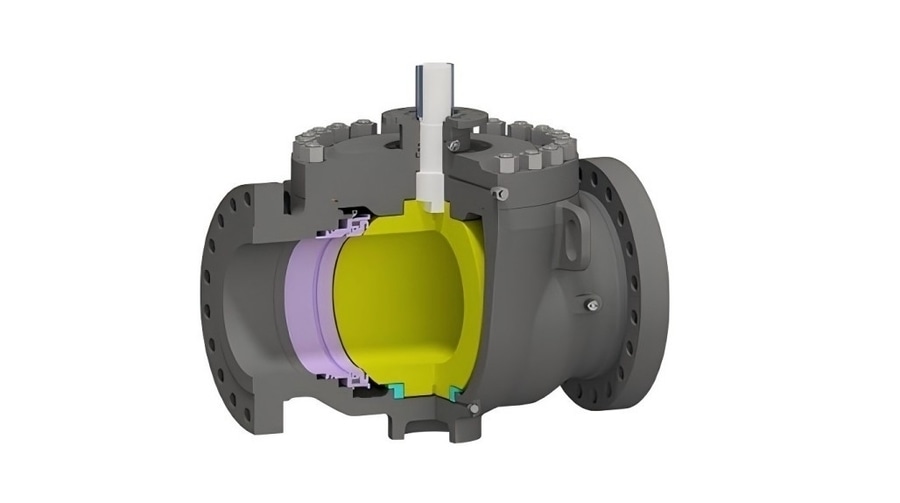
#White Papers
FAQs and Solutions About Top Entry Trunnion Mounted Ball Valve
Top Entry Trunnion Mounted Ball Valve
Top entry trunnion mounted ball valves are integral components in various industrial applications, offering advantages such as ease of maintenance and reliable performance. However, users have identified several concerns associated with these valves. Next, Athena delves into the primary issues and provides insights into their implications and potential solutions. Athena is a senior ball valve manufacturer from China, contact us to get more ball valve information.
1. Leakage Concerns about Top Entry Trunnion Mounted Ball Valve
Leakage is one of the most common issues encountered with top entry trunnion mounted ball valves. This can disrupt operations, lead to financial losses, and even cause safety hazards depending on the medium being handled. Below are some of the main causes of leakage and solutions to address them:
1.1 Worn-out Seals
Over time, the seals in a trunnion mounted ball valve can wear out due to constant operation, exposure to high temperatures, or contact with corrosive substances. When seals degrade, they fail to maintain a tight closure, leading to leaks.
Solutions:
Use high-quality seals made from materials compatible with the medium and operating conditions (e.g., PTFE or elastomers for chemical resistance).
Regularly inspect the valve and replace seals during scheduled maintenance intervals to prevent unexpected leaks.
Monitor operating conditions, such as pressure and temperature, to ensure they stay within the valve’s design specifications.
1.2 Improper Installation
Incorrect installation can cause misalignment between the ball and seats, resulting in leaks. This issue is particularly common when installation guidelines are not followed, or when inexperienced personnel handle the process.
Solutions:
Ensure that the valve is installed per the manufacturer’s instructions, including proper alignment of flanges and correct tightening of bolts.
Use trained and experienced technicians for installation and commissioning to minimize human errors.
Perform a hydrostatic test after installation to verify the valve’s sealing performance before full-scale operation.
1.3 Damage from Debris or Foreign Particles
Debris or foreign particles trapped between the ball and the seats can compromise the sealing surface and lead to leakage. This issue is especially common in systems without adequate filtration.
Solutions:
Install strainers or filters upstream of the valve to prevent debris from entering the valve body.
Schedule regular cleaning of the pipeline and the valve interior to remove any accumulated deposits.
Opt for a valve design with self-cleaning features, such as spring-loaded seats that allow small debris to pass through.
1.4 Thermal Expansion or Contraction
Extreme changes in temperature can cause the valve body, ball, or seats to expand or contract, potentially creating gaps that result in leakage.
Solutions:
Use valves designed for high-temperature applications, with materials that can withstand thermal expansion.
Employ thermal compensators to mitigate the effects of temperature fluctuations.
