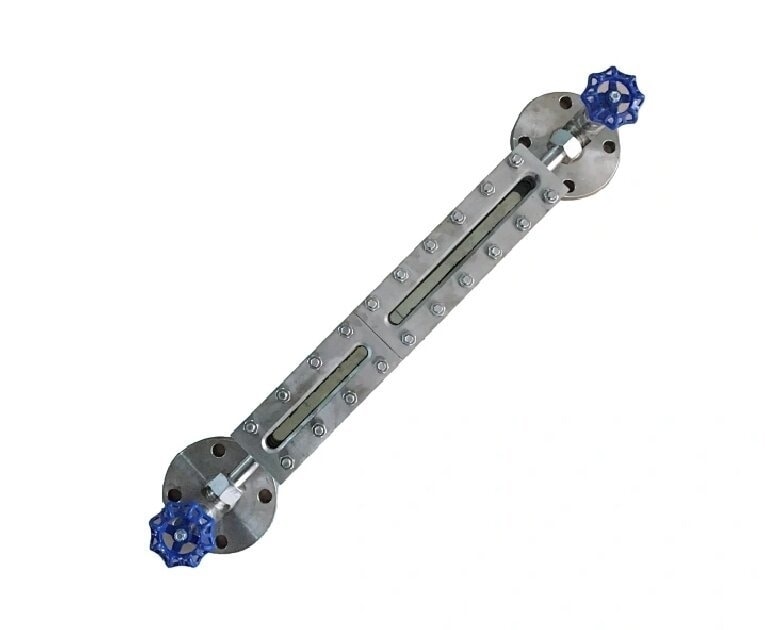
#Product Trends
Guide to Glass Plate Level Gauge
Essential level gauge: glass plate level gauge
Glass plate level gauges are crucial components in industries requiring precise monitoring of liquid levels in tanks and vessels. Their straightforward yet highly effective design makes them indispensable in applications ranging from chemical processing to water treatment facilities. Below is a comprehensive article from Athena examining their design, functionality, applications, and benefits.
What is a Glass Plate Level Gauge?
A glass plate level gauge is a device used to provide a direct visual indication of the liquid level inside a tank or vessel. It consists of a transparent glass plate mounted on the body of the gauge, which is connected to the vessel containing the liquid. As the liquid level changes, it can be observed directly through the glass plate. This simplicity of design ensures reliability and ease of use.
How Does a Glass Plate Level Gauge Work?
The working principle of a glass plate level gauge is straightforward. It relies on the hydrostatic principle, where the liquid level inside the tank corresponds to the liquid visible in the gauge. When installed, the gauge connects to the tank via top and bottom ports, creating a continuous flow path for the liquid. The level in the gauge mirror the tank level, offering a clear visual indicator.
Transparent Gauges: Both the liquid and gas phases are visible, allowing operators to observe the liquid’s color and clarity.
Reflex Gauges: These employ prismatic glass that enhances visibility by creating a high-contrast display between liquid and gas zones. The liquid appears dark due to light absorption, while the gas zones appear silvery or bright due to reflection.
Key Components of a Glass Plate Level Gauge
Glass Plate: Typically made from borosilicate glass, ensuring resistance to thermal shock and corrosion.
Body: Constructed from materials like stainless steel to withstand high pressures and aggressive fluids.
Valves: Installed at connection points for isolation during maintenance or emergencies.
Seals and Gaskets: Ensure a leak-proof design.
Vent and Drain Plugs: Facilitate cleaning and prevent sediment buildup.
Applications of Glass Plate Level Gauges
Glass plate level gauges are essential across various industries, especially where precise liquid level measurement and visual observation are critical. Here's a detailed look at their applications in different sectors:
Glass plate level gauges are valued across industries for their simplicity, reliability, and adaptability, ensuring precise liquid monitoring even in demanding conditions. With customization options available, they continue to evolve to meet diverse operational needs.
Limitations of Glass Plate Level Gauges
Fragility: Glass can be damaged under mechanical stress or sudden temperature changes.
Sediment and Scaling: These can obstruct visibility, necessitating regular cleaning.
Not Suitable for Opaque Liquids: Visual clarity is hindered when the liquid lacks transparency.
Comparing Glass Plate Level Gauges with Other Technologies
Magnetic Level Gauges: Offer non-invasive measurement and are ideal for hazardous liquids but lack the direct visibility of glass plate gauges.
Ultrasonic Level Sensors: Provide remote monitoring but are more expensive and require complex installation.
Reflex vs. Transparent Gauges: Reflex gauges enhance visibility for clear liquids, while transparent gauges allow for detailed inspection.
When to Choose a Glass Plate Level Gauge?
A glass plate level gauge is an ideal choice in scenarios where:
Direct, real-time observation of liquid levels is essential.
Cost-effective and simple solutions are required.
The liquid is transparent or semi-transparent.
Operating conditions include moderate to high pressure and temperature.
Maintenance Tips
To ensure long service life:
Regularly clean the glass to prevent sediment buildup.
Inspect seals and gaskets for wear and replace them when needed.
Use appropriate safety measures to handle glass under pressure.
By understanding the capabilities and limitations of glass plate level gauges, industries can ensure efficient and safe monitoring of liquid levels, tailoring their use to specific applications for optimal performance.