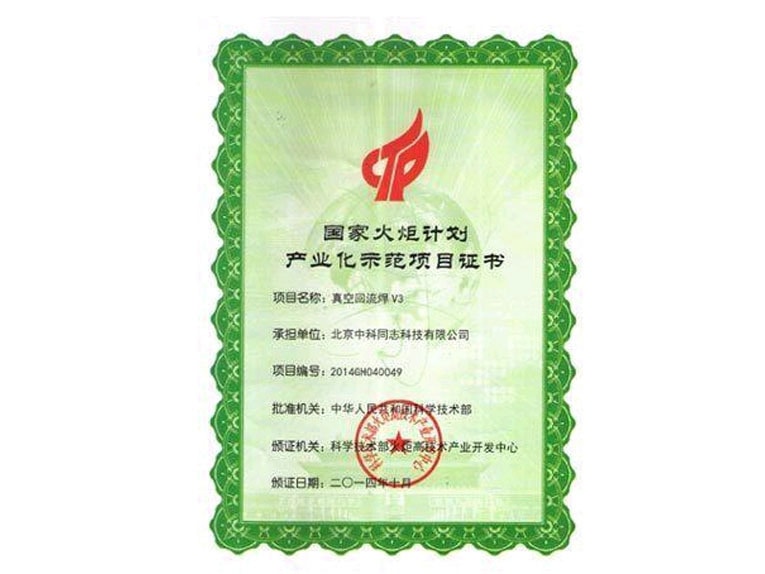
#Product Trends
What is vacuum soldering system? TORCH tell you!
Vacuum eutectic furnace/vacuum soldering system
Vacuum eutectic furnace (vacuum soldering system) is a process welding furnace for high-end products, such as laser devices, aerospace, electric vehicles and other industries. Compared with traditional chain furnaces, it has greater technical advantages. The main components of the vacuum eutectic furnace system include: vacuum system, reducing atmosphere system, heating / cooling system, gas flow control system, safety system, control system, etc.
Product Principle
Compared with the traditional reflow soldering system, the vacuum soldering system mainly uses a vacuum to help the voids be discharged above the liquidus in the solder paste / solder, thereby reducing the void ratio. Because of the existence of a vacuum system, the air atmosphere can be changed to a nitrogen atmosphere to reduce oxidation. At the same time, the presence of a vacuum also increases the possibility of a reducing atmosphere.
Vacuum removal of voids
In the atmospheric environment, the air bubbles / flux formed in the solder paste / solder in the liquid state are also under atmospheric pressure. When the outside world becomes a vacuum environment, the difference in air pressure between the two can increase the volume of bubbles in the liquid solder paste / solders, merge with adjacent bubbles, and finally reach the surface and discharge. Subsequently, the air pressure is restored, and the remaining bubbles remaining therein will become smaller and continue to remain in the system.
From the perspective of industrial production, the following points need to be pointed out:
Absolute high vacuum (10 -n mbar claimed by some manufacturers) can theoretically reduce the void ratio to a greater extent because the pressure difference is the driving force for bubble ejection. It then takes a very long time to pump high vacuum, which needs to be considered in actual production. In addition, the time above the liquidus also needs to be considered. And in fact, because the surface of the material in the production cavity is not completely flat, it will adsorb some gas and liquid phase substances, and it is theoretically possible to achieve absolute high vacuum.
Absolute 0% voiding cannot be achieved, and it is not guaranteed that every bubble will be completely removed in production. Generally speaking, the requirement of the so-called low void ratio is that the total void ratio is <3%, and the maximum void ratio is <1%.
Nitrogen atmosphere
The addition of a vacuum system allows the cavity to be filled with a nitrogen atmosphere after evacuation, which is also involved in traditional reflow soldering. However, the following points need to be pointed out:
The addition of nitrogen is to exhaust O2 in the air to prevent oxidation. In the open environment of the reflow furnace, it is not possible to completely exhaust O2. The industry believes that the need to reduce O2 to less than 100 ppm can guarantee the possibility of no oxidation. Therefore, a closed system is an appropriate system for applying the N2 environment.
In addition to the presence of O2, the oxidation of metals is extremely important for temperature. Therefore, when nitrogen protection is applied, the temperature of the device must be lowered to a certain temperature before the system can be opened to contact with O2. For example, for DCB welding, it should be ensured that the surface temperature of Cu rises to more than 50C and the surface temperature after welding decreases to 50C before oxidation can be completely avoided in the N2 environment.
Reducing atmosphere HCOOH formic acid and N2H2 syngas
In the use of solder paste, a reducing atmosphere is practically unnecessary due to the presence of a flux. The vacuum step can reduce the void ratio. However, considering the flux residue / cleaning cost, etc., some manufacturers will choose to use flux-free solder pads. In this case, the use of a reducing atmosphere is required. The reducing atmosphere can increase the wettability of the solder pads, thereby reducing the void ratio from another angle. For the common reducing atmosphere HCOOH formic acid and N2H2 synthesis gas, the following points need to be pointed out:
Both work by reacting with metal oxides to reduce them to pure metals for subsequent liquefaction.
The reaction temperature of HCOOH formic acid and metal oxide is lower than 200C, forming metal formate and water. Above 200C metal formate decomposes into metal and H2O CO2, so HCOOH formic acid is suitable for low melting point alloy system
The reduction reaction of H2 needs to be performed in a high temperature (250C) environment, so it is not suitable for low melting alloy systems.
others
The main principle of the vacuum eutectic furnace is to use vacuum to remove voids. Nitrogen atmosphere and reducing atmosphere are additional conditions. Customers should choose according to their product requirements and economic level.
The existing vacuum systems are mainly divided into
Traditional reflow soldering + vacuum module: The advantage is that in theory, it can be improved in the existing reflow soldering production line. The disadvantage is that other parts except the vacuum system module cannot completely prevent oxidation.
Single vacuum module with heating and cooling device: The advantage is that it can ensure the vacuum environment and nitrogen atmosphere. The disadvantage is that the heating and cooling are completed by the same heating and cooling plate, and the service life is short.
Multi-vacuum modules, a single module is only responsible for heating, welding, and cooling steps: the advantage is that it can ensure the vacuum environment and nitrogen atmosphere, different modules are responsible for different temperature zones, similar to the traditional reflow multi-chamber welding furnace, so as to maximize the output Efficiency and quality, the disadvantage is the higher price.
In-line vacuum eutectic furnace: This is to fully preheat in a nitrogen environment and then eutectic weld in a vacuum environment. The equipment adopts plate heating, with high heating efficiency, low nitrogen consumption, and oxygen content can be controlled to 10PPM. Ideal for welding of higher quality products.
There are not many domestic manufacturers of vacuum eutectic furnaces. At present, Beijing Zhongke Comrade has done a good job in science and technology, and there is not much gap with imported equipment. Many listed companies use their vacuum eutectic furnaces, and overall market feedback is good. He has also obtained the National Torch Plan Industrialization Demonstration Project.