Monitor the operating temperature and avoid sudden temperature changes in the pipeline.
1.5 Corrosion or Material Degradation
Exposure to corrosive fluids or environments can weaken the valve’s materials, leading to surface pitting, erosion, or other forms of degradation that cause leaks.
Solutions:
Choose valves constructed from corrosion-resistant materials, such as stainless steel or duplex steel, for applications involving aggressive chemicals.
Apply anti-corrosion coatings or linings to the valve components to extend their lifespan.
Regularly inspect the valve body for signs of corrosion and replace compromised components promptly.
1.6 Pressure-induced Leaks
Excessive pressure within the pipeline can exceed the valve’s design limits, causing the seals to fail and resulting in leakage.
Solutions:
Verify that the valve’s pressure rating is suitable for the application before installation.
Install pressure relief devices, such as safety valves, to prevent overpressurization.
Regularly monitor pipeline pressure to ensure it remains within the valve’s operating range.
By addressing these common leakage concerns, operators can enhance the reliability and performance of top entry trunnion mounted ball valves, reducing downtime and ensuring safe, efficient operations.
2. Operational Challenges about Top Entry Trunnion Mounted Ball Valve
Top entry trunnion mounted ball valves are designed for durability and reliable operation, but certain operational challenges can arise over time, impacting their performance. These issues often stem from wear and tear, improper maintenance, or unsuitable operating conditions. Below is an in-depth exploration of common operational challenges and their solutions.
2.1 Valve Sticking
One of the most frequently reported issues is valve sticking, where the valve becomes difficult or impossible to operate. This can occur due to the accumulation of debris, corrosion of the internal components, or lack of proper lubrication. Sticking not only delays operations but can also lead to more serious mechanical failures if not addressed.
Causes:
Buildup of dirt, debris, or sediment within the valve mechanism.
Corrosion caused by exposure to moisture or aggressive chemicals.
Lack of regular maintenance and lubrication.
Solutions:
Implement a routine cleaning schedule to remove debris and sediment from the valve and pipeline.
Use anti-corrosion coatings or materials like stainless steel or Inconel for valves exposed to harsh environments.
Apply high-quality lubricants designed for ball valves to ensure smooth operation.
2.2 High Operating Torque
High operating torque refers to the excessive force required to open or close the valve. This challenge can make manual operation difficult and put strain on automated actuators.
Causes:
Wear and tear on the seats or ball, leading to increased friction.
Insufficient lubrication or use of inappropriate lubricants.
Misalignment during installation, creating uneven contact between components.
Solutions:
Conduct regular inspections to identify worn-out parts and replace them as needed.
Ensure proper lubrication using manufacturer-recommended lubricants.
Verify correct alignment during installation and make adjustments as necessary.
2.3 Slow or Inconsistent Operation
In some cases, users experience delays or inconsistency in valve operation. This can disrupt processes that rely on precise flow control.
Causes:
Malfunctioning actuators (for automated valves).
Blockage or damage to the valve stem.
Irregular pressure or temperature changes affecting valve components.
Solutions:
For automated systems, perform regular testing and maintenance of actuators to ensure reliable performance.
Inspect the valve stem for blockages or damage and replace defective parts.
Monitor pipeline conditions and implement safeguards to prevent sudden pressure or temperature spikes.
2.4 Noise and Vibration
Excessive noise or vibration during valve operation can indicate underlying mechanical issues or improper flow conditions. Left unaddressed, these problems can lead to damage or failure.
Causes:
Cavitation, where bubbles form and collapse within the valve due to rapid pressure changes.
Improper sizing of the valve, causing turbulence or unstable flow.
Loose internal components or worn-out parts.
Solutions:
Use valves with anti-cavitation features or install flow regulators to minimize pressure fluctuations.
Ensure proper valve sizing during system design to match the flow requirements.
Tighten or replace loose or worn-out components to prevent vibration.
2.5 Corrosion-related Failures
Corrosion can significantly impact the operation of top entry trunnion mounted ball valves, leading to partial or complete failure in opening or closing.
Causes:
Exposure to corrosive fluids or gases over prolonged periods.
Inadequate protection of valve materials or surfaces.
