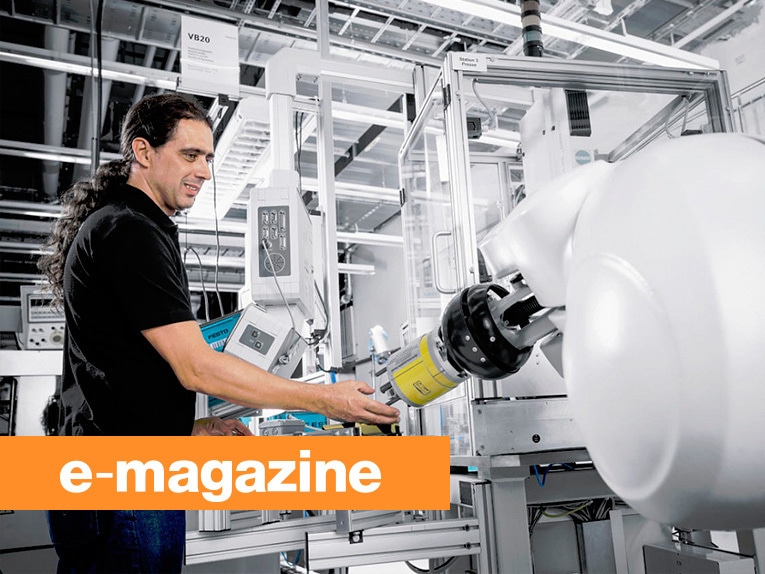
#Industry News
Festo in Germany: Industry 4.0 in Action
The factory of the future is fast becoming a reality. This is nowhere more obvious than in Germany. The rise of automated plants is bringing Industry 4.0 to the forefront of production, with companies like Festo leading the way in automation.
An Intuitive HMI Technology Plant
In Scharnhausen, southeast of Stuttgart, pneumatic and electronic automation company Festo has invested €70M in expanding and renovating their oldest factory, creating a new plant on the cutting edge of automation technology.
Festo spokeswoman, Annette Ostertag:
It is now our leading plant for valves, valve terminals and electronics. Our philosophy was to create a plant of intuitive human-machine interfaces (HMIs), training and qualification, as well as innovative technologies.
For example, all service engineers use tablet computers as HMI systems, with a special app that helps them rectify technical faults quickly and process orders on-site.
Looking Green
Completed last autumn, the plant produces valve technology for the food and beverage, automotive, electronics, solar and end-of-line packaging industries. It takes advantage of the very latest energy-efficient processes and green production techniques.
We have two production lines for solenoid valves. Over one million valves are assembled each year and assembly and testing is completed in a few seconds. In order to keep energy consumption to a minimum, we took innovative paths when planning the factory and building.
This includes two natural gas-powered cogeneration stations that produce both electricity and heat for the plant’s 66,000 m2, ensuring basic supplies and reducing demand for mains energy.
But it doesn’t stop there.
As processes are often mutually dependent, the energy has to be distributed sensibly. By continually adjusting the generation process to the actual consumption situation, the necessary energy can be provided very efficiently.
The plant is also implementing three pilot projects, aimed at further reducing energy consumption and increasing efficiency:
EnEffAH focuses on energy efficiency in drive and handling technology. Festo reorganized its compressed air system for enhanced efficiency.
The EMC2 Factory is designed to improve a factory’s energy performance. Festo introduced building and machinery measurements for ever greater energy savings.
Metamorphosis Industry 4.0 helps convert existing operations into intelligent and networked factories. Festo set up a networked energy management system and an energy control station to continually adjust their generation process to match consumption needs.
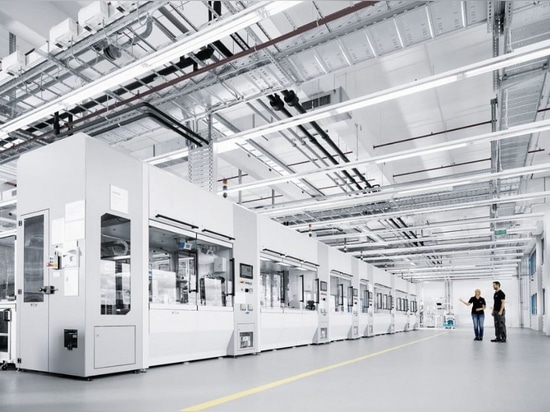