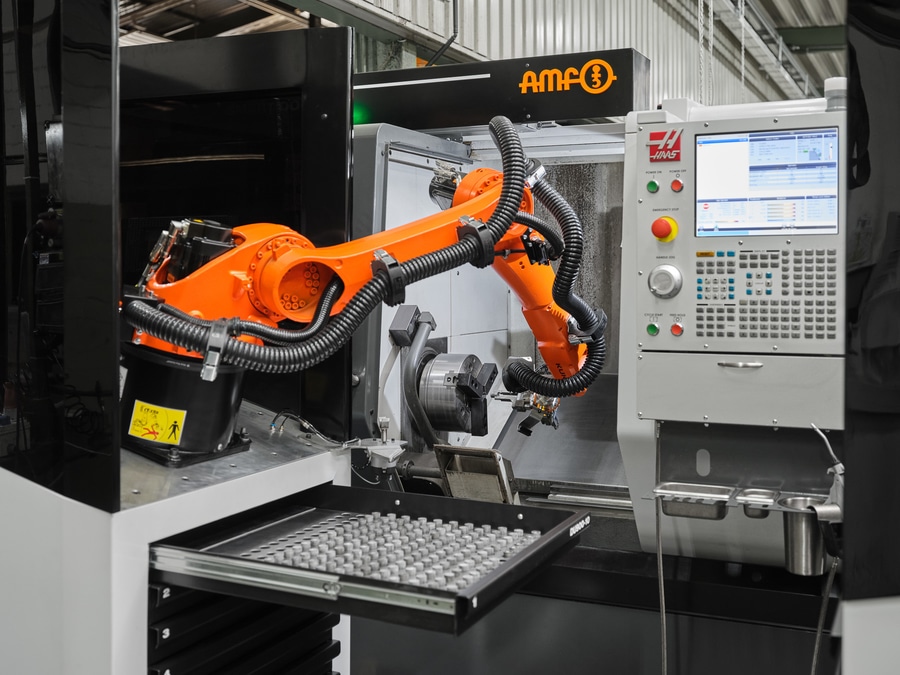
#Product Trends
AMF loading system fulfils trade fair promise and increases vertical integration for the user
Automated for greater independence and higher delivery performance.
(Ebersbach/Fellbach) At the EMO in autumn 2023, it was the celebrated star at the trade fair stand of Andreas Maier GmbH & Co. KG (AMF). Swarmed around and marvelled at, the Smart Automation loading system attracted attention and interest. Just a short time later, Güthle Pressenspannen GmbH became the first production company to benefit from the flexible robot loading system for automated workpiece handling. The smart, slim and flexible loading cell with very little space requirement not only ensures greater productivity, but in-particular, for more independence. Attached to an existing lathe, it ensures reliable and unmanned continuous loading and unloading. And thanks to its smart sister opposite, the parts arrive spotlessly clean for further processing.
"The fact that we may be the first to use the new AMF loading system is a nice note on the side. What is much more important, however, is what Smart Automation brings us in terms of independence," emphasises Wolfgang Stein, Site Manager at Güthle Pressenspannen GmbH. The new, flexible Smart Automation robot loading system from AMF automates the workpiece handling of ball sockets on the Haas lathe. They now manufacture these parts, which are important for their main product, themselves in Ebersbach an der Fils near Stuttgart instead of having to continue buying them in. Each year, up to 10,000 of the pressed metal parts are turned to size in four variants. The workpieces are loaded and unloaded by the robot. For this purpose, Smart Door automatically opens and closes the door to the lathe before the workpieces are cleaned in the Smart Cleaning system positioned opposite and then sent to hardening.
Systems for effortless tool changes
"The decision in favour of this wonderfully interacting ensemble is not necessarily based on economic considerations. It also enables us to reduce risks in the supply chain and meet our customers' deadlines more reliably," explains Wolfgang Stein. Wolfgang Stein does not fail to mention that this also relieves the burden on warehouse management and reduces storage costs. Güthle, which celebrates its 100th anniversary next year, is known for its Rollbloc and Dilos changing systems up to more than 60 tonnes tool weight. The ball strips, which depending on the tool size and weight contain 2-28 balls, are decisive for their success. These balls are pressed into the ball sockets. This makes it easy to insert tools into a machine.