Solutions:
Select materials resistant to the specific corrosive agents in the application (e.g., stainless steel, duplex steel, or Hastelloy).
Apply protective coatings or linings to reduce corrosion risk.
Conduct periodic inspections to detect and address early signs of corrosion.
2.6 Pressure-induced Challenges
In high-pressure applications, operational difficulties can arise, such as difficulty in sealing or trouble maintaining a consistent flow rate.
Causes:
Exceeding the valve's pressure rating.
Uneven pressure distribution within the valve.
Solutions:
Choose a valve with a pressure rating appropriate for the application.
Install pressure regulators to ensure consistent and safe operating conditions.
2.7 Actuator Malfunctions (for Automated Valves)
For automated valves, actuator failures can disrupt operations, leading to delays or unplanned downtime.
Causes:
Power supply issues for electric actuators or pressure problems in pneumatic actuators.
Wear and tear of actuator components.
Solutions:
Conduct regular testing of actuators to identify and resolve potential malfunctions.
Use actuators designed for heavy-duty applications to match the operating conditions.
Maintain a backup power or air supply system to prevent operational delays during actuator failures.
3. Maintenance and Repair Issues about Top Entry Trunnion Mounted Ball Valve
Top entry trunnion mounted ball valves are often praised for their ease of maintenance due to their design, which allows access to internal components without removing the valve from the pipeline. However, certain maintenance and repair challenges persist, particularly in high-demand or critical applications. Understanding these issues and adopting best practices can enhance valve longevity and performance.
3.1 Sealant Injection Difficulties
Sealant injection is a common method to address minor leaks or improve valve sealing in emergencies. However, challenges can arise if the injection system is not functioning properly or if the wrong sealant is used.
Causes:
Blockage in the sealant injection port due to hardened or degraded sealant.
Use of incompatible or low-quality sealant that does not perform well under operating conditions.
Failure to maintain or test the injection system regularly.
Solutions:
Use high-quality, manufacturer-recommended sealants suited to the application’s temperature and pressure conditions.
Clean and inspect the sealant injection system periodically to prevent blockages.
Train maintenance staff on proper sealant injection procedures to ensure effective application during emergencies.
3.2 Component Wear and Tear
Continuous operation of the valve under high pressure, temperature, or abrasive conditions can lead to the wear and tear of critical components such as seats, seals, and the ball itself. Over time, this can result in reduced sealing performance or operational inefficiencies.
Causes:
High-frequency operation leading to mechanical fatigue.
Abrasion from solid particles in the fluid medium.
Exposure to corrosive or high-temperature environments.
Solutions:
Establish a preventive maintenance schedule that includes regular inspection and replacement of worn components.
Use durable materials like tungsten carbide-coated balls or reinforced seats for abrasive or high-stress environments.
Apply coatings or linings to critical components to protect against corrosion or wear.
3.3 Downtime for Maintenance
While the top entry design facilitates easier maintenance compared to side entry valves, it still requires shutting down the pipeline to access the valve's internal components. For systems that demand continuous operation, this downtime can be a significant drawback.
Causes:
Lack of redundancy in the system, making it impossible to isolate the valve for maintenance.
Time-consuming disassembly and reassembly of valve components.
Solutions:
Design systems with bypass lines or redundant valves to allow maintenance without disrupting operations.
Use quick-disconnect designs or specialized tools to reduce the time required for disassembly and reassembly.
Opt for advanced valve designs that allow maintenance under pressure, where feasible.
3.4 Difficulty in Diagnosing Issues
Identifying the exact cause of a valve failure or performance issue can be challenging, especially in large industrial systems. Misdiagnosis can lead to unnecessary repairs or component replacements, increasing maintenance costs.
Causes:
Lack of adequate diagnostic tools or instrumentation to monitor valve performance.
Inexperience or insufficient training of maintenance personnel.
Complex systems that make it difficult to isolate the valve for inspection.
Solutions:
Install diagnostic tools like position indicators, pressure sensors, or acoustic monitoring devices to detect anomalies in valve operation.
Train maintenance staff in troubleshooting techniques and the specific design of the valve being used.
Conduct regular performance testing and keep detailed records to track wear trends and identify issues early.
