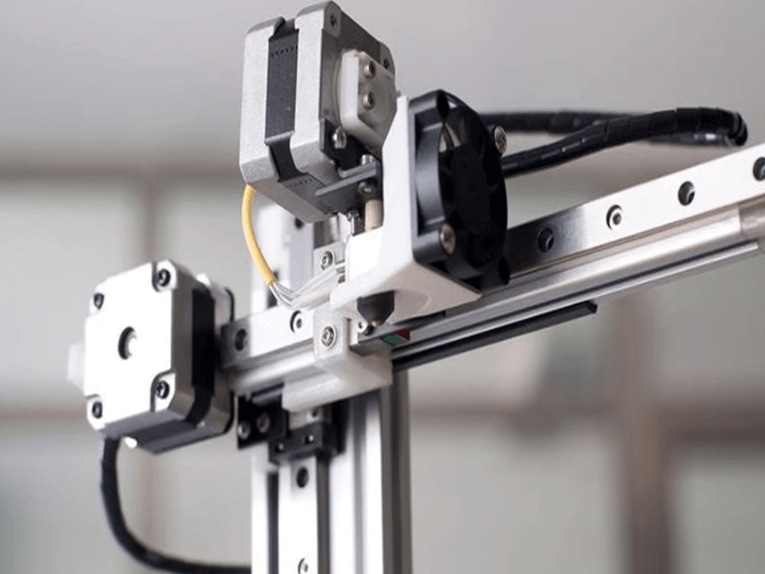
#White Papers
5 Points You Should Consider When Replace Linear Motion Systems
Shorter production downtime and Reduced lifecycle costs.
We outline the top five points that engineers, maintenance technicians and service providers should consider when replacing linear profile rail systems.
When a linear system has reached the end of its useful life, often the easiest thing to do is to replace it with a like-for-like linear system from the original equipment supplier (OE-fitted brand).
However, this may not necessarily be the best choice for your machine or your business.
Replacing a linear system with a product from an alternative linear supplier could be more beneficial, both in the short term and over the complete lifecycle of your machine.
Shorter production downtime
Whether the linear system is part of a special purpose machine tool, automated handling system, pick-and-place machine or part of a production line refurbishment, in the short term, choosing an alternative linear supplier’s product could result in a faster delivery time, allowing your machine(s) to be up and running again sooner, thus minimising production downtime to your business.
Reduced lifecycle costs
If the replacement linear system is higher/premium quality, over the long term, it is likely that your machine’s lifecycle costs or Total Cost of Ownership (TCO) will be reduced.
While the initial purchase price of the linear system may be higher, over the complete lifecycle of the machine, the potential savings that can be achieved in the form of improved energy efficiency (eg, by using lower friction components) and reduced maintenance costs (by using better sealing, special protective materials or corrosion-resistant coatings) often more than outweigh the initial higher purchase price of the premium linear product.
Key factors to consider
In this article, ‘linear systems’ and 'linear profile rail systems' refer to a complete rail(s) and carriage(s) assembly.
Replacement linear systems from alternative manufacturers must be replaced as a complete carriage(s) and rail(s) system.
This is necessary as replacements will be based on matching external boundary dimensions with acceptance of differing internal geometry.
When a supplier receives a linear system enquiry for replacing existing used product, certain factors need careful consideration before a suitable product for a single-, two- or three-axis positioning system can be selected.
Although not all the technical data will be available to hand, certain key features of the linear system need to be established if performance of the new system is to be maintained, while enabling sourcing from alternative original manufacturers:
1. Size and length of the rail(s) and carriage(s), ball or roller type
It is important to provide the linear supplier with accurate information on the size and length of the rail(s) and carriage(s), as well as the type of carriage (ball or roller). Do not simply rely on the markings. It may be that the size marking is visible on the carriage(s) but even if it is, overall system height, carriage length and the rail length should be measured for the system and provided to the supplier. If the rails are butt jointed, joint position(s) should also be indicated. Eg,Ball type carriage size 35, overall length 110mm, overall system height 48mm. Rail length 760mm, one-piece rail.
2. Rail end dimensions, symmetrical or non-symmetrical
Rail end dimensions should be provided. These include whether the dimensions are symmetrical or non-symmetrical, as well as the centerline of the first and last hole to the end of the rail (for both ends). Eg, symmetrical, both ends, 20mm.
3. Number of carriages per rail and design style
The number of carriages per rail and the design style are also important.
Typically, the design style of the carriage(s) is either rectangular or flanged but other more obscure styles do exist. Eg, two carriages per rail, flanged design style.
4. Number of rail sets, in parallel, in the machine
The number of rail sets, in parallel, in the machine needs to be provided. Eg, 2 parallel rails per set.
5. Type of machine being maintained
The type of machine is important to the support staff in selecting your precise product, as much information can be included from knowing the base application.
Providing a photograph of the application to the linear supplier can also prove very useful.
For example, a simple pick-and-place machine will operate satisfactorily on standard precision-grade product with a 'normal' or 'clearance-free' option.
However, in a machine tool, providing a linear system with a light or medium preload will be critical, together with a higher precision grade product. Eg, vertical machining centre.
In addition, depending on the machine type and operating environment, various options are sometimes specified for the linear system such as coatings or special lubricant, seal kits or lubrication accessories for specific conditions (eg, food-grade grease or coating, wipers, double seals, or a permanent lubrication feed).
Application experience is vital
From this base data provided in the five points above, a reliable selection of a replacement linear system can be made by a reputable supplier with qualified, trained support staff who also have application experience.
This enables a replacement linear system to be supplied that will help restore your machine to production performance, even when the original loading, speed, acceleration, stiffness and precision grade details are not available.
Ensuring that you receive the right replacement linear system to enhance the life of your machine means you must direct your enquiry to manufacturers of linear systems (or their distribution partners) who possess the necessary in-house expertise to discuss and specify your requirements in the necessary depth to allow you to get your production going again and help you reduce your Total Cost of Ownership.