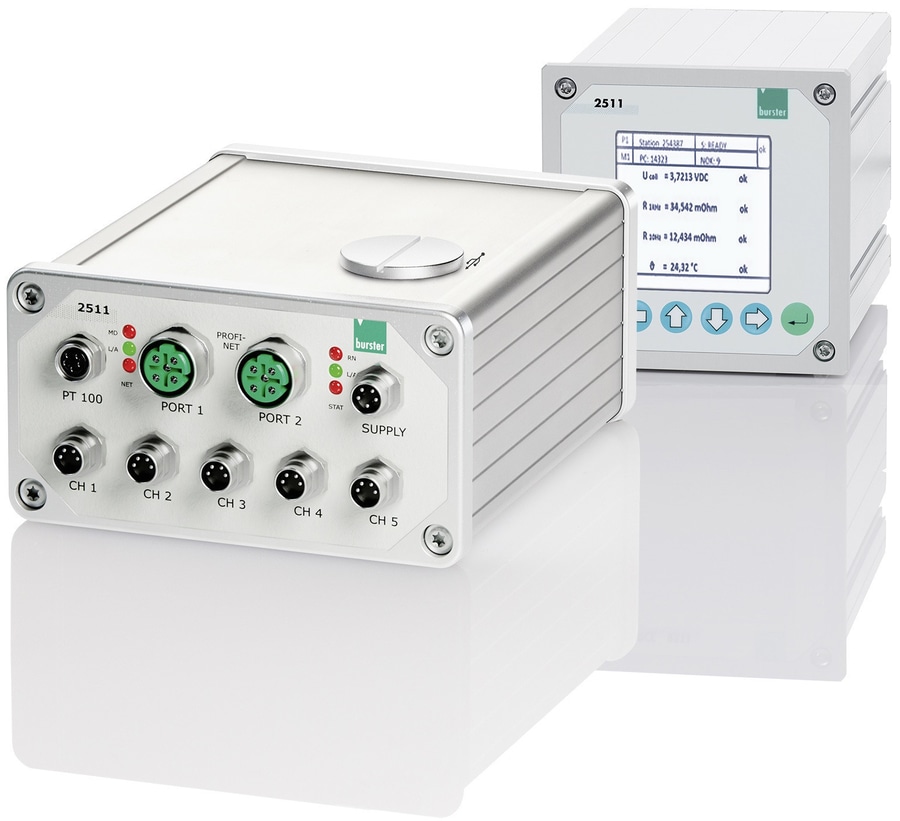
#Industry News
100% quality control in fractions of a second
Battery testing and measuring modules for automation, testing and laboratory use
Whether telecommunications, tools, leisure or electromobility – many modern devices and vehicles today operate independently of the mains with rechargeable batteries. For these to work reliably, the electrical properties of the individual battery cells must be as homogeneous as possible, and their mechanical connections must also be tested 100 %. As some larger batteries contain hundreds of individual cells, cell evaluation measurements have to be carried out quickly, reliably and safely during the production process. This requires modern Industry 4.0 capable measuring devices for all relevant parameters relating to the individual cells.
An electrical battery consists of individual battery cells grouped together to achieve a higher voltage or capacity. This means, however, that a battery is only as good as its weakest cell. Battery manufacturers therefore have to test the exact properties of all individual cells and preassembled individual modules for the ongoing production process, and classify them into quality groups. An electric car battery, for example, usually has several hundred cells installed in multiple modules. Testing such large quantities in the shortest possible time places special demands on the measurement technology. It takes many years of experience with electrical and mechanical measuring methods to combine the key properties for battery production in one family of measuring devices. These modern devices can then be used individually or in a group. They are Industry 4.0 compatible and easy to connect to standard fieldbuses, integrate into production systems, or use for research and development purposes.