3.5 Handling of Large Valves
In industrial applications involving large-diameter pipelines, top entry trunnion mounted ball valves can be quite heavy and bulky. Maintenance or repair of such valves requires additional resources and specialized equipment.
Causes:
Large valves are often difficult to lift and maneuver due to their weight and size.
Disassembly of large valves requires significant time and effort, especially if lifting equipment is not readily available.
Solutions:
Use cranes, hoists, or other lifting equipment to handle large valves safely and efficiently.
Schedule maintenance during planned downtime to allow adequate time for handling and repairs.
Consider modular valve designs for easier disassembly and transport of components.
3.6 Access to Spare Parts
Timely repair of top entry trunnion mounted ball valves often depends on the availability of spare parts. Delays in procuring parts can extend downtime and disrupt operations.
Causes:
Limited availability of specific parts, especially for older or custom-designed valves.
Dependence on overseas suppliers, leading to longer lead times.
Solutions:
Partner with reliable valve manufacturers or suppliers to maintain an inventory of critical spare parts.
Standardize valve models across systems to simplify parts procurement and reduce inventory complexity.
Work with manufacturers to establish service agreements that guarantee faster delivery of replacement parts.
3.7 Corrosion and Erosion Damage
In applications involving corrosive fluids, erosion or corrosion of internal components is a significant maintenance concern. This damage can make repairs more complex and costly.
Causes:
Continuous exposure to corrosive chemicals or abrasive particles in the fluid.
Insufficient protective coatings or use of unsuitable materials.
Solutions:
Use corrosion-resistant materials like stainless steel, duplex steel, or Hastelloy for valve construction.
Apply specialized coatings or linings to protect against corrosion and erosion.
Conduct regular inspections to identify early signs of damage and replace affected components promptly.
4. Installation and Alignment Problems About Top Entry Trunnion Mounted Ball Valve
Proper installation and alignment are critical to ensuring the performance and longevity of a top entry trunnion mounted ball valve. Incorrect installation or misalignment can lead to operational inefficiencies, premature wear, and even complete valve failure. Here is a detailed look at common installation and alignment problems, their causes, and solutions.
4.1 Misalignment During Installation
Misalignment of the valve with the pipeline is a common issue that can create stress on the valve components and impair its operation. It may result in uneven torque, leaks, or improper sealing of the valve.
Causes:
Poorly aligned flanges or pipeline supports.
Lack of precision during the valve's placement or bolting process.
Use of inadequate tools or equipment for installation.
Solutions:
Conduct a detailed pre-installation check of the pipeline to ensure flanges are properly aligned and free of defects.
Use precision tools and measurement instruments to confirm alignment during installation.
Engage experienced technicians or follow manufacturer guidelines for correct positioning and assembly.
4.2 Over-tightening or Uneven Tightening of Bolts
During installation, bolts securing the valve to the flanges must be tightened evenly and to the correct torque. Over-tightening or uneven tightening can distort the valve body, causing sealing issues or damaging the internal components.
Causes:
Failure to use a torque wrench or follow torque specifications provided by the manufacturer.
Uneven tightening sequence, which creates an imbalance in the valve's placement.
Solutions:
Always use a torque wrench to tighten bolts to the manufacturer-recommended specifications.
Follow a crisscross tightening pattern to ensure even distribution of stress across the flanges.
Conduct a final inspection to verify the tightness of all bolts after installation.
4.3 Inadequate Support for the Valve
Large top entry trunnion mounted ball valves can be heavy, and improper support during installation can lead to misalignment or strain on the valve body and pipeline.
Causes:
Lack of proper lifting or support equipment for large valves.
Insufficient pipeline supports to bear the weight of the valve.
Solutions:
Use appropriate lifting tools, such as cranes or hoists, to handle heavy valves safely and precisely.
Provide additional pipeline supports or brackets near the valve to distribute the weight evenly and reduce stress.
Ensure the valve is secured firmly in place before connecting to the pipeline.
4.4 Improper Positioning of the Valve
The orientation of a top entry trunnion mounted ball valve is critical for its operation. Incorrect positioning can interfere with flow regulation, limit accessibility for maintenance, and increase the likelihood of failure.
