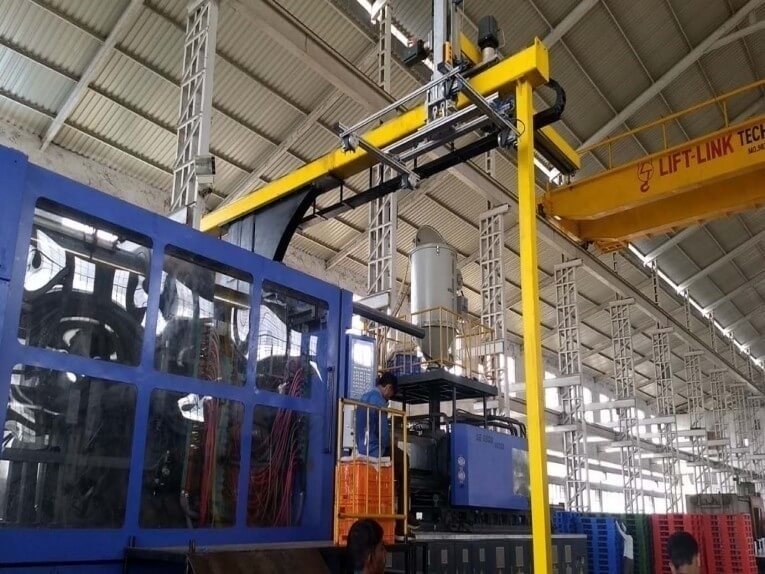
#Product Trends
What Are The Different Types of Pick and Place Robots?
Robotic Arm, Cartesian, Delta, Fast Pick, Collaborative.
Pick and place robots are available for a wide range of applications. Whilst this gives you an overview of pick and place robots, the exact type of pick and place robot to suit your application will be very dependent on your specific requirements.
Robotic pick and place systems can be configured for multiple different types of products and plant layouts. As a robotic handling system, it can run without any operator input, to pick and place parts from one process into another, or from a process into packaging or any other application where items need to be moved from one place to another. A robotic pick and place system will reduce repetitive strain injury and worker fatigue, whilst increasing production throughput, productivity and efficiency.
Robotic Arm
Probably the most common type of pick and place robot is the robotic arm type; which typically come as 5 axis robots for standard pick and place application in plane, or 6 axis robots for more complex applications where the products needs twisting from the horizontal (similar to the image above).
Cartesian
The cartesian robot is also a very common type of pick and place robot, that used to be cheaper, but is now not so commonly installed apart from for injection moulding machines.
Delta
Delta robots are mounted above conveyors and are typically used for high speed pick and place applications.
Fast Pick
Fast pick robots are also another option for fast pick and place applications; with cycle times as fast as 150 cycles per minute.
Collaborative
In recent years a wide range of different types of collaborative robots have hit the market and these are becoming increasingly used in industrial applications, but they are mostly smaller, slower robots with less of the complex functionality available. This limits their usefulness for some applications.
Installing and commissioning robotic systems requires a wide range of skilled automation engineers; from robot programmers and PLC programmers through to mechanical engineers and CAD design engineers.
A robotic pick and place systems would usually include the following:
1. A robot.
2. Touch screen control system – giving you set up options and a lot of surplus capacity for adding extra functionality such as, conveyors, link up with other machinery and remote production logging and monitoring.
3. Guarding and doors with interlocks and safety as required.
4. Bespoke robot gripper (the price may vary depending on how complex your items are to pick up and handle).
5. A basic conveyor.
With a bespoke designed pick and place system you will also be able to have the design modified suit your requirements. Modification can include; layout, guarding, how many products the robot picks up at once, stacking configuration and much more.
Small Robotic Pick and Place System
Small robotic pick and place systems are usually used where the product is small, and the distance that the product needs to be moved is short. Some example applications where a small pick and place system would be appropriate include; packing chocolates into boxes, transferring small items from a conveyor to a tray or conveyor, placing components into a circuit board, and orientation of small parts.
Medium Robotic Pick and Place System
Medium pick and place robots are usually used where the product is larger and needs to be moved over a longer distance, or where there are multiple smaller pick and place applications that come together. Some example applications of a medium pick and place system include; moving products between machines, movement of products within a food production process, and assembly of components.
Large Robotic Pick and Place System
Large robotic pick and place systems are usually used where the product is very large, or very heavy for example products weighing 100Kg or even up to as much as 1,000Kg +. Some example applications for a large pick and place system include; moving cars on a production line, moving large sheets of glass and raw materials on production lines etc.
Conclusion
Whilst this post gives you a broad overview of the different types of robotic pick and place systems, it is always important to have your own requirements professionally assessed to ensure you receive the optimum solution to meet your needs. Along with many other benefits, a truly bespoke pick and place system will enable you to increase efficiency, reduce product defects, improve productivity, reduce wasted space, reduce the risk of repetitive strain injury, run your plant 24/7, and improve profits.