, reproducible mixing homogeneity of his product batches in the shortest possible time. Avoiding contamination of the product and easy maintenance of the system are further important points.
Furthermore, with our global network of over 60 WAMGROUP subsidiaries, we offer our customers a local contact person and the best possible service in literally all countries.
Editor’s question:
You describe yourself as a partner who offers solutions. What does that look like in practice?
Answer:
Of course, we can't reveal everything... But we can say so much that we don't produce a standardised machine for this sector. Rather, we have developed numerous suitable options for the multitude of applications. In the meantime, we have specialised a number of variants and can therefore react to different requirements and offer the optimal solution for each product, recipe or process.
In battery mass production, different raw materials are used, and different production processes are employed. We have been working closely with the industry leaders for many years and have therefore been involved in development for quite some time. Our cooperation not only extends to our customers, but also includes universities and research centres. This sector is constantly evolving, and it is therefore of great advantage for us to always be involved at a very early stage thanks to our close relationships. From the first tests to an industrialised solution, we accompany the entire process. To do this, we also use our own 10 test laboratories spread around the globe.
There we are already working together with our customers on the next generation of production technology, in particular with regard to sustainability.
Editor’s question:
Can you at least give us a hint about these jointly developed solutions that justify your leading role?
Answer:
The partnership is not only limited to us and our customers, but also involves strategic suppliers and universities, thus creating a strong team. In this team we have not only been able to develop options and accessories, but also to further develop and industrialise materials for these applications. Depending on the process and product, the mixers are designed with different coatings, which can differ both in the base material and in application technology. After all, it is not only important to choose the right materials for a coating. It is at least as important to use the appropriate application technique. This applies to ceramic materials as well as to polyurethane, hard metals or other materials.
In order to improve the dosage of the product to be dispensed, we have specialised the entire outlet situation. By using special seals and materials, we can completely avoid product loss and contamination.
All of these developments involve hard work, a lot of effort and humility. The mistakes we have made over the years have also helped us to keep improving and to be able to support today such a large number of successful projects.
Editor’s question:
1,200 machines sold in battery mass production is an impressive number. What do you expect from the future?
Answer:
Yes, we have sold 1,200 machines in recent years, especially in the Asian markets where this technology has developed and in some European countries. However, we expect much larger numbers in the future. We are already working with both long-term and new customers on several projects, also here in Europe and North America.
In view of this great potential, we have set up a separate production line to meet the growing demand and to be able to react quickly. On this production line, we are able to ensure high product quality in all manufacturing stages and in all processes and methods applied. We have adapted our production instructions, our quality management and quality control as well as machine acceptance tests to the high requirements of this industry. And yet every day there are new tasks and many new challenges that we face together with our partners. We are therefore convinced that we are well positioned for the future.