Causes:
Installing the valve in a position not suited to its design (e.g., vertical installation when horizontal alignment is required).
Failure to account for access points needed for maintenance or repair.
Solutions:
Verify the recommended orientation and position in the manufacturer's installation manual.
Ensure the valve is installed in a location that allows easy access to the top entry for maintenance and repair.
Check that the valve's flow direction matches the pipeline’s flow requirements, using indicators or markings on the valve body.
4.5 Neglecting Pre-installation Inspections
Skipping pre-installation inspections can lead to undetected issues such as debris in the pipeline, flange imperfections, or damaged valve components, all of which can affect the valve's performance.
Causes:
Rushed installation processes without thorough preparation.
Lack of awareness of potential pipeline or valve defects.
Solutions:
Clean the pipeline thoroughly to remove debris, sediment, or foreign particles before valve installation.
Inspect flanges for any imperfections, such as warping or rough surfaces, and address them before connecting the valve.
Perform a visual inspection of the valve to check for damage during shipping or storage.
4.6 Improper Gasket Selection or Installation
Gaskets play a vital role in creating a tight seal between the valve and pipeline flanges. Using the wrong gasket material or installing it incorrectly can cause leaks or operational issues.
Causes:
Using gaskets that are incompatible with the valve or fluid being handled.
Poor alignment or incorrect tightening of the gasket.
Solutions:
Select gaskets made from materials that are compatible with the operating pressure, temperature, and fluid type.
Ensure proper alignment of the gasket between flanges during installation.
Tighten flange bolts evenly to create a uniform seal around the gasket.
4.7 Ignoring Thermal Expansion and Contraction
Pipelines and valves are subject to thermal expansion and contraction due to changes in operating temperature. Failing to account for this during installation can lead to stress on the valve body, misalignment, or leaks.
Causes:
Lack of consideration for temperature variations in the system.
Use of rigid connections that do not accommodate thermal movement.
Solutions:
Install expansion joints or flexible couplings near the valve to accommodate thermal movement in the pipeline.
Use materials for flanges and fasteners that can withstand temperature changes without deforming.
Verify that the valve's materials and design are appropriate for the expected temperature range.
4.8 Inadequate Testing After Installation
Skipping or insufficiently performing post-installation testing can leave undetected alignment or sealing issues that may affect the valve’s operation once the system is live.
Causes:
Rushing to commission the system without thorough testing.
Inadequate testing procedures or lack of proper equipment.
Solutions:
Conduct hydrostatic pressure tests to ensure the valve is sealed properly and does not leak under operating pressure.
Perform operational tests to verify that the valve opens and closes smoothly.
Inspect all connections and supports for alignment and stability before commissioning.
5. Material and Design Limitations About Top Entry Trunnion Mounted Ball Valve
While top entry trunnion mounted ball valves are renowned for their robust design and versatility, they are not without limitations when it comes to materials and design choices. These constraints can impact their suitability for certain applications, reduce performance under extreme conditions, or increase maintenance requirements. Identifying and addressing these limitations is crucial for ensuring efficient and reliable operation.
5.1 Material Compatibility Issues
The materials used in the construction of the valve body, ball, seats, and seals must be compatible with the media flowing through the valve. Failure to select appropriate materials can result in corrosion, erosion, or chemical degradation, leading to performance issues or valve failure.
Challenges:
Corrosion of valve components in highly acidic, alkaline, or saline environments.
Erosion caused by abrasive particles in the fluid medium.
Swelling, hardening, or degradation of seals and gaskets due to exposure to aggressive chemicals or high temperatures.
Solutions:
Use corrosion-resistant materials such as stainless steel, duplex steel, or Inconel for applications involving corrosive fluids.
Opt for erosion-resistant coatings like tungsten carbide or ceramic for valves exposed to abrasive media.
Choose seals and gaskets made from materials such as PTFE or elastomers that are specifically designed for chemical and temperature resistance.
5.2 Temperature and Pressure Constraints
Although trunnion mounted ball valves are robust, their performance may be limited by the material properties under extreme temperature and pressure conditions. This can lead to issues like material deformation, leakage, or even catastrophic failure.