Until that time comes, the AMF innovations have to do their job reliably. "his starts with programming, which can be completed intuitively on the screen without any programming knowledge," promises Product Manager Maximilian Gress from AMF in Fellbach. This is particularly important when the quantities of production orders are becoming ever smaller and more diverse. A decisive factor for Güthle is also the small space requirement of Smart Automation. At 930 x 960 mm, the loading cell requires less than one square metre of floor space and has the smallest footprint on the market. This means that the operator can access the machine at any time. Naturally, the robot has already come to a standstill until then. This is because a floor scanner acts as a space-saving alternative to an enclosure in and ensures safety of the employee by slowing the robot down and then by stopping it completely.
Sophisticated design with the smallest space requirement on the market
AMF implements the small footprint by placing the KUKA 6-axis robot with a load-bearing capacity of 10 kg on the top instead of on the side. Underneath, there is a workpiece trolley with ten drawers with grid plates that the robot opens and closes independently. Güthle places up to 2000 blanks and finished parts for the ball sockets made of tool steel in them. The four variants cover a diameter range from 18 to 36 millimetres. The workpiece trolley is pushed in from the rear. Because it stands on heavy-duty rollers, it can be easily moved in and out. If a second trolley is available, the drawers are loaded externally and parallel to production time. Güthle does not need this, as the Smart Cleaning sister unit opposite also contains a workpiece trolley with ten drawers - but more about this later.
In two clamping operations, the ball sockets are brought to their final dimensions by two turning operations. At the end of the 6-axis robot there is a double gripper with integrated blow-out. Thanks to the different gripper geometries, it can remove a finished part and insert a new blank in one cycle. An optional turning unit enables the machining of parts on all sides. This is not possible at Güthle, as the second clamping operation requires a different mounting. This means that all the first turning operations are carried out before all the second ones are completed after the mounting has been changed. To ensure that this runs smoothly and fully automatically, Güthle has also installed the Smart Door door opening from AMF. Smart Door is for machines without automatic door opening. The unit is compatible with all standard machine designs, can be easily retrofitted and programmed and is therefore also suitable for the Haas lathe. Cutting machine operator Ibah Koda also welcomes this: "I'm no longer so tied to this machine and can devote myself to other projects."
Power air from Smart Cleaning ensures clean components
Because Güthle not only wants to increase its delivery performance, but is also struggling with a shortage of skilled labour like many others, as a third element, the company has added the Smart Cleaning system from AMF, which is also brand new. Once the robot arm has removed a part with both grippers and inserted the next one, it guides the finished part into the Smart Cleaning unit positioned opposite. There it holds it in the air jet, which blows away chips and coolant via six nozzles. Meanwhile, the next workpiece is almost finished. "The interaction between the three units works perfectly," says an impressed Wolfgang Stein. "And because everything is set up so quickly, we can produce the parts to order without having to build up a large warehouse."
This is a major improvement for the production of Rollbloc bars, which Güthle introduced in 1978. In those days, Güthle revolutionised tool changes on presses. Tools weighing tonnes could suddenly be moved easily and positioned precisely. Together with the robust Dilos tool transporters and intelligent clamping technology, Güthle has become an important original equipment manufacturer for many press manufacturers. The fact that the in-house production of the ball sockets with the help of the three new AMF automation solutions ensures delivery performance certainly strengthens the position of Güthle with customers.
Eye on new applications after successful testing
Of course, neither the machine nor the automation units are fully utilised with the 10,000 parts per year. This is why Güthle is only now really starting to think about where else these flexible and mobile units could be used. Smart Automation can be moved and repositioned effortlessly and flexibly using a pallet truck. The same applies to Smart Cleaning. Product Manager Maximilian Gress encourages this. "We put a lot of thought into the design and came up with the best solution for all applications. This gives users a multifunctional and highly flexible loading cell for many applications."Wolfgang Stein concludes: "We scrutinise our production to see where AMF Smart Automation and "colleagues" can also increase process reliability and boost machine running time and productivity."
