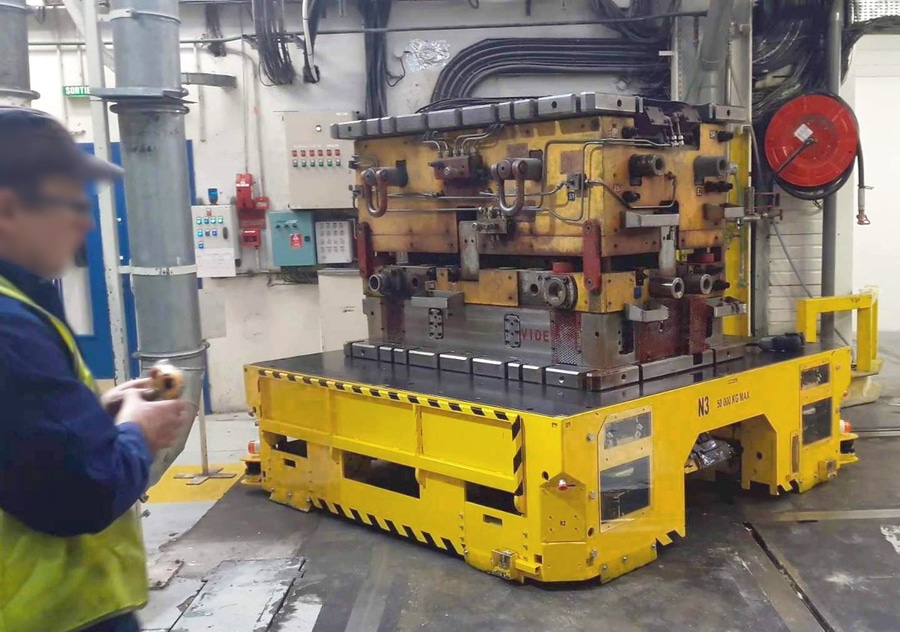
#Industry News
Autonomous trolleys
Flow automation: A leap forward in efficiency and innovation.
The automation of inbound and outbound logistics flows is an exciting challenge for companies seeking to achieve maximum efficiency in their operations. For Dynalserg, the automation process starts with a clear objective: to improve efficiency, increase production and reduce costs. In this context, discover a leading company in the plastic injection moulding industry, which takes a big step towards efficiency and quality by automating its production and logistics flows, redefining mould management and setting a new standard in optimising internal operations.
In a highly competitive world of industry, the pursuit of efficiency and process improvement is essential. When an industry decides to improve its internal logistics operations, it takes a big step in creating a flow automation project that redefines the way it manages products between halls. Such projects not only address complex internal logistics challenges, but also incorporate advanced technologies to ensure efficiency and safety.
Dynalserg is a company with a team with more than 40 years of experience in lifting and handling, whose top priority is safety.
Over the last 10 years we have developed a complete range of self-propelled vehicles and trolleys for heavy loads (up to 100 tonnes).
We pride ourselves on not selling standard products, but designing and supplying complete and customised solutions for our customers' "heavy load transport" needs.
Our quality, tailor-made products can be adapted to a very wide range of industries: food processing, steel industry, plastic injection moulding, manufacture/use of various panels (wood, gypsum, sheet metal, aluminium, etc.), manufacture/use of various coils (steel, aluminium, paper, plastic, etc.).
All our machines are manufactured in our workshops and are tested by an approved body before shipment.
THE CHALLENGE
The main objective of these ambitious projects is to automate production and logistics flows, significantly improving operational efficiency and product quality. Previously, all this transport was carried out by two trucks in three shifts and a forklift truck.
POSITIVE RESULT
The production flow and logistics automation project is a prime example of how innovation and vision can transform efficiency and safety in industry.
Our client has demonstrated that, through intelligent automation and the incorporation of advanced technologies, it is possible to overcome complex logistical challenges and increase productivity without compromising safety. "The automation of this flow with the implementation of AGVs has replaced the use of 2 trucks, 1 driver per shift (3 per day) and 1 forklift, making it economically more interesting. Despite the technology present in this new system, its use is very simple and logical for all those involved in the system. Another important aspect has been the ease of amortisation, as the entire investment can be amortised in a very short time," says Albert Bru.
This case demonstrates that intelligent automation can not only improve efficiency, but also boost sustainability in manufacturing processes.
General features:
High autonomy traction batteries.
* Steel rollers and tracks for loads from 50 to 100 T (with 4 steerable drive wheels).
* Wheels with polyurethane tyres, for use on workshop floors, for loads from 15 to 50 T (with 2 steerable drive wheels).
* Integrated intelligent battery charger.
* Intuitive radio control.
* Safety with 2 radars.
* Optional load lift.
Wide range
* Loads and dimensions on request.
* Automatic parking brake.
* Flashing lights when the vehicle is in motion.
* Peripheral safety foot protectors.
* Attractive price/performance ratio.

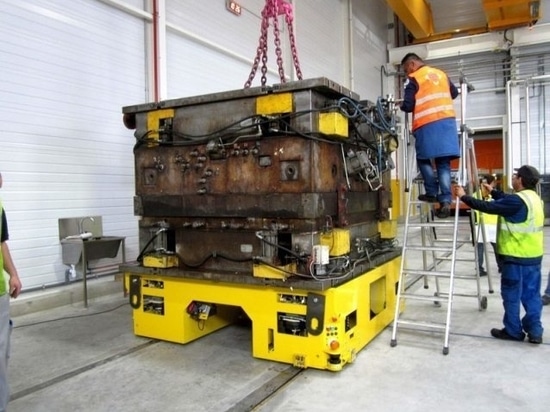