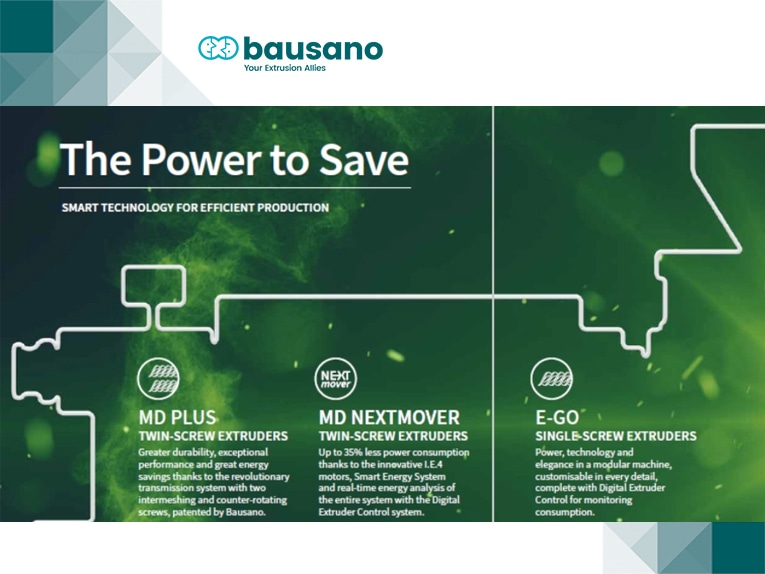
#Product Trends
Extru-dinary energy efficiency with plastic extruders
Energy costs are a major item on the balance sheets of plastics manufacturers.
In the current climate, the management of these expenses is vital to maintain competitiveness in the market. However, controlling energy costs should not compromise the functionality and efficiency of the production processes.
The extruder itself is the main energy-consuming component for a company producing plastic products. Designed by our team of technicians, the new series of MD NEXT-MOVER extruders offers a package of innovations, including plastic extruder energy efficiency, setting it apart in the field of plastic granule, profile and tube production technology.
The last five years at Bausano have been transformational, as the company has undergone a massive renewal. Fully aware that the plastics industry is at a crossroads, Bausano has evolved, investing in innovative, safer and more sustainable materials and technologies.
Bausano has the expertise to produce a fully customisable range of plastic extruders for a variety of sizes, applications and materials. Extruders from Bausano can be designed to manufacture anything from pipes to windows, to pellets and specialised devices like medical tubes. A broad range of plastic and food materials can be processed, including PVC, HDPE, pet food or even grain-based foods.
With our technology, we can design versatile machinery for the manufacture of mainly five product categories: granules, medical products (tube, bag and sheet), profiles and tubes. Last but not least is the processing of special materials, such as WPC, made from wood and plastic.
Alongside the impressive range of customisable plastic extruders, what sets Bausano apart from the competition is its underlying philosophy. The company sees itself as an ally to all its customers, always looking for ways to help.
Bausano’s new NEXT MOVER range focuses on plastic extruder energy consumption, which is managed by the DIGITAL EXTRUDER CONTROL system 4.0. This measures all the energy used, presenting the operator with elaborate graphs and tables that allow customers to verify their exact energy consumption during the production process.
According to data, the NEXT MOVER extruders deliver energy savings of around 30–35%. These efficiencies are achieved as a result of the Bausano induction barrel heating system (patent pending) and the patented Multidrive gearbox.