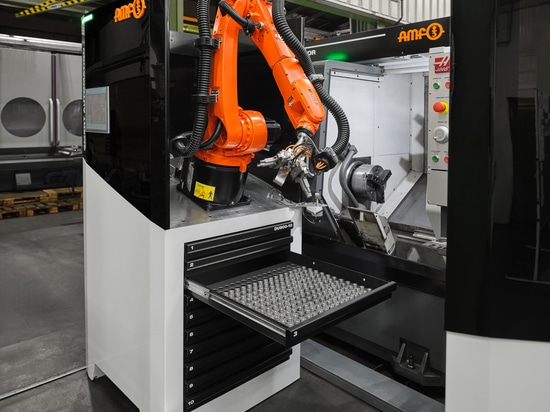
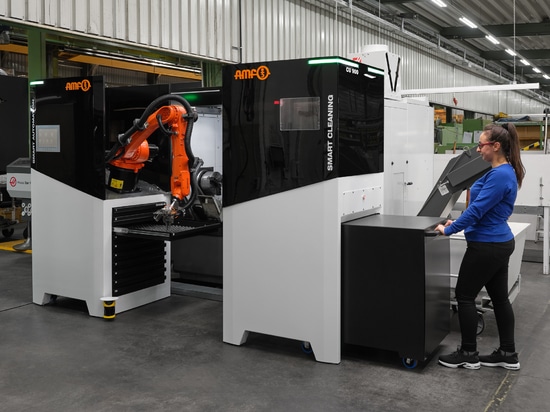
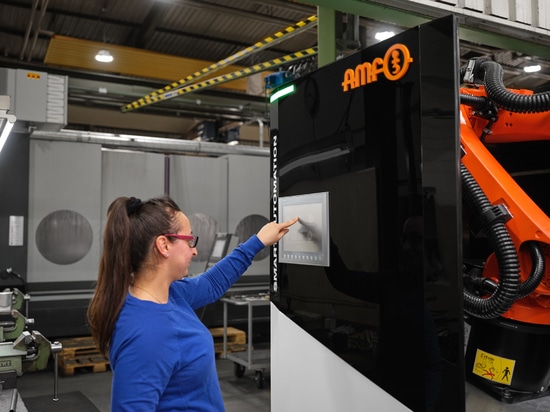
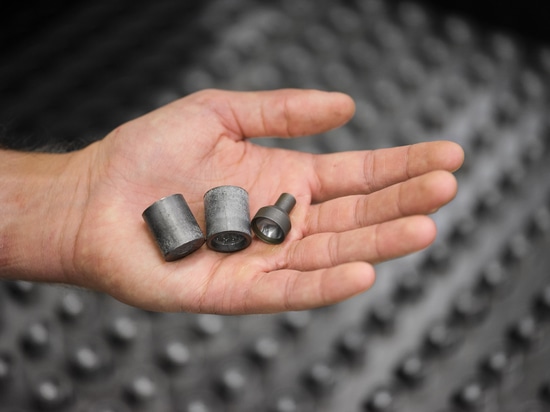
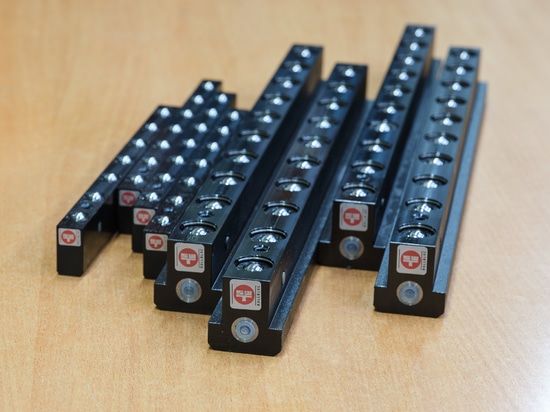
