
#Product Trends
amixon® large-scale mixers for baby food ensure the highest quality standards.
The demand for industrially produced infant formula from dry milk products in industrialized and emerging countries is very high, as are the requirements for the quality and composition of the mixed powders used.
The production of infant nutrition involves great responsibility and the high-quality processing of powdered raw materials in process-safe facilities is of utmost importance. The food must be clean, safe and healthy, because the intestinal flora of newborns develops only in the first years of life. There is a parallel with drugs from the pharmaceutical industry: If trace elements or vitamins are under- or overdosed, this will harm the infant.
amixon® mixers guarantee the highest mixing quality.
Micro-components such as probiotics or prebiotics, minerals and trace elements such as zinc, copper, selenium or chromium must be mixed in precisely . At the same time, mixing plants are required that operate with the lowest possible energy input and preserve the particle structure of the raw materials. Our claim: Dust-free, fast dispersing, reliable wetting, fast dissolving and homogeneous baby food. In addition, amixon® guarantees fast residue-free emptying of the powder mixers and compliance with the highest hygienic standards.
Modern filling and packaging machines for the production of baby food process volume flows of 20 m³ per hour, which corresponds to approximately 10 tons per hour. Accordingly, functioning logistics concepts are required for the provision of the individual components involved, their metering and the suitable mixing technology. If several filling lines are fed simultaneously, precise powder mixers with a batch volume of 10 m³ - 15 m³ are required. Our solution: The amixon® vertical twin-shaft mixer HM.
The mixing vessel consists of two cylinders, one inside the other. In their center rotate two SinConvex® mixing tools which have a pitch of approximately 30 degrees and generate a three-dimensional flow within the mixed material. The screw belt width allows almost a quarter of the mixed material to flow per revolution. Along the periphery of the mixing vessel, the powder initially flows upwards in a spiral. Once there, it flows back down along the mixing shaft due to gravity. The mixing effect occurs three-dimensionally within the boundary regions between the two macroflows.
Thanks to the dead-space-free flow, technically ideal mixing grades are thus achieved after approximately 20 to 90 revolutions, which cannot be optimized in practice . The mixing process is particularly gentle and energy-efficient. The peripheral speed of the mixing tool is usually between 0.5 m/s to 3 m/s and is adjustable.
Due to the design of our powder mixers, and because the flow effect takes place independently of the degree of filling, ideal mixing qualities can already be achieved with a degree of filling of approx. 10-15 percent.
40 years of know-how in mixing technology for baby food
Would you like to learn more about your benefits with amixon® mixing technology? Then contact us and we will convince you with demonstrations of elegant mixing processes. amixon has excellent demonstration machines on a 400-liter scale in Germany, the USA, China, Japan, India, Thailand and South Korea.
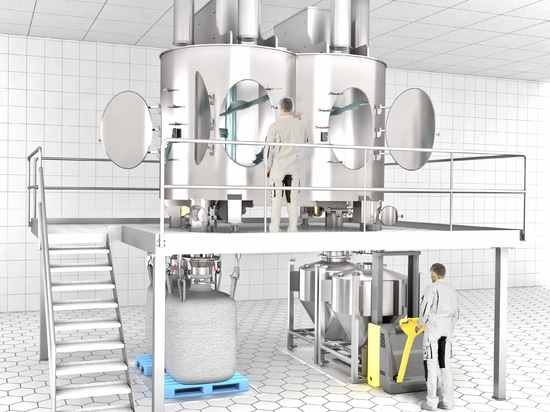