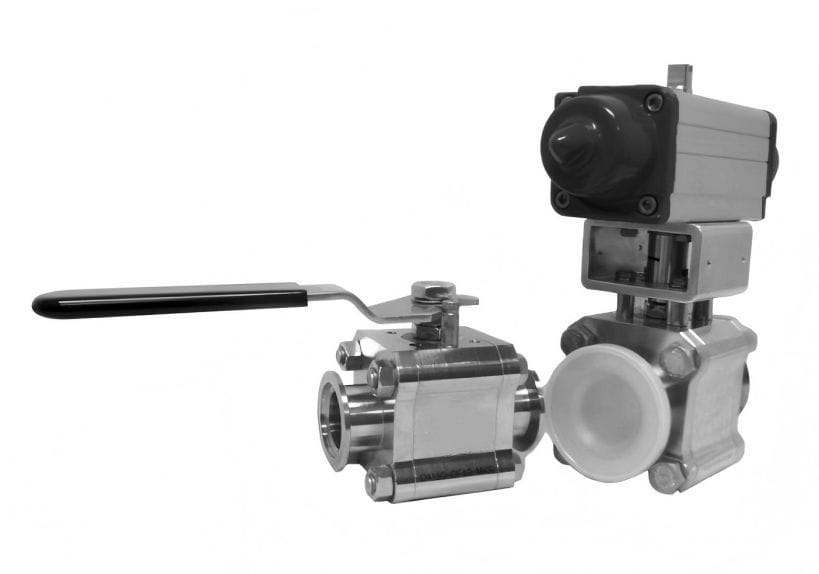
#Product Trends
What Are the Benefits of Using a Ball Valve for Vacuum Applications?
Ball Valve
Ball valves are widely used in vacuum systems due to their numerous advantages, making them an ideal choice for applications that require precise flow control, leak-proof sealing, and long-lasting durability. In this section, we will delve into the key benefits of using a ball valve for vacuum applications, focusing on the critical aspects that make them superior to other valve types in such environments.
1. Superior Leak Prevention
One of the most important benefits of using ball valves in vacuum applications is their exceptional leak prevention capabilities. In a vacuum system, maintaining a stable, low-pressure environment is crucial. Even the smallest leak can compromise system performance, introduce contaminants, or cause a loss of pressure that disrupts the process. Ball valves are designed to offer a robust, leak-tight seal, which is vital in maintaining the integrity of the vacuum.
Precise Sealing Mechanism:
Ball valves have a simple yet effective sealing mechanism. When the valve is closed, the ball’s smooth surface fits tightly against the valve seats, creating a seal that is virtually impervious to leakage. This makes ball valves ideal for environments where maintaining a vacuum is critical, such as in semiconductor manufacturing, pharmaceutical production, and research laboratories.
Use of Advanced Seal Materials:
The materials used for sealing in ball valves are specifically chosen to ensure they remain resilient and effective under low-pressure conditions. PTFE (Polytetrafluoroethylene) and PFA (perfluoroalkoxy) are commonly used as sealing materials in vacuum ball valves, offering excellent low-outgassing properties, which are crucial to maintaining a clean vacuum environment. These materials also resist wear, ensuring the valve will not degrade or lose its sealing ability over time.
2. Ease of Operation and Control
Ball valves are renowned for their easy operation, which is one of the key benefits in any application, including vacuum systems. Unlike more complicated valve types, ball valves are simple to operate and provide quick, precise flow control with minimal effort.
Simple and Fast Actuation:
The 90-degree turn required to open or close a ball valve means that operators can rapidly switch between open and closed positions. This quick actuation is essential in vacuum systems, where users may need to make rapid adjustments to maintain system pressure or to isolate certain sections of the system.
Manual or Automated Operation:
Ball valves are versatile in terms of actuation. While many vacuum systems use manual ball valves for simpler setups, they can also be fitted with automated actuators (e.g., pneumatic or electric) for more complex operations. Automated ball valves can be controlled remotely, allowing for precise adjustments without the need for manual intervention. This makes them especially useful in automated production lines or high-throughput processes, where continuous operation and precise control are required.
3. Durability and Longevity in Low-Pressure Conditions
Ball valves are highly durable, which is another significant advantage in vacuum applications. Since vacuum systems often operate continuously or over long periods of time, it’s important to have valves that can endure the harsh conditions associated with low-pressure environments.
Resistant to Wear and Tear:
In vacuum conditions, mechanical stress can cause wear on valve components. However, ball valves are constructed using corrosion-resistant materials like stainless steel or brass, ensuring they can withstand prolonged exposure to low pressures without deteriorating. The ball and seat materials are often engineered to resist abrasion and corrosion, further enhancing the valve's long-term reliability.