Challenges:
Soft seat materials may degrade or lose elasticity at high temperatures.
Valve components may become brittle at extremely low temperatures.
Pressure ratings of the valve may not match the system's requirements, leading to potential blowouts or leaks.
Solutions:
For high-temperature applications, use metal seats or high-performance polymers that retain integrity at elevated temperatures.
For cryogenic applications, select valves made from materials specifically engineered for low-temperature performance, such as austenitic stainless steels.
Ensure the pressure rating of the valve matches or exceeds the maximum operating pressure of the system.
5.3 Limited Suitability for Certain Media
Top entry trunnion mounted ball valves are highly versatile but may not be the best choice for all media. For example, they may face challenges when handling slurries, highly viscous fluids, or solids-laden media.
Challenges:
Ball valves can trap solids between the ball and seats, leading to operational difficulties or damage.
Highly viscous fluids may require excessive force to operate the valve.
Slurries or media with solid particles can cause abrasion and wear on internal components.
Solutions:
For slurry or solids-laden media, consider using valves with self-cleaning or flushable designs to prevent particle buildup.
Use hardened or coated components to minimize wear in abrasive applications.
In cases where ball valves are unsuitable, consider alternate valve types, such as knife gate or pinch valves, for specific media.
5.4 Weight and Size Constraints
Top entry trunnion mounted ball valves are often larger and heavier than other types of ball valves due to their robust construction and added features. This can pose challenges in certain applications or installation scenarios.
Challenges:
The heavy weight of large valves may require additional support and specialized handling equipment during installation.
Limited space in some systems may not accommodate the bulkier top entry design.
Solutions:
Opt for compact valve designs where space constraints are a concern.
Use lightweight materials, such as aluminum or composite materials, for less demanding applications.
Ensure proper planning and structural support during installation to accommodate the valve’s size and weight.
5.5 Complexity of the Design
The advanced design of top entry trunnion mounted ball valves, while advantageous in many ways, also introduces complexity that can lead to increased manufacturing costs and potential operational challenges.
Challenges:
Precision machining and assembly requirements can increase production time and cost.
The complexity of the design may make troubleshooting and repairs more difficult for untrained personnel.
Solutions:
Work with trusted manufacturers who adhere to stringent quality control processes during production.
Train operators and maintenance staff to understand the valve’s design and functions thoroughly.
Standardize valve models across a facility to simplify training and reduce the learning curve.
5.6 Cost Considerations for High-Quality Materials
The use of premium materials such as stainless steel, duplex alloys, or corrosion-resistant coatings can significantly increase the upfront cost of top entry trunnion mounted ball valves. While these materials enhance durability and performance, they may not always align with budget constraints.
Challenges:
Higher initial investment compared to other valve types.
Increased cost for replacement parts made from specialized materials.
Solutions:
Perform a cost-benefit analysis to weigh the initial investment against long-term savings from reduced maintenance and extended service life.
Use high-quality materials only for critical components, such as the ball and seats, while employing cost-effective materials for less stressed parts.
Partner with reliable manufacturers who can provide affordable yet high-performance valve solutions.
5.7 Limited Flexibility in Extreme Environments
Despite their versatility, top entry trunnion mounted ball valves may have limitations in environments involving rapid temperature fluctuations, radioactive materials, or extreme pressures beyond standard ratings.
Challenges:
Thermal expansion or contraction of materials can impact valve performance in rapidly changing temperatures.
Exposure to radiation can degrade certain materials over time.
Extreme pressures or shock loads may exceed the design capabilities of standard valves.
Solutions:
Use valves with specialized materials and designs tailored for extreme environments, such as those used in nuclear or deep-sea applications.
Incorporate additional features like pressure relief mechanisms or flexible connectors to mitigate the impact of extreme conditions.
Conduct thorough application reviews and consult with valve manufacturers to select the most suitable design for challenging environments.
Conclusion
Top entry trunnion mounted ball valves offer significant advantages in industrial applications. However, addressing user concerns through regular maintenance, proper installation, and adherence to manufacturer (such as Athena ) guidelines is essential to ensure their optimal performance and longevity.