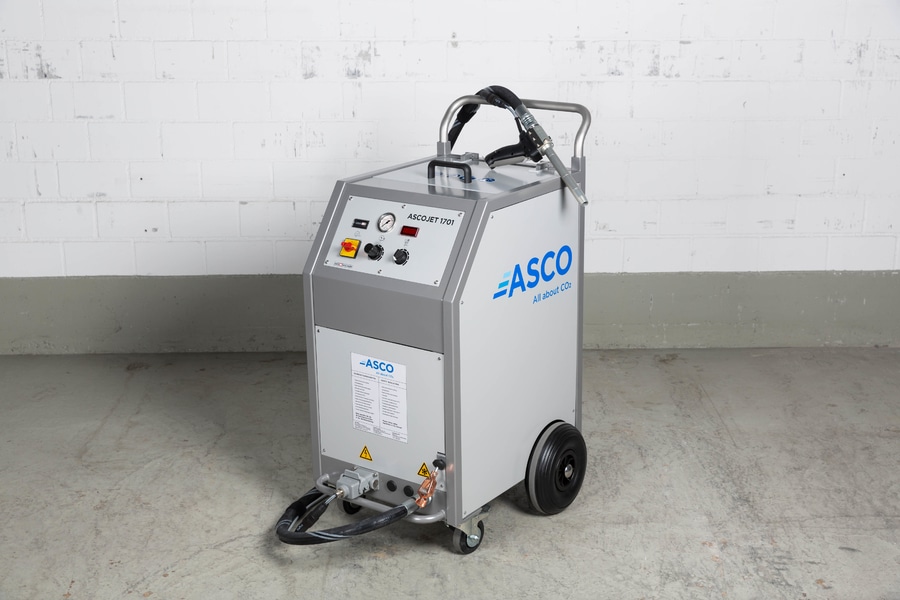
#Industry News
Lifetime of Casting Moulds at KSM Castings Group increased thanks to ASCOJET 1701
After an intensive selection process with other blasting units, the plant in Hildesheim decided on two ASCOJET 1701 dry ice blasting units at once
The KSM Castings Group spans the globe with production facilities in Germany, USA, China and the Czech Republic. With their products and solutions, they fulfil the core requirements of the markets: value-based service, conservation of resources and energy-efficient production.
The two ASCOJET 1701 dry ice blasting units are used to remove mould coatings and metal residues. "Due to its robustness and performance, the ASCO test unit stood out from those of the other manufacturers in the selection process. That is why KSM Castings Group decided to make ASCO Dry Ice Blasting Technology the standard at the Hildesheim plant at the beginning of 2021," says Mr Joachim Wikinger, Maintenance Gravity Die Casting, at KSM in Hildesheim. Parts of the moulds are blasted several times a day and a basic cleaning of the moulds, which means a complete blasting, is carried out once or twice a week or as required. The KSM Castings Group used to blast the moulds with sand, which shortened the life of the mould. Therefore, dry ice blasting is now used in all gravity die casting plants of KSM Castings Group.
The ASCO Dry Ice Blasting Process is a gentle and non-abrasive cleaning process. In contrast to conventional blasting methods with sand or glass beads, the cleaned surfaces are not damaged or changed. For example, closing surfaces of moulds are not rounded off and burr formation is thus avoided. In addition, the ASCO Dry Ice Blasting Process has the advantage that it can be carried out directly on the equipment. This eliminates expensive production downtimes. Even hot moulds, such as ingot moulds, can be cleaned directly in the process without being cooled down noticeably, which means that production can be resumed immediately after cleaning. The ASCO Dry Ice Blasting Process can thus be easily applied on a regular basis and integrated into the daily work process. In this way, this technology contributes to quality and process assurance with little effort.