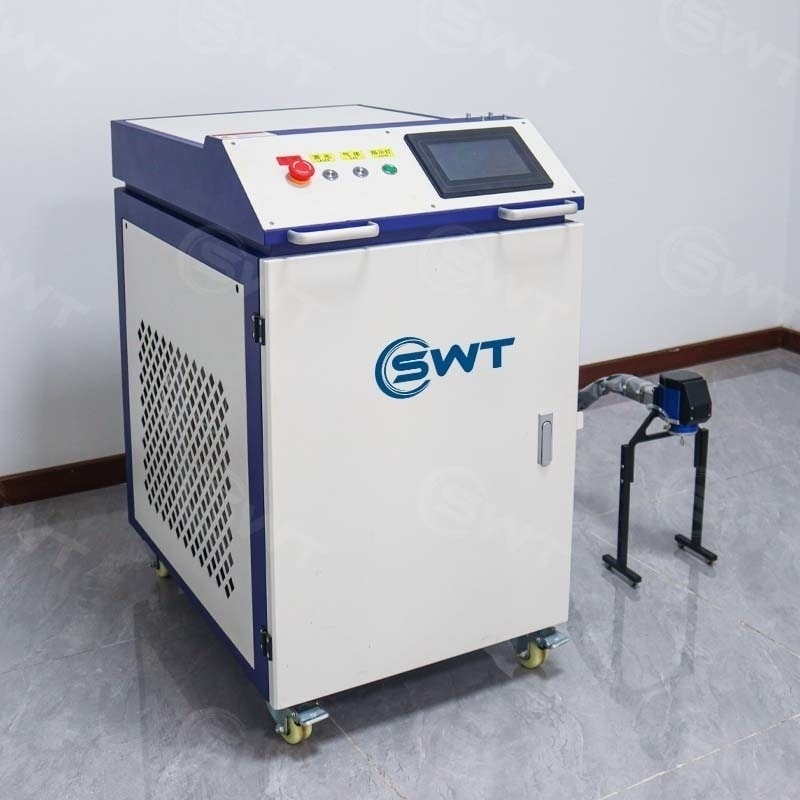
#Product Trends
Pulsed Laser VS CW Laser For Cleaning
Pulsed Laser VS CW Laser
We all know that the types of laser generators include continuous wave lasers (also known as CW lasers) and pulsed lasers. As the name implies, the continuous wave laser output is continuous in time, and the laser pump source continuously provides energy to generate laser output for a long time, thereby obtaining continuous wave laser light. The output power of CW lasers is generally relatively low, which is suitable for occasions requiring continuous wave laser operation. Pulsed laser means that it only works once at a certain interval. The pulsed laser has a large output power and is suitable for laser marking, cutting, welding, cleaning, and ranging. In fact, in terms of working principle, they all belong to the pulse type, but the output laser pulse frequency of the continuous wave laser is relatively high, which cannot be recognized by the human eye.
In the field of laser cleaning, fiber laser has become the best choice for laser cleaning light source due to its higher reliability, stability and flexibility. As the two major components of fiber lasers, continuous fiber lasers and pulsed fiber lasers occupy a dominant position in macroscopic material processing and precision material processing, respectively.
The removal of rust, paint, oil and oxide layer on metal surfaces is currently the most widely used field of laser cleaning. Floating rust removal requires the lowest laser power density, and can be achieved by using ultra-high-energy pulsed lasers or even continuous wave lasers with poor beam quality. In addition to the dense oxide layer, it is generally necessary to use a MOPA laser with a near-single-mode pulse energy of about 1.5mJ with a high power density. For other pollutants, an appropriate light source should be selected according to its light absorption characteristics and the ease of cleaning. SWT's series of pulsed and continuous wave laser cleaning machines are suitable for the application of super large energy coarse spot and high energy fine spot respectively.
Under the same power conditions, the cleaning efficiency of pulsed lasers is much higher than that of continuous wave lasers. At the same time, pulsed lasers can better control the heat input and prevent the substrate temperature from being too high or micro-melting.
CW lasers have an advantage in price, and can make up for the gap in efficiency with pulsed lasers by using high-power lasers, but high-power CW lasers have greater heat input and increased damage to the substrate.
Therefore, there are fundamental differences between the two in application scenarios. With high precision, it is necessary to strictly control the heating of the substrate, and the application scenarios that require the substrate to be non-destructive, such as molds, should choose a pulsed laser. For some large steel structures, pipes, etc., due to the large volume and fast heat dissipation, the requirements for damage to the substrate are not high, and continuous wave lasers can be selected.
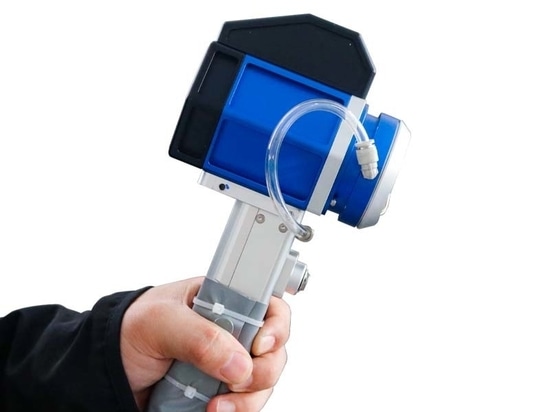