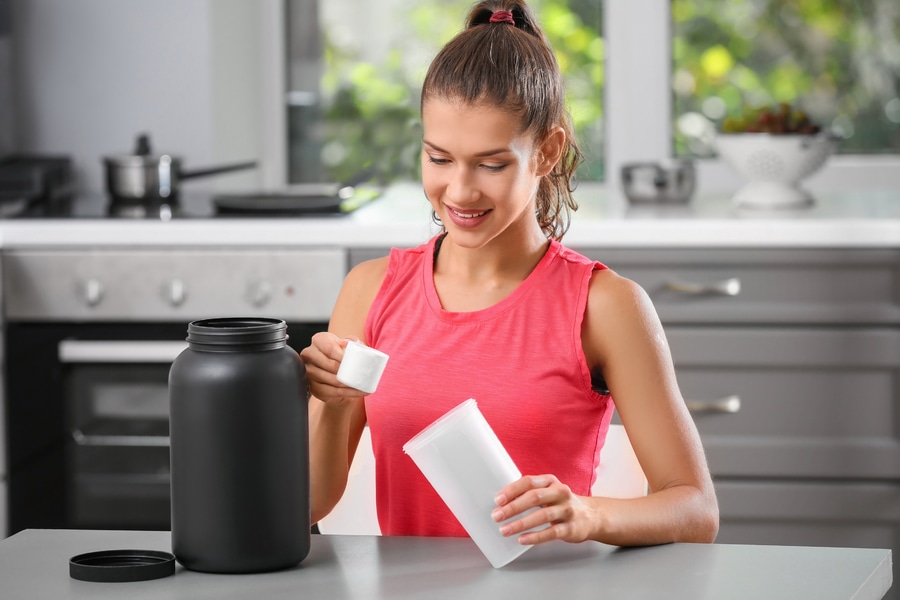
#Industry News
The right mix for health and more performance
Here we describe how amixon® powder mixers use innovative technologies to ensure uniform mixing, efficient dust binding and compliance with high hygiene standards.
Strictly regulated on the borderline to medicine
§ 1 of the Nem (Food Supplements Ordinance) defines food supplements as foodstuffs which:
1. are intended to supplement the general diet (intended use);
2. are a concentrate of nutrients or other substances with a nutritional or physiological effect, alone or in combination (composition), and
3. are brought to the market in dose form, in particular in the form of capsules, pastilles, tablets, pills and other similar dosage forms, sachets of powder, ampoules of liquids, bottles with droppers and similar dosage forms of liquids and powders for ingestion in measured small quantities (dosage form).
Food supplements are therefore foods that serve to supplement the general diet with vitamins, minerals or other substances such as amino acids, dietary fibres or secondary plant substances. They contain the nutritionally effective nutrients in concentrated form and in dosed quantities.
Demarcation from drugs is not always easy. Food supplements must not have pharmacological properties, as required by the definition of medicinal products in § 2 of the German Medicines Act (AMG), or give the consumer such an impression.
Production according to pharmaceutical guidelines
The requirements for the production technology used to prepare FS for pleasant intake by the consumer, correspond to those for food and pharmaceutical production according to relevant technical specifications as specified by GMP/FDA.
Because ever newer packaging variants and ingredients for FS are entering the market, many manufacturers rely on the services of contract manufacturers. They know the high demands in production very well and are able to produce the required outstanding and consistent quality.
FS manufacturers take advantage of the production flexibility of contract manufacturers and their readiness to tackle new challenges. This is because the different dosage forms require different, sometimes specialised and investment-intensive, manufacturing and packaging processes.
Good residual emptying saves a lot of time and money
The amixon® precision mixer HM 7000 shown here can mix batches of up to 7 m³ of mix. The result is an ideal random mix that can no longer be improved in practice - regardless of whether the filling level is only 1,000 litres or the nominal filling level of 7,000 litres is used. It should be emphasised that amixon® mixers mix very gently. In this case, the peripheral speed of the mixing tools is only 1.3 metres per second. Despite this, the mixing time is only 4 minutes.
The spiral mixing tools were retrofitted with ComDisc®. This enables an effective residual discharge of up to 99.9 %. The residual quantity is less than 5 kg. ComDisc® removes mix residues from the floor - similar to a windscreen wiper. This happens automatically. The mixer remains closed until it is completely emptied. The large inspection doors are used for checking.
Cleaning efficiency determines the degree of flexibility
Due to frequent recipe changes and because of the strict specifications for pharmaceutical production, the mixers used in the production of FS should be validatable in a short time and easy to clean.
The installation and operation of the mixer is ensured during the qualification process. For validation, the mixing and cleaning processes must also be checked for conformity to the defined specifications. If a mixer does not pass this qualification, it cannot be used in production according to the specifications.
During wet cleaning of a precision mixer, for example, rotating washing heads are lowered/inserted into the mixing chamber from above and from the side. At the same time, the mixing tools rotate and ensure that all surfaces in contact with the product are flushed with water. The wash water is discharged at the lowest point in the bottom of the mixer.
Since the heat capacity of stainless steel is only 11 percent of the heat capacity of water, the mixer heats up very quickly when cleaned with warm water. That is why the machine dries more quickly afterwards. As a rule, no detergents are needed for cleaning.
Multi-stage wet cleaning is only needed if very intensive colours or aromas have been processed. It consists of pre-wetting, foaming and rinsing. The same applies when liquids have to be mixed in micro-droplets into a powder and consequently unwanted adhesions have to be washed off. Given good organisation, washing and drying takes an hour.
For good process efficiency, it is the small constants that ultimately influence the cost of producing the FS. So if set-up and cleaning times can be clearly planned and are short, and the product quantities to be discarded are low, the bottom line is higher margins for the food supplement manufacturer.
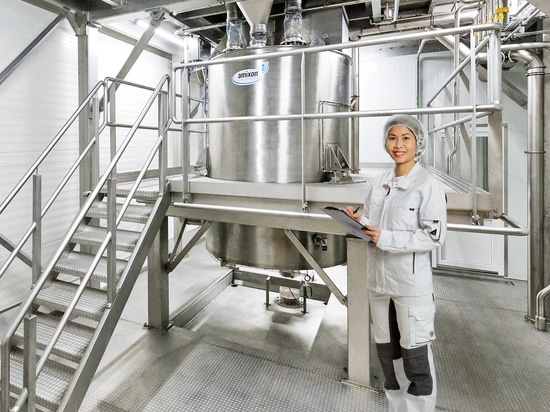