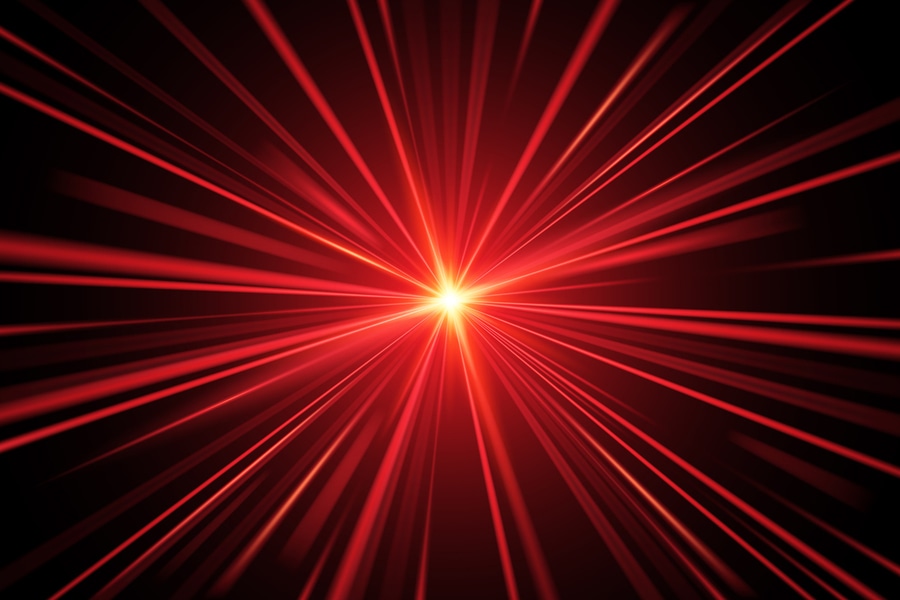
#Industry News
HISTORY | 60 Years of Laser: A Solution For So Many Problems (Part 1)
HISTORY | 60 Years of Laser (1/2) – The laser was invented 60 years ago in 1960. On the occasion of its 60th anniversary, journalists and industry experts tell the impact that laser technology had in Germany and evaluate its future.
On May 6th, 1964, the New York Times featured an interview with Theodor Maiman, the man who had built the first laser in Mai 1960. 60 years later we know how many problems his invention solved. Without lasers, we would have no internet, no computers and no gene sequencing, to name but a few major applications. But it took 60 years and many brilliant minds around the globe to get all these problems solved with lasers.
By Nikolaus Fecht (Dipl.-Ing. at Deutsche Presse-Agentur) and Dr. Andreas Thoss (Managing Director at THOSS Media GmbH)
It all began in May 1960, with a bright-red dot. In a Malibu laboratory, the physicist and electrical engineer Dr. Theodore H. Maiman was experimenting with a synthetic ruby, several centimeters in length. This rod-shaped crystal had a silver mirror at each end and was surrounded by a helical xenon flash lamp. The intense light from this lamp made the rod shining pink – in physical terms, it excited the atoms in the crystal. A light pulse bounced to and thro between the mirrors and left the pink ruby as a bright-red beam of light. It was the first-ever officially documented laser beam.
Death Rays?
In his memoirs, How the Laser Happened, Nobel laureate Charles Townes, another laser pioneer, relates how the military’s imagination was fired from the very beginning by the laser’s destructive potential. There was talk of death rays and of bringing down rockets in space. His brother-in-law and co-inventor, Arthur Schawlow, rather encouraged this idea by demonstrating in public how a laser could be used to shoot down party balloons.
Such ideas quickly led to a massive expansion in research and development – in both East and West. The USA thought the laser might be “the biggest breakthrough in the weapons area since the atomic bomb” and pumped millions of dollars into research from 1960 onwards. Back in Germany, budgets were much smaller; but here, too, the Federal Ministry of Defence soon enlisted the support of industry, in the shape of companies such as Leitz and Telefunken. It rapidly became clear, however, that the laser’s chief use lay in the areas of measurement and surveying. The development of “death rays” for shooting down rockets never advanced beyond the test phase.
Among the first to the table were, of course, established companies from the optics industry. In the early 1960s, both Carl Zeiss from Oberkochen in former West Germany and VEB Carl Zeiss from Jena in former East Germany launched development activities, partly at their own expense. By 1962, the first laser was up and running in Oberkochen, VEB Carl Zeiss presented a first lab model of a laser-based range finder in 1965.
Work on military projects was soon flanked by civil applications, not least in Germany. As early as the mid-1960s, the Architectural Academy of the former German Democratic Republic (Bauakademie der DDR) had introduced the use of construction lasers – some 20 in all – for the purpose of high-precision measurement and surveying in the construction of, for example, television towers.
