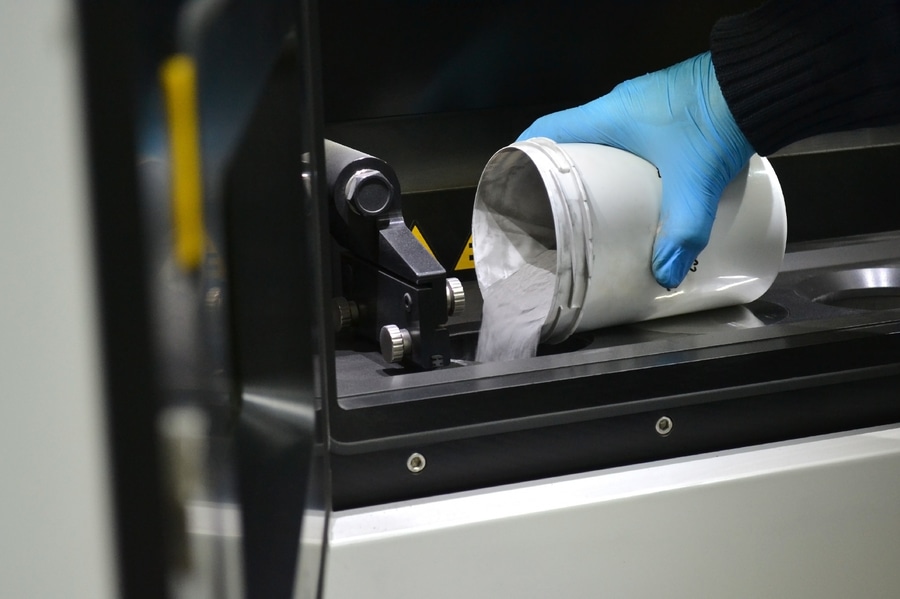
#Product Trends
Powder processing for additive manufacturing with industrial mixers
Mixing, vacuum drying, and reacting equipment plays a crucial role in the production and reconditioning of materials for powder-based 3D printing.
Powder bed 3D printing proceeds successively, layer by layer. For each layer of the structure, a powder bed is first laid to the desired thickness. Next, a precisely controlled energy source melts these clusters of powdery particles into the exact dimensions of the cross-section. Finally, surplus powders are removed, ideally to be repurposed for use in subsequent layers.
In order to achieve a functional end-product, the powders used in 3D printing must be adequately stable so that particle size, bulk density, and rheological characteristics remain unaffected by the melting process. At the same time, each step of the process must take place in quick succession if cost-efficiency is to be ensured. Speedy processing is usually aided by the implementation of pneumatic conveyance, which can often lead to a high degree of abrasion. For this reason, polymer powders used in 3D printing must be expertly conditioned.
This same challenge applies to selective laser micro sintering, a 3D manufacturing process that uses metallic powders. The metallic materials are laid into the powder bed by means of a doctor blade, a process that is often relatively time-intensive. The materials’ flowabiltiy characteristics play a decisive role in the resulting homogeneity of the powder bed. The powders must be as free-flowing as possible, requiring a spherical particle shape and a narrow particle size distribution. Additionally, agglomerates must be eliminated in order to prevent the formation of laminar or lineal defects in the finished component. Most metallic powders used in 3D printing are cohesive and have a particle size less than 10 µm, meaning they have a tendency toclump and adhere to the doctor blade or work surface. While this phenomenon is objectionable, it is alsodifficult to avoid.
In order to prevent the formation of unwanted agglomerates, 3D printing powders may be coated with nanoscopic additives as a means of conditioning them. Such a conditioning process is best performed in an automated precision mixer or fluidized bed processor, where clumping and unwanted agglomerates are less likely to form and the flowability characteristics of the powders can be improved.
The role of mixers, vacuum dryers, and synthesis reactors in the manufacturing of 3D printing powders
Mixing, drying, and reacting equipment plays an important role in powder metallurgy and the preparation of polymers for 3D printing. These devices must be incredibly precise, because it is only possible to create a nanoscopic coating on each individual particle by adding the coating agent to the mixture in minute dosages as a weak solution or suspension.
Homogenously integrating coating agents into bulk ingredients involves creating uniform levels of moisture within the powder. In order to achieve this, each and every individual particle must be wetted. If the liquid phase is ultimately to be dried, then the coating will remain evenly distributed upon the surface of each particle. Ideally the drying process will take place under a vacuum, reducing the both the duration and heat involved.
amixon® offers field-tested solutions to these complex processing challenges, drawing from over 37 years of experience. Our mixing equipment can even homogenously blend just 100g of nanodispersive soot into 35 tonnes of metallic powders. Nearly every piece of processing equipment created by amixon® is a one-of-a-kind prototype, unique in part due to minute yet decisive details designed for the specific processing needs of our customers from diverse industries. We offer end-users in-depth consultations with our processing engineers, giving them the opportunity to discuss their specific processing criteria in extreme detail. These consultations, the contents of which are protected by strict confidentially agreements, prove to be incredibly profitable for our customers.