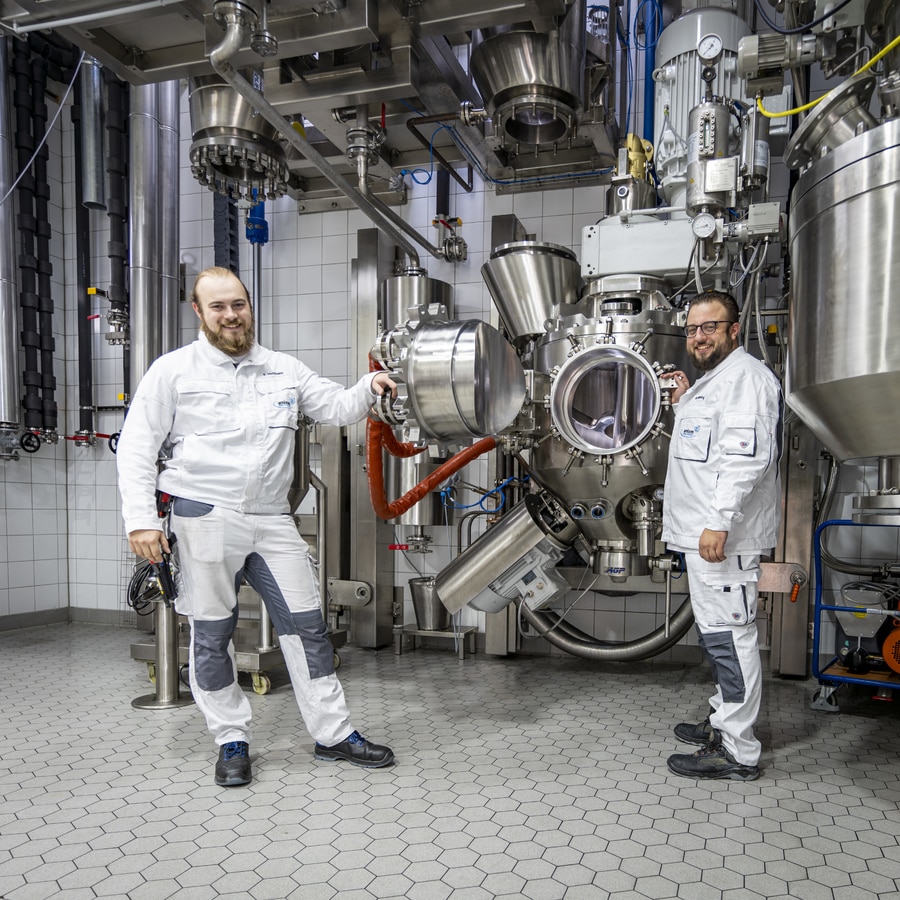
#Product Trends
Efficient forms of diffusion in technical ceramics and powder metallurgy
Diffusion plays an important role in powder metallurgy when foreign materials in finely dispersed form are pressed into a shaped body. In this case, one speaks of a "mechanical alloy".
Diffusion plays an important role in powder metallurgy when foreign materials in finely dispersed form are pressed into a shaped body. In this case, one speaks of a "mechanical alloy".
So-called foreign diffusion takes place at the phase boundaries, grain boundaries and surfaces of the microstructure. Atomic groups from regions of higher potential slowly migrate to regions of lower potential. These processes are more intense the smaller the microstructural particles involved are and the more they are pressed against each other.
Diffusion can be a suitable method for doping high-performance materials by introducing foreign atoms into disrupted lattice structures. Diffusion is particularly strong when concentration gradients meet in the form of nanoscale powders. This is particularly the case at phase and grain boundaries.
Diffusion is particularly strong,
1. when the goods are present as nanofine dispersions.
2. if there is as large a concentration gradient as possible.
3. when the process temperatures are high.
4. when particles with high concentration meet particles with low concentration as often as possible.
5. when the particles slide closely along each other - without being surrounded by a gaseous phase.
Accelerated diffusion in the amixon® reactor
to 1)
The mixing process in the amixon® reactor is always free of dead space and efficient - regardless of the speed of the mixing tool. The flow properties of the mixing goods - dry, moist, wet or suspended - are irrelevant. In addition, the precision mixing takes place regardless of the filling level.
to 2)
In the amixon® reactor, the components can be in any aggregate state to diffuse into each other: dry, liquid or gaseous.
to 3)
amixon® reactors can run predetermined heating/cooling curves with an accuracy of a few tenths of a Kelvin. Up to 350 °C. Current further developments of amixon® even target temperatures above 600°C.
to 4)
The dead space free mixing process ensures that particles/liquids or gases are in constant and random contact with each other. An amixon® test reactor operates with up to 25 bar overpressure. (amixon® process plants meet the legal requirements of TA Luft. They are technically tight - even at high temperatures and pressures).
to 5)
Solid-solid reaction / diffusion: In the amixon® apparatus, a steep concentration gradient can be generated by applying a high vacuum. In single-phase mixtures (without gas phase), the solid particles rub closely together - even at high temperatures.
Please visit us in our test center. We cordially invite you to carry out trials with your original products.