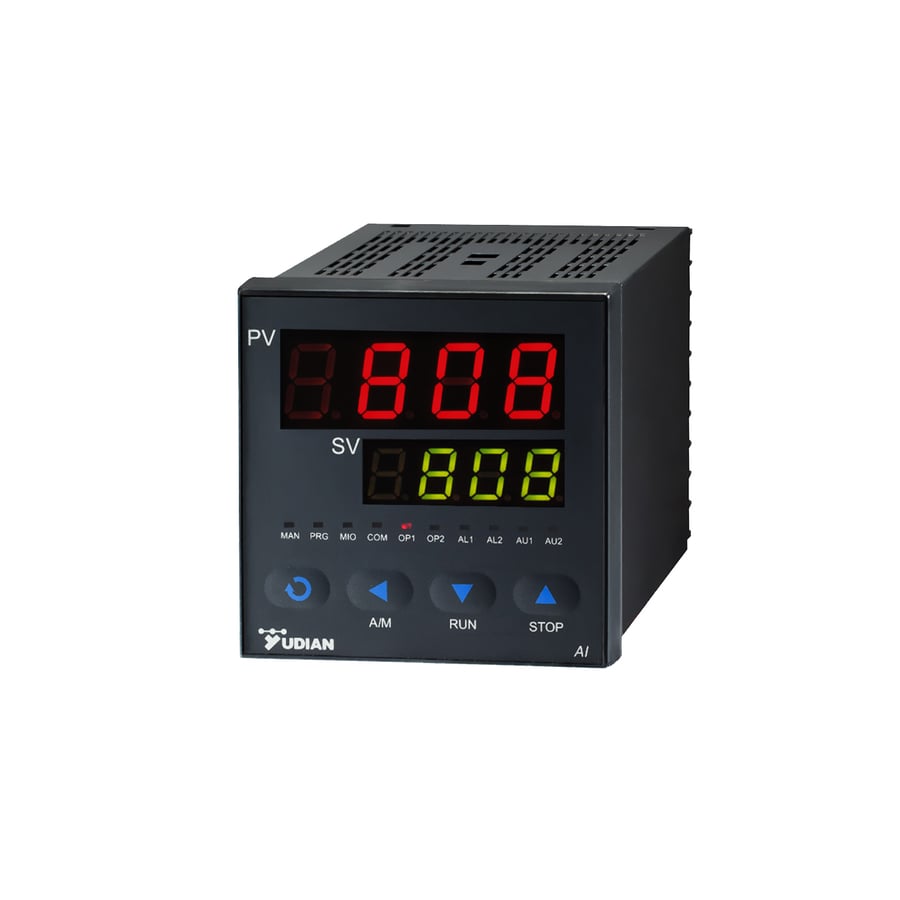
#Product Trends
Application of AI series temperature controller in aluminum foil production
Application of AI series temperature controller in aluminum foil production
Overview: This article mainly introduces the production process of aluminum foil from raw aluminum. In this project, the temperature control is connected at each step, which simply explains the function of the instrument and some simple instrument parameter settings.
Key words: primary aluminum, temperature control instrument, aluminum foil
Introduction:
In the early days, China's aluminum was mainly used for military purposes. The demand for aluminum foil was very small. After the 1980s, aluminum foil was developed as a civilian product. After the mid-to-late 1990s, the market for cable foil, air-conditioning foil and cigarette foils grew rapidly. During the period, China's aluminum foil industry has developed rapidly. According to relevant statistics, the average demand for aluminum foil is about 6% of total requirements of aluminum . In China, the demand for aluminum foil is basically in sync with the demand for aluminum. In developed countries, aluminum foil accounts for 7.5% to 8% of the total aluminum, showing that the overall level of aluminum foil consumption in China is low. At present, the most demanding products in China's aluminum foil market are air-conditioning foils, cigarette foils, decorative foils and cable foils. The demand for these four varieties accounts for more than 70% of the total demand. The demand for automotive foils, flexible packaging foils, pharmaceutical foils and electronic foils is small, but the market growth is good and has become an important growth point in the aluminum foil market. At present, Xiashun Aluminum Foil Co., Ltd., Henan Antai Foil Co., Ltd. and Henan Keyuan Electronic Aluminum Foil Co., Ltd. are the largest manufacturers of thin aluminum foil in China. Among them, Henan Keyuan Electronic Aluminum Foil Co., Ltd. specializes in producing aluminum foil for electrolytic capacitors. The demand for aluminum foil for electrolytic capacitors is not large, but the prospects are good.
