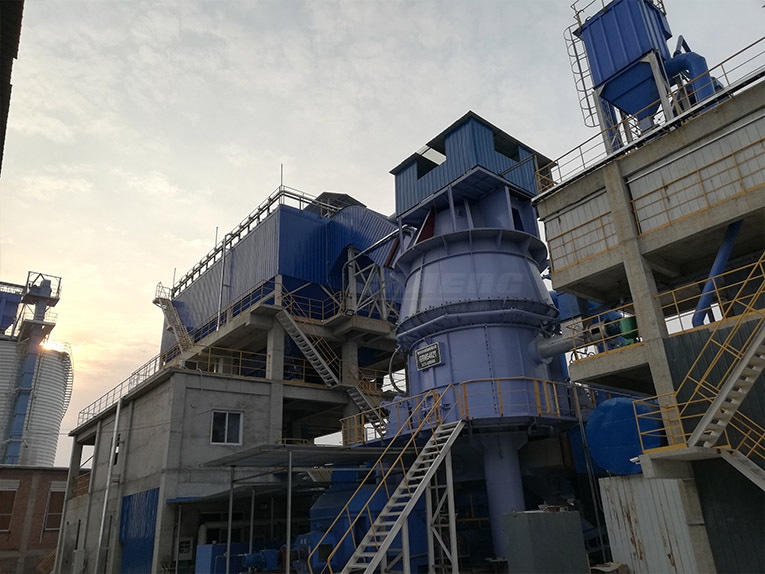
#Product Trends
Introduction of cement clinker grinding systems--CHAENG
Introduction of cement clinker grinding systems--CHAENG
In a modern cement plant the total consumption of electrical energy is about 100 kWh/t . The cement grinding process accounts for approx. 40% if this energy consumption. Further the quality of the final cement is very dependent on the operation mode and product quality as well as consumption of electrical energy it is important that the cement grinding plant is adequately designed , and is operated properly .
Cement Clinker.jpg
FINENESS
The cement has to be ground fine enough to meet the requirements for strength properties specified in current standards or, more often, requirements from the customers .
As it takes quite a long time to determine especially the late strength, the-hour –to hour and day-to-day control of cement grinding has to be based on the cement fineness . Over longer periods, however, it is the strength figures that determines to which fineness the cement is to be ground
The cement fineness can be determined by various methods. So far, determination of the specific surface, for instance, according to the Blaine permeability method, has been commonly used. However it is getting more common to determine the finesse by sieve,analysis on one or more sieves or by a complete particle size, since fineness figures based on these methods usually have a better correlation to the cement strength properties
GRINDABILITY
Experience from laboratory grinding tests, as well as from a great number of cement mills, show that the specific power consumption required to obtain a certain fineness, for instance 3000 Blaine , varies from 25% below 50% above the average .
Cement clinker with a low lime saturation factor has a high content of C2 S and generally difficult to grind. There are, however, many other factors that seem to influence the grindablity. For instance, clinker with a high content of very small pores will be easy to grind, Other factors, as crystal size, cooling velocity after burning, and age of clinker after burning, may exert some influence on the grindability.
So far, it is not possible to calculate clinker grindability from the chemical and mineralogical composition. The proper dimensioning of cement mill must, therefore be based on laboratory grinding test, or in the case of a new cement plant where the clinker is not available, on certain assumptions as far as grindability is concerned.
The common cement grinding systems can be divided into three main groups:
1.Tube Mill Only
All grinding work is done in the tube mill and the set-up is:
(1)Tube mill in open circuit
(2)Tube mill in closed circuit with
(3)Mechanical air separator
(4)Rotor type separator
2.Tube Mill with Pregrinding Unit
Part of the grinding work is done in a pregrinding unit, which can be:
(1)Roller press
(2)Vertical shaft impact crusher
(3)Vertical roller mill (without separator, only grinding tool is used)
3.Finish Grinding System
The tube mill is omitted and all grinding work is done in a more efficient comminution machine. The possible systems are:
(1)Roller press with desagglomerator and rotor type separator
(2)Vertical roller mill with integrated rotor type separator