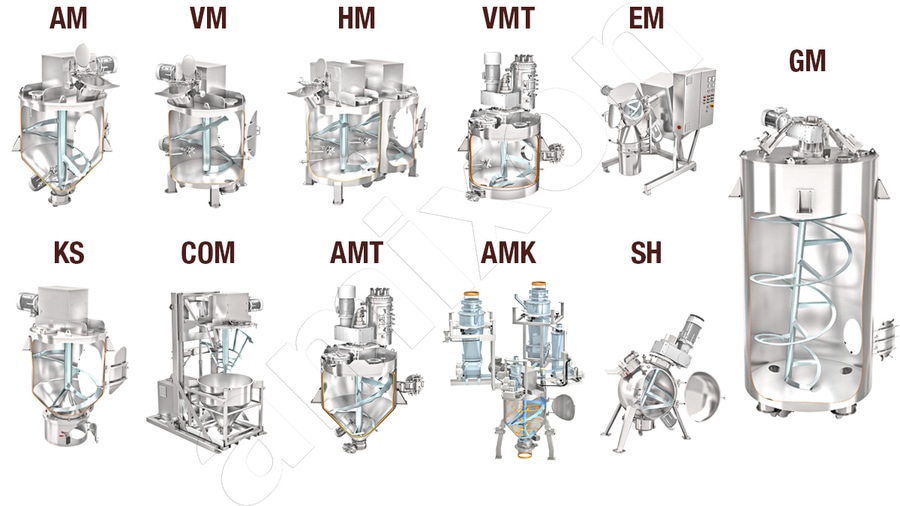
#Product Trends
Mixing plants for powder preparation of chemical and pharmaceutical active ingredients
Chemical synthesis produces pure, concentrated active substances. Precision is vital in formulation for market release. The closed "containment" process safeguards against dust, ensuring tightness in engineering systems.
Powdered active ingredients from chemical synthesis are highly pure and highly concentrated. This high concentration can also be dangerous. Before the active ingredients can be marketed, they have to be converted into a user-friendly form using filling agents.
This type of formulation is understood to include both dilution by carriers and adjustment of particle size by size reduction, build-up granulation, fluidized bed agglomeration or compaction, and binding of any dusts that may be present. In special cases, the active ingredient particles are coated with a protective film.
The final mixing process is of particular importance. It must ensure the absolutely uniform distribution of the active substance in the carrier substance. In addition, the mixer must effectively deagglomerate. In some cases, liquid additives are mixed in. The distribution of these particles must be micro-fine. In this way, unwanted dusts can be bound. The surface activity of the active ingredient particles must not be changed in the process.
The formulation process must take place in a completely closed system (containment). No dust may escape from the system and no foreign substances may enter the active ingredient mixture.
"Containment" in this context also means the technical protection of operating personnel and the environment from the mixtures of active substances. The permanent tightness of a process plant is not a trivial matter. In the case of powder mixers and synthesis reactors, seals on shaft feedthroughs should be mentioned first and foremost. One part of the sealing system is stationary, the other part (the shaft surface) moves with more or less speed. The peripheral speeds can be 8 m/s and more. The bulk goods in the mixing container can be abrasive, adhesive, curing, nanoparticulate dusting and toxic.
In addition, the mixing goods in the mixing container may be under pressure. Differential pressures of minus 1, plus 3 bar, 6 bar or even 25 bar are not uncommon. Although the problem of shaft penetration and sealing is more than 100 years old, there is still no universal solution for permanent tightness. Labyrinth seals, lip seals, flow gap seals, stuffing box packings, mechanical seals; single and double acting, dry running, liquid or gas lubricated, ..... and combinations of different seal types. The topic is and remains highly topical. amixon® has gathered a great deal of experience over forty years and has developed many tried-and-tested solutions. Matched to the respective product and the preparation task in the mixer, the most economical solution is offered.
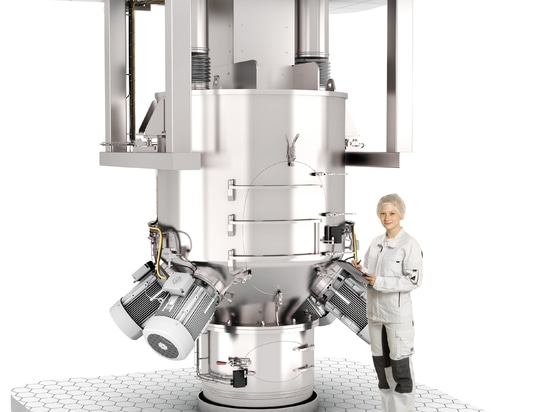