Laser-Drilled Diamond Draw Plates
Zeiss in Oberkochen went on to develop q-switched solid-state lasers with a peak output power in the megawatt range. Although unsuitable for processing materials, they were more than adequate for measuring and surveying purposes.
By a quirk of fate, it was a precision engineer who paved the way for the first industrial application. Dr. Paul Seiler, then a young lab engineer, was given a free hand by Dr. Siegfried Panzer, head of the high-frequency lab, to work on laser technology. Seiler, now 82 years of age recalls:
“Following exploratory experiments with microscope optics, we then built a lab-spec device. We were in uncharted territory – it was not only the laser technology that was new but also the optics and the power supply with capacitor discharge.”
But the work paid off, as Zeiss was able to sell the lab device to, for example, light-bulb manufacturer Osram, who used it to drill diamond draw plates.
Laser Welding Replaces the Traditional Bonding Process
For Seiler, the decisive step came with another customer, CARL Haas from Schramberg in southwest Germany. The precision engineering specialist was looking for a welding process with which to attach the hairspring to the balance wheel in mechanical timepieces. Seiler developed a lab system that performed so well in welding trials that Haas offered him a job. That was in 1971.
Seiler felt he was plowing a lone furrow at Zeiss, so he moved to Haas in Schramberg, where he and a small team went on to develop a solid-state laser suitable for industrial purposes. This laser then replaced the traditional gluing process for attaching the hairsprings, which took ten times as long. The ultimate breakthrough for Seiler and his team followed at the end of the 1970s when laser technology paved the way for the automated production of welded parts for cathode-ray tubes in the recently developed color TV. Seiler was later appointed managing director of the then independent company Haas Laser GmbH, which became part of the TRUMPF Group in 1992.
Gas Lasers Versus Solid-state Lasers
At TRUMPF laser technology was the focus of a young manager – Berthold Leibinger. Initially a design engineer at TRUMPF and then, from 1966, technical managing director – he flew to the USA in 1978 and visited a number of laser manufacturers. Nothing of what he saw was suitable for industrial purposes, but he did purchase his first CO2 laser. At the end of a year’s intensive development work, he unveiled his first industrial laser cutting machine.
Engineers were intrigued by the differences between gas and solid-state lasers, explains Christian Schmitz, chief executive officer for laser technology at TRUMPF:
“The CO2 laser was actually the first-ever laser capable of delivering a high output power in continuous-wave operation whereas the solid-state laser had a high output power in pulse operation, which made it ideal for applying spot welds in electronic components.”
But for the next 20 years, the cutting and welding of sheet metal parts would remain the preserve of the CO2 laser. It was only at the turn of the new century, with the development of increasingly efficient diode lasers, that solid-state technology had its breakthrough.
Tailored Light With a Wide Range of Wavelengths
The 1980s brought a new generation of scientists and a rash of new research institutes. One of these upcoming researchers was Reinhart Poprawe. Inspired by a tour of the Lawrence Livermore National Laboratory in California, he went on to study – and complete a doctorate – under Professor Gerd Herziger at the Technical University of Darmstadt. In 1985, he and Herziger then established the Fraunhofer Institute for Laser Technology ILT in Aachen. At the time, Poprawe was managing director of Thyssen Laser Technik GmbH, which was then making a name for itself with the development of the first-ever industrial-scale laser cutting machines for thick sheet metal and the next generation of tailored blanks for the automotive industry. After a couple more years, however, he moved on to become director of Fraunhofer ILT.
At Fraunhofer ILT, Poprawe was able to witness how laser technology, in every new variations, progressively established a foothold in the manufacturing industry. Looking back, he picks out some highlights: the development of the ultrashort pulse laser, of the InnoSlab laser and, last but not least, of the concept of “tailored light” – laser technology that delivers light perfectly customized to individual applications.
Additive Manufacturing: The Long Road to Industrial Application
After the euphoria of the early years, laser technology then had to prove that it could beat conventional processes on quality and cost. The advent of additive manufacturing for metal parts offers a good example of how rival technologies battled for supremacy. According to Schmitz, TRUMPF “had a share in inventing” this technology. It was in 2004/05 that TRUMPF launched its first laser metal deposition (LMD) machines. Schmitz recalls:
“Around the same time, however, the first really fast five-axis milling machines came on the market. And with additive manufacturing, the parts always needed a little bit of finishing. So people thought it was better to mill them from a single piece of material.”
While the development of LMD continued, TRUMPF suspended its work on laser metal fusion (LMF). Production of the Trumaform – TRUMPF’s first LMF machine – was halted and only restarted again in 2013/14, in cooperation with the Italian company Sisma.