Requirements of Aluminum foil production
The aluminum foil used in electrolytic capacitors is a kind of corrosive material working under polar conditions. It has high requirements on the structure of aluminum foil. The aluminum foil used is divided into three types: cathode foil, thickness is 0.015mm~0.06mm; high pressure foil, 0.065mm~0.1mm, and it is required to produce aluminum foil with high purity aluminum; low pressure foil with thickness of 0.06mm~0.1mm. Moreover, the use of aluminum foil is different from aluminum foil for packaging. The surface requirements of aluminum foil are very strict. Here, we mainly introduce the production process of electronic foil and the application of temperature control instrument in this process.
Production steps
The first step, smelting: The primary aluminum is converted into aluminum liquid by a large-capacity regenerative melting furnace, and enters the casting mill through the launder. During the flow of the aluminum liquid, the refining agent Al-Ti-B is added online to form a continuous uniformity. The refining effect; the graphite rotor degassing and removing slag on the line at 730-735 °C, forming a continuous uniform cleaning effect;
In the first step of the process, the melting of the original aluminum is relatively simple; but to control the graphite degassing, slag removal requirements are relatively high, most of the selection of AI-708AK3L1 can be basically satisfied, the parameter settings are relatively simple, the instrument interior The parameter Ctrl M5 P T is written by the instrument self-tuning. The parameter to be set is HIAL=740 SN=0 CF=0. Other parameters can be kept at the factory value.
The second step, rough rolling: The aluminum liquid after the first melting is introduced into the casting and rolling mill into a blank; in this process, the cooling water flow in the inner cavity of the roller is controlled to a certain range so that the outlet water temperature is controlled at 28- 32 ° C, the aluminum melt static pressure between the roll gap is controlled at 0.004-0.005Mpa, to ensure the material's crystal direction {100} face ratio>95%, grain size ≤5μm, rolling out 6.5-7.5mm slab;
By controlling the opening degree of the inlet valve, the temperature of the outlet can be controlled. Select the instrument model: AI-808AX3L1, where the parameter setting of the instrument is Ctrl, M5, P, t written by the instrument self-tuning, the parameter to be set is HIAL=34, SN = 21, CF = 1. Other parameters remain at factory values.
Third step, intermediate rolling: The slab is re-rolled by a cold rolling mill to a thickness of 4.5 mm, which is fed into an annealing furnace and annealed according to the following process.
In this process, the instrument of AI-708PAK3L1 is selected as the temperature control, and the parameters and curves are set as follows:
Parameter setting: HIAL=600, DLAL=3.0, SN=O, OPT=0, CF=0, RUN=27
The curve is set as follows: C01=30, t01=30
C02=360, t02=120
C03=360, t03=30
C04=580, t03=1080
C05=580, t05=-121
After heating from room temperature to 360 ℃, after holding for 2 hours, heating is continued to 580 ℃, and kept for 18 hours, and homogenization annealing is performed to make the crystal grain size uniform and the directionality uniform;
The annealed 4.5 mm thick aluminum foil was continuously cold rolled in a cold rolling mill to 0.60 mm, and again fed into an annealing furnace, and annealing was continued according to the following process.
In this process, the instrument of AI-708PAK3L1 is selected as the temperature control as in the previous process. The parameters and curves are set as follows:
Parameter setting: HIAL=480, DLAL=3.0, SN=O, OPT=0, CF=0, RUN=27
The curve is set as follows: C01=30, t01=30
C02=460, t02=300
C03=460, t03=30
C04=400, t03=420
C05=400, t05=-121
After heating to 460℃, holding for 5 hours, cooling to 400℃, holding for 7 hours, intermediate annealing; then continue rolling to a thickness of 0.3 mm as aluminum foil wool;
Fourth step, foil rolling: The above-mentioned 0.3 mm aluminum foil wool was rolled into a finished aluminum foil by a four-roller irreversible foil rolling mill.
Fourth, summary:
The production of aluminum foil for electrolytic capacitors in our country is relatively backward, mostly relying on imports. With the maturity of the production process, the production of aluminum foil for electronic use is relatively mature. The aluminum foil production process described above is short, the operation cost is low, the production investment scale is small, and the quality of the ultra-thin aluminum foil produced can reach the most advanced level in the world, and the temperature control instrument plays a key role in the whole process. Annealing of gas to aluminum foil. So grasping the whole process plays an important role in introducing and promoting our company's instruments to our customers.