Minimal Maintenance Requirements:
The simple design of ball valves means fewer components that could potentially wear out or fail over time. With proper installation and minimal maintenance, a well-designed ball valve can function effectively for many years without significant degradation. This reliability and durability make them an economical choice for long-term operations in vacuum systems, where downtime is costly and undesirable.
4. High-Precision Flow Control
In vacuum systems, precise control of gases and liquids is often required to maintain specific pressures and flow rates. Ball valves excel in providing accurate flow control, making them an essential component in such systems.
Accurate Flow Adjustment:
Ball valves can be adjusted precisely to control the flow of gases or liquids within a vacuum system. This is especially important in industries like pharmaceutical manufacturing, semiconductor production, and chemical processing, where maintaining specific flow rates and pressure levels is essential for the success of the process. Even small fluctuations in flow can result in inconsistencies or defects in the product, making precise flow control a critical requirement.
Quick Response Time:
The design of a ball valve allows it to respond quickly to flow changes, which is important in dynamic vacuum systems where conditions can change rapidly. The ball’s 90-degree rotation ensures that operators can adjust the flow immediately, without the delays that might occur with more complex valve types. This fast response time helps maintain system stability and process consistency.
5. Low Internal Volume to Minimize Contamination
In high-purity vacuum applications, such as those in the semiconductor or pharmaceutical industries, minimizing contamination is crucial. Ball valves are designed with a low internal volume, which helps reduce the risk of contaminant buildup inside the valve body. This is particularly beneficial in environments where the introduction of external gases or particles can have serious negative effects.
Reduced Gas Trapping:
Ball valves are designed with a smooth, compact interior that prevents gases from being trapped in the valve body. This is important because trapped gases can disrupt the vacuum and potentially introduce impurities into the system. By minimizing internal volume, ball valves ensure that only the required gases are allowed into the system, maintaining the purity of the environment.
Contamination-Free Design:
Ball valves are often constructed from clean materials and undergo thorough cleaning processes to ensure they are free from any contaminants that could affect the vacuum system. Materials like stainless steel and PTFE are not only resistant to corrosion but also free of contaminants that could outgas into the vacuum. This is vital for maintaining the purity of the vacuum, particularly in industries where even the smallest particle can have detrimental effects on the final product.
6. Versatility and Adaptability to Various Vacuum Applications
Ball valves are incredibly versatile and adaptable, making them suitable for a wide range of vacuum applications. Their flexibility in terms of design and functionality makes them ideal for many industries, from research and development to large-scale manufacturing processes.
Wide Range of Configurations:
Ball valves come in a variety of configurations, including two-way, three-way, and multi-port designs. These different valve configurations allow for versatile flow control, making them adaptable to both simple and complex vacuum systems. For example, a multi-port ball valve can direct flow to multiple paths within a vacuum system, while a three-way ball valve can be used to isolate or divert flow as needed.
Suitability for Various Industries:
Ball valves are used in a variety of industries where vacuum systems are employed, including semiconductor manufacturing, chemical processing, pharmaceuticals, food packaging, and research laboratories. Their ability to handle low-pressure environments, provide precise control, and resist contamination makes them ideal for these diverse applications.
7. Cost-Effective and Efficient
In addition to their performance benefits, ball valves for vacuum systems are also cost-effective. Their durability, low maintenance requirements, and long lifespan contribute to reduced operational and repair costs over time. This makes them an excellent investment for businesses operating vacuum systems.
Reduced Downtime:
The reliability of ball valves means fewer instances of malfunction, leading to less downtime. This is crucial in high-demand environments where continuous operation is essential. Fewer maintenance interventions also mean less interruption to production or research processes.
Affordable Long-Term Solution:
Though the initial cost of a ball valve may be higher than some other valve types, the reduced maintenance costs and long service life make ball valves a more cost-effective solution over the long term. Their durability and efficiency also contribute to overall energy savings in vacuum systems, further improving their cost-effectiveness.
Conclusion
Ball valves offer a wide range of benefits for vacuum applications, including superior leak prevention, ease of operation, durability, precise flow control, and cost-effectiveness. Their ability to maintain a vacuum environment without compromising system integrity makes them essential for industries that rely on low-pressure environments. Whether for semiconductor manufacturing, chemical processing, or laboratory applications, ball valves provide the reliability, precision, and versatility needed to ensure that vacuum systems operate smoothly and efficiently.