Testing electrical properties of individual cells
The most important aspect of cell testing is to determine the individual electrical properties of single cells. If a cell with a lower capacity is connected in series, the entire group of cells is only able to deliver the lower amount of current. This can also lead to total failure, as the cell with the lower capacity is fully charged first, but the others continue being charged and the cell with the lowest capacity overheats. The deviating cell can overheat when discharging, too. Another issue is caused by different internal resistances, which result in uneven charging and heating of the cells. For this reason, the battery cells should have parameters that are as identical as possible (see figs. 1a, b). As battery packs are made up of individual cells with different formats (round, pouch, prismatic), the measurement technology must be able to test all variants.
With thousands of individual cells to test in many cases, a high throughput is essential. The use of measuring devices in the automated production testing of battery cells for consistent 100 % quality assurance in fractions of a section requires extensive expertise. The 2511 all-in-one module (see fig. 2) from measurement technology specialists burster (see company boxed text) is a measuring device specially developed for such tasks. Offering AC/DC internal resistance measurement with values from 0.1 µΩ … 300 mΩ in 4 measuring ranges from 10 … 300 mΩ, as well as a four-wire measurement method for maximum precision, it allows measurement and evaluation results to be generated in the shortest possible time. Measurements can be performed in the frequency range of 1 kHz, 100 Hz, 10 Hz, 1 Hz and at voltages of 0 ... ±5 V DC. In just a few milliseconds, the cascadable battery measuring module provides information on electrolyte and electrode quality compared to the manufacturer’s specifications, via single to multi-channel applications and temperature measurement. Its compact design and PROFINET and EtherCAT fieldbus interfaces enable simple integration into production. Matching PC software for intuitive parameterization/configuration facilitates the creation of individual measurement programs (see fig. 3).
Testing high-current connections
Inside a battery pack, the individual cells have to be connected together. This is done using rigid busbar connectors, wires or spring contacts that are pressed, screwed, soldered or crimped onto the cells. It is important that the specified contact resistances are adhered to very precisely, to minimize power loss and heating of the battery. With large production quantities, measuring devices also need to have very fast evaluation times. At up to 100 measurements per second, the model 2311 RESISTOMAT® from burster is tailored to the requirements of high-speed applications in automation (see figs. 4a, b). The four-wire measurement method eliminates test-lead resistances and contact resistances. Integrated open-circuit detection monitors the test leads. Despite a measuring range of 20 mΩ … 200 kΩ with a resolution of up to 1 μΩ and a measurement accuracy of ≤ 0.03 % of reading, the testing instrument achieves high-speed measurements from 10 ms per measurement including evaluation. A 2-way and 4-way comparator with switching outputs performs classifications and selections. All device settings can be configured individually in up to 32 different measurement programs, optionally also via Ethernet, USB (standard) or fieldbus interfaces (optional). The integrated data logger can store up to 900 measured values per measuring program.
Determine mechanical measured values
Mechanical parameters are also important in battery production. By measuring tightening torques and tightening forces, it is possible to ensure that contact surfaces are securely attached and contact resistance is minimized. When press-fitting high-current contacts onto PCBs or inserting individual cells into retaining tubes or boxes, it is likewise necessary to measure the forces that occur. Recording and validating the joining forces immediately reveals any joining defects. Force/displacement press-fit monitoring with window and envelope techniques allows e.g. recording of min/max peak values and mean force values within a specified tolerance range. Such test methods are easy to implement with the DIGIFORCE® 9307 X/Y process controller (see fig. 5). With a PROFINET, EtherCAT, EtherNet/IP and Ethernet UDP interface, the module supports flexible process control and measurement data acquisition. Up to 128 measurement programs allow a high degree of product variance. For example, where force/displacement is monitored for the insertion of individual cell plates / cell blocks into a cell housing, several units can always be joined simultaneously to optimize the cycle time, and each individual plate can be measured and evaluated with the aid of cascaded DIGIFORCE® controllers.
