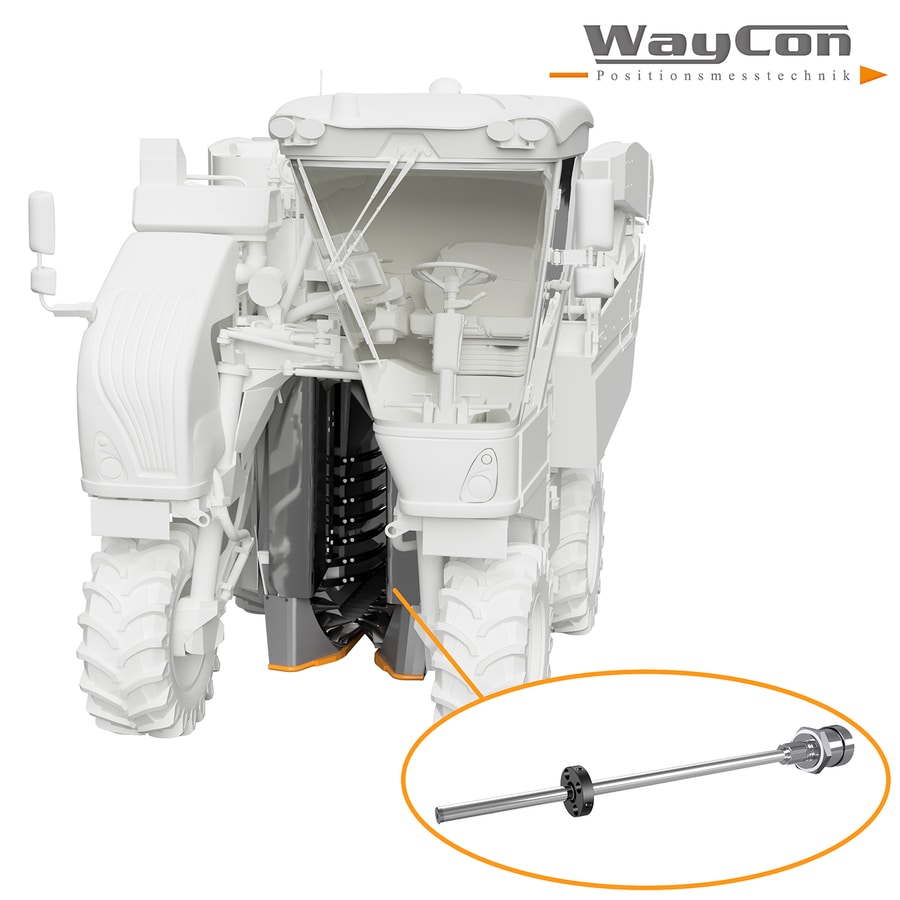
#Product Trends
Magnetostrictive Transducers Sensors Optimise Yield and Cost Efficiency in Grape Harvesters
In modern agriculture, automation plays a central role in maximising yields while optimising work processes at the same time.
Sensors such as magnetostrictive displacement sensors are revolutionising the use of modern agricultural machinery, especially in grape harvesters. The use of these precise sensors for measuring length and position significantly increases efficiency in viticulture and raises machine control to a whole new level.
Magnetostrictive sensors make it possible to detect mechanical movements with high precision and convert them into analogue signals. This is particularly important when controlling moving components, such as the vibrating arms or the conveyor mechanism of a grape harvester, in order to protect the sensitive grapes and vines during harvesting. Thanks to the high repeat accuracy and wear-free measuring principle of magnetostrictive sensor technology, positions can be determined precisely without mechanical wear having an adverse effect on measuring accuracy. This is a significant advantage in the demanding milieu of winegrowing, where vibrations, dust and exposure to plant parts are a fact of everyday life.
Sensor-supported control of the work processes not only improves harvest quality but also contributes to a reduction in energy consumption and machine load. The use of magnetostrictive sensors clearly illustrates the continuous development and use of intelligent technologies in agricultural engineering, with the aim of maximising efficiency while minimising operating costs. The resulting advantages are decisive factors that will have a positive influence on the future of viticulture.
One example of these sensors are the magnetostrictive displacement sensors of WayCon’s MSB series. These robust sensors are capable of a measuring length up to 2.5 m at an accuracy down to ±0.02 %. With a housing that is pressure-resistant up to 350 bar, the sensors are ideally suited for use in hydraulic cylinders. Thanks to a travelling speed of up to 10 m/s, the displacement sensors are also able to keep up with dynamic applications. The standardised analogue output signals also facilitate their integration in device control systems.