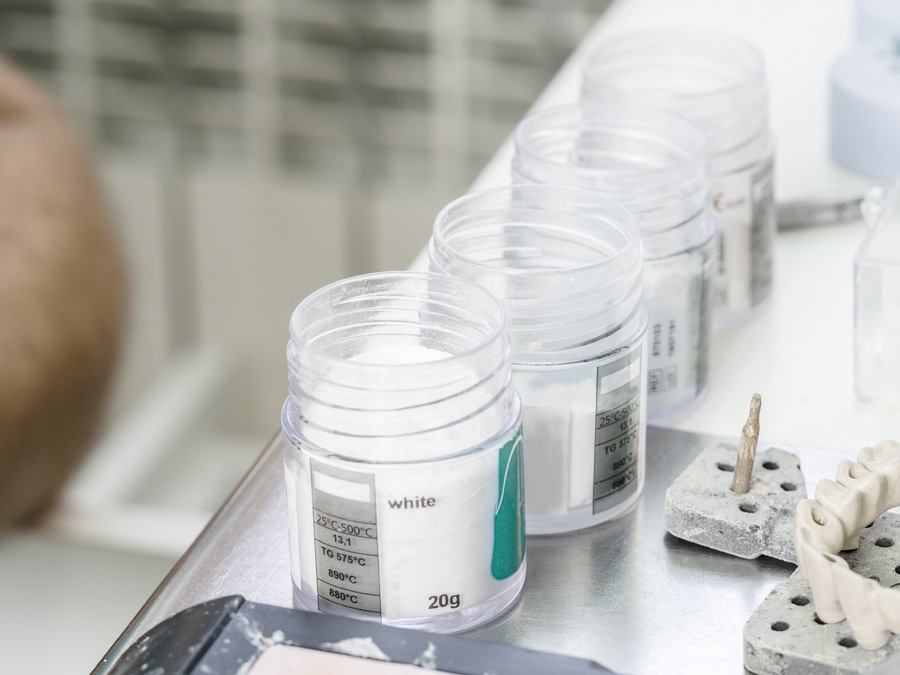
#Industry News
Vertical mixers prepare high performance ceramics
In the production of technical ceramics, there are many parallels to the powder metallurgy. The raw materials used are expensive. These are oxides, nitrides, carbides or borides of high-purity metals.
Alongside plastics, ceramic materials are considered to have the greatest potential for development because of their unique stability, temperature resistance and durability. Engineering ceramics are used as a high-temperature-resistant material in power generation, as corrosion, acid and wear protection in apparatus engineering, and as high-frequency semiconductors in communications engineering.
In the production of technical ceramics, there are many parallels to the powder metallurgy. The raw materials used are expensive. These are oxides, nitrides, carbides or borides of high-purity metals. Examples are aluminum oxide, aluminum titanate, silicon carbide, silicon nitride and zirconium oxide. Due to their brittleness, ceramic components are prone to "critical failure". In the manufacture of advanced ceramics, therefore, the highest degree of purity must be ensured.
Ceramics have unique properties
Ceramics have unique specific properties unmatched by any other group of materials: extreme strength, high heat resistance, acid resistance, ductility, electrical and thermal conductivity, electrical insulation, optical refraction, transparency, color depth, etc.
Ceramic powders are prepared with the greatest care. In some cases, the starting components are converted to a state with an extremely high specific surface area. The particle sizes are smaller than 0.01 µm. This type of particle size reduction requires a high energy input.
Such small particles tend to agglomerate spontaneously. The agglomerates must be separated (deagglomerated) back into primary particles to ensure a uniform microstructure of the sintered material. The process chain is long: Raw material extraction from the chemical industry, defined surface enlargement, chemical breakdown, sieving, doping, homogenisation, dispersion in the wet phase, solid-liquid separation up to thermal drying, homogenisation/blending. The material diffusion takes place at high sintering temperatures in the calcining furnace. Cooling completes the first synthesis step. This is followed by similar or different preparation steps, which again start with grinding and mixing. If the composite contains plastic polymers, synthesis reactions can take place dry, wet and gaseous in the amixon® mixer.
Many small batches are homogenized into one large batch
Most of the processes take place in continuously operating process equipment, the parameter settings of which have to be determined from upstream substance analyses. In this respect, the continuous individual steps must be carried out in sections and the intermediate products collected as batches in containers, silos, mixers or big bags. For representative analyses, a homogenous total mass must be assumed. The batch sizes to be homogenized in powder metallurgy vary between 5 l and 20 000 l. amixon® mixers are successfully used to achieve ideal mixing qualities. The three-dimensional circulation flow guarantees short mixing times.
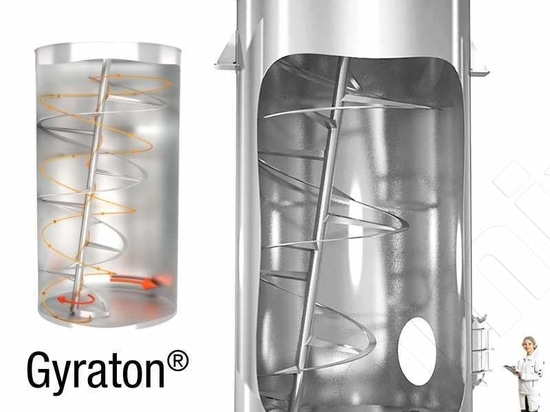