Long-term monitoring of the expansion behavior of battery cells
But it is not only time-critical measurements in the production line that are important. Measuring devices are also needed for laboratory measurements of cell and battery behavior – for example in development or for spot checks. These devices can also be used to easily obtain mechanical measured values for long-term monitoring e.g. of expansion during charging and discharging cycles, or to determine the forces that occur with temperature monitoring, or to optimize pressure distribution and service life. Thanks to its small size and three fixing holes, the burster 8526 compression load cell is suitable for tasks like these in various application areas (see fig. 6). Even angle errors in the load application with a deviation of up to 3° from the measurement axis have only a negligible influence on the measurement result. Its wide choice of measuring ranges from 0 … 100 N to 0 ... 1 MN allows precise measurement of forces or expansion with temperature – not only for battery cells – for example as cells are charged and discharged. This in turn permits an exact assessment of the long-term behavior and aging process.
Picture captions:
Figs. 1a, b: Battery cells should have parameters that are as identical as possible (source: burster).
Fig. 2: The 2511 all-in-one module is ideal for use in automated production testing of lithium-ion battery cells for consistent 100 % quality assurance in milliseconds (source: burster).
Fig. 3: Matching PC software for intuitive parameterization/configuration facilitates the creation of individual measurement programs (source: burster).
Figs. 4a, b: The model 2311 RESISTOMAT® is designed for the requirements of high-speed applications in automation (source: burster).
Fig. 5: When recording and validating the joining forces with the DIGIFORCE® 9307 X/Y process controller, any joining defects are detected immediately (source: burster).
Fig. 6: Mechanical measured values for long-term monitoring of expansion during charging and discharging cycles, or to determine the forces that occur (source: burster).
(All pictures see link)
Company box: About burster
burster supplies measuring technology ranging from individual sensors to system solutions. Its customers are mainly in mechanical and plant engineering, automation, the automotive industry and its suppliers, electrical and electronic engineering and the chemicals industry. The range includes measuring instruments and testers as well as standard sensors for mechanical and electrical measured values, such as load cells, pressure, torque and displacement sensors, milli- and megohmmeters, and resistance decade boxes. In addition, individual custom OEM solutions are possible, including for many other sectors and future markets such as medical engineering, biotechnology and e-mobility. Many years of experience in designing and building measuring instruments and sensors guarantee optimum solutions every time. Developed and manufactured in Germany, burster sensors, amplifiers and transmitter modules, precision instruments and measuring systems for sensor signal processing are shipped to customers all around the world.
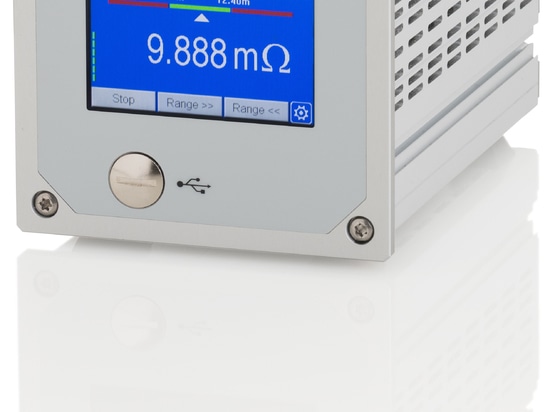
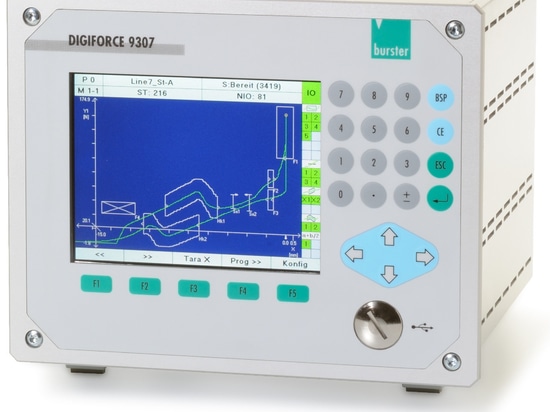