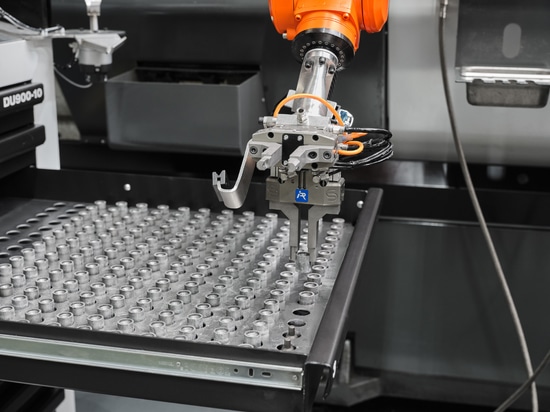
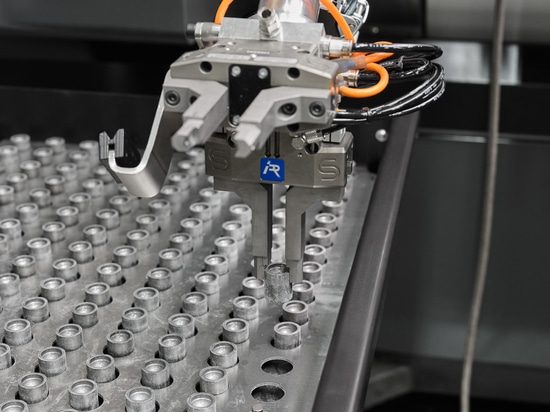
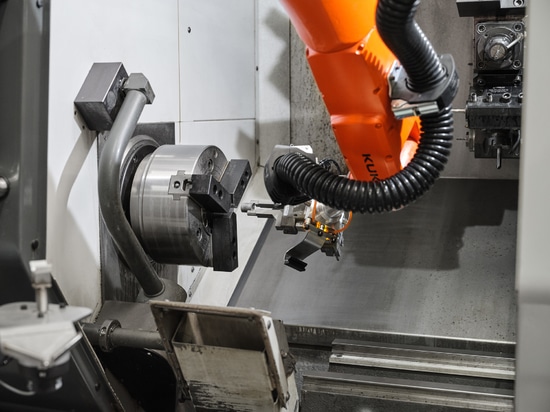
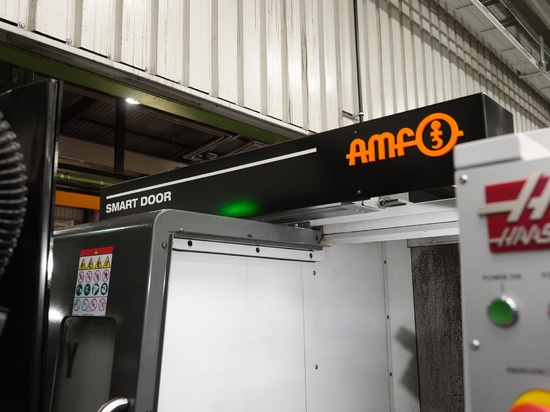
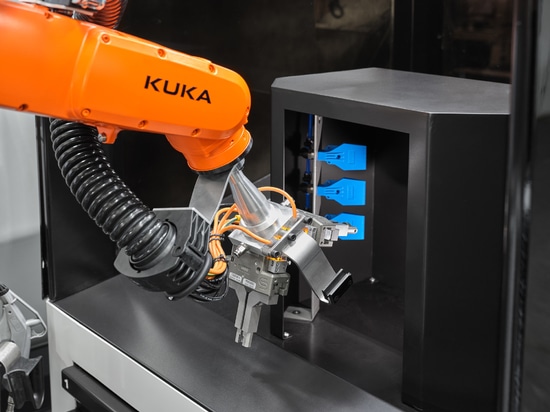
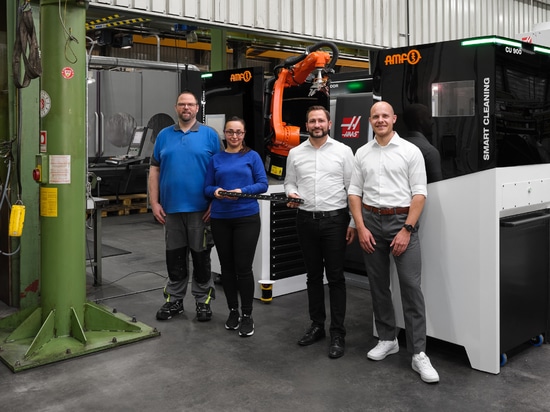