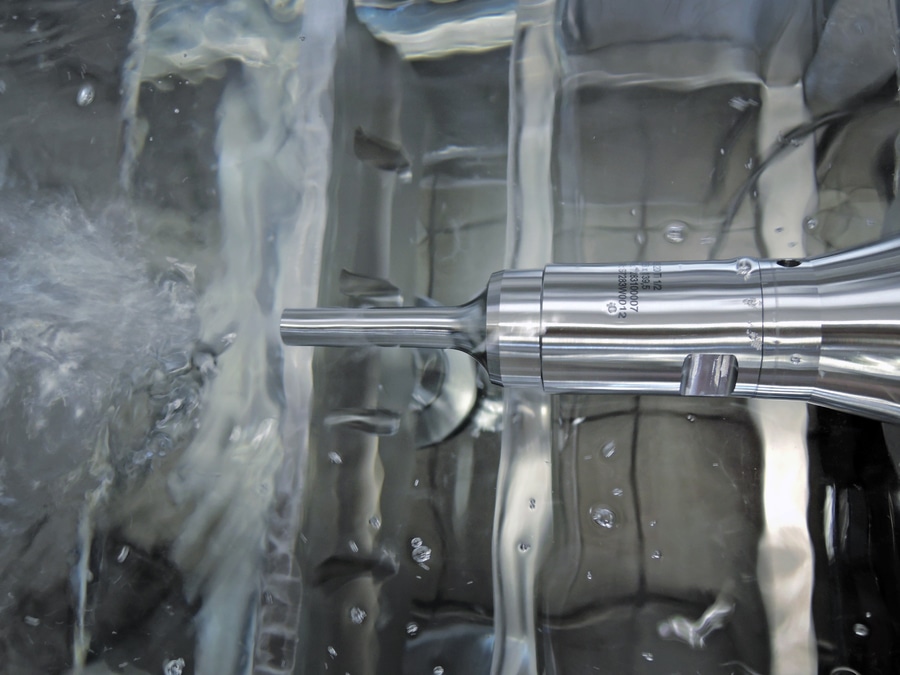
#Industry News
Deburring with ultrasound
Removing burrs accurately, gently and in an energy-efficient process
The demand for greater process efficiency also extends to deburring. Ultrasonic deburring is the first ever process to use the cavitation effect of ultrasound to gently and accurately remove burrs from metallic components in a targeted and cost-efficient way.
Burrs on metallic components, in particular in internal cavities such intersecting boreholes, are today typically removed mechanically using a cutting tool. However, this process also harbours the risk of creating secondary burrs. Alternatively electrochemical or thermal processes and high pressure water jet blasting are sometimes employed. Yet these technologies are highly energy-intensive and therefore costly.
Weber Ultrasonics, one of the world's leading manufacturers of ultrasonic components, has cooperated with the Fraunhofer Institute for Manufacturing Engineering and Automation (IPA) to develop a process that uses the cavitation of ultrasound to deburr metallic components. Just like ultrasonic cleaning, deburring is also performed in a liquid. During the process, the workpieces are subjected to intensive cavitation for a brief period. When they implode, the localised high-density cavitation bubbles generate such high forces that the burrs are effectively yet gently removed. The key criteria for the deburring effect are the amplitude, power output and frequency of the ultrasound, as well as the distance from the workpiece and the treatment time. Setting application-specific parameters allows the entire spectrum of deburring to be performed - from micro to rough deburring. An important bonus here is that the deburred surfaces are also simultaneously cleaned.
Energy-efficient deburring of internal and external surfaces
The new process can be used both for contactless deburring of internal areas and for external component surfaces, such as stamped, cast aluminium and die-cast zinc parts. The system is matched to the respective component geometry by the design of the deburring tool – the sonotrode. It can be guided manually, with mechanical support or in a fully automated sequence.
Experiments with various aluminium parts have confirmed the excellent deburring effect. They also showed that the process is significantly more energy- and cost-efficient than high-pressure water jet deburring.
www.weber-ultrasonics.com
About Weber Ultrasonics
Weber Ultrasonics GmbH is based in the town of Karlsbad-Ittersbach in the south-west of Germany and was founded in 1998 by Dieter Weber, co-inventor of the "push-pull" principle. The company represents the Surface Technology business segment within the Weber Ultrasonics Group. Thanks to its innovative components for ultrasonic cleaning and excellent service, the company has developed into one of the global technology leaders in the space of just a few years.
The ultrasonic cleaning solutions offered by Weber Ultrasonics are used in the automotive, sanitary and watch & clock-making industries, the fields of electrical engineering, electronics, precision mechanics, optics, surface and cleaning technology, metal working, PCB manufacture and numerous other sectors.
Other business segments of the Weber Ultrasonics Group include the development and manufacture of high-grade components and systems for ultrasonic welding and cutting, as well as environmental technology. The Group is represented in over 50 countries. The subsidiary Weber Ultrasonics America produces and sells the Group's ultrasonic solutions across the entire American continent. Weber Ultrasonics Asia was founded in 2013 and is responsible for sales and distribution of ultrasonic cleaning products in the entire Asian market.
www.weber-ultrasonics.de