Then a new idea was developed in Aachen that would prove a game-changer: extreme high-speed laser material deposition – a process also known under the German acronym EHLA. It was developed and patented at the Fraunhofer ILT in cooperation with the Chair for Digital Additive Production (DAP) at RWTH Aachen University. This increased deposition speeds from 2 meters, at most, to several hundred meters per minute. Following close cooperation with the Netherlands engineering company Hornet Laser Cladding and with ACunity, a Fraunhofer ILT spin-off, EHLA technology was then rolled out for industrial production worldwide. Laser pioneer TRUMPF was also impressed with the fast coating speeds enabled by the EHLA technology and in 2017 launched production of its highly successful TruLaser Cell range of EHLA machines for processing components of varying sizes. Currently, the idea is rolled out to real 3D processes.
After 20 years of ups and downs, laser-based additive manufacturing processes have finally achieved the market breakthrough.
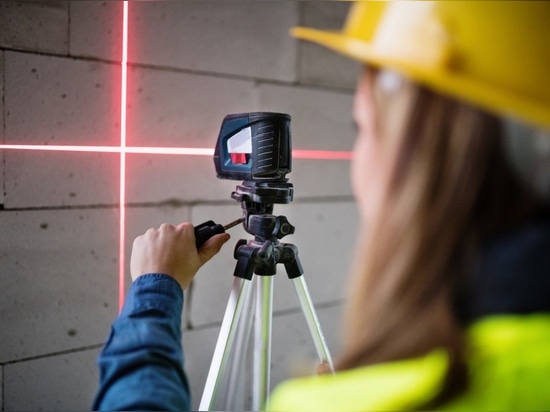
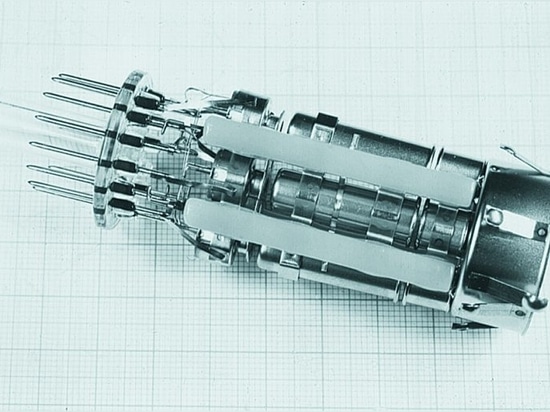
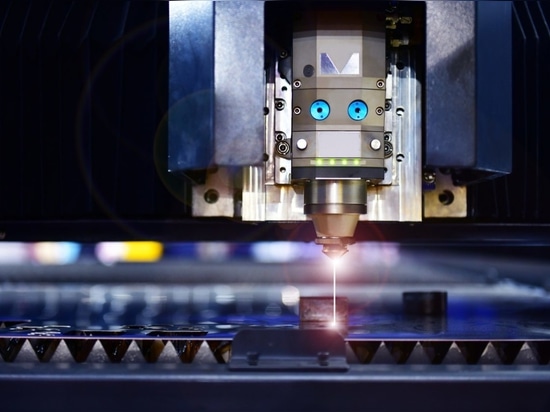
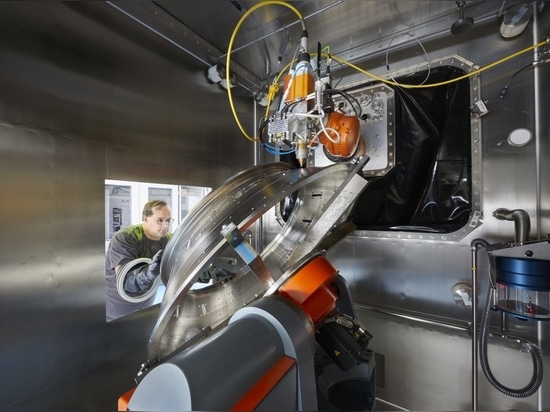
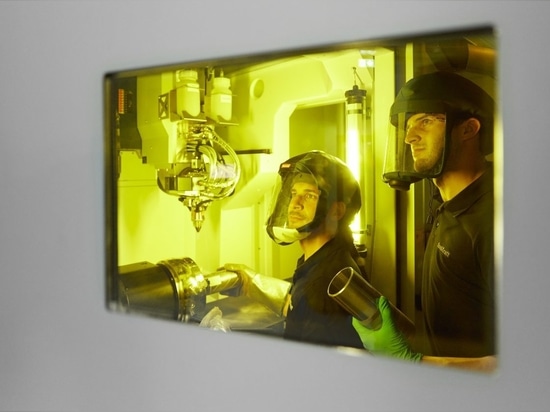