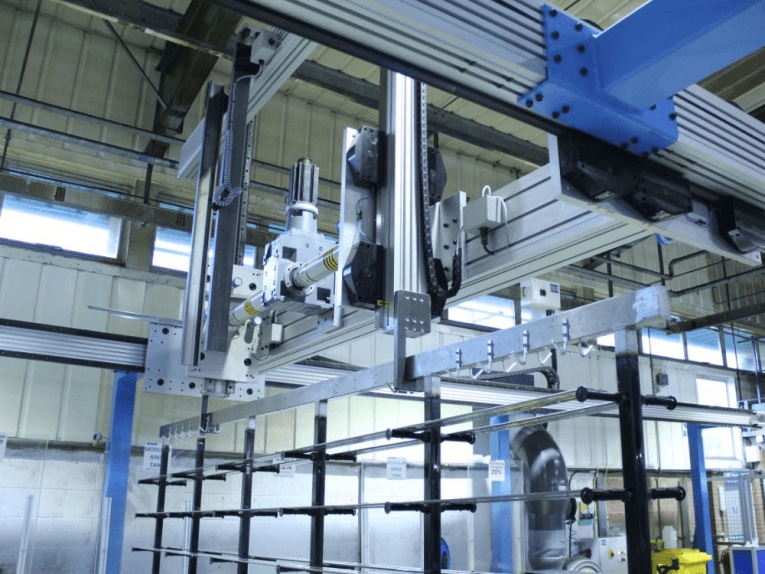
#Product Trends
What are Robot Gantries?
Components of XYZ Positioning System.
Robot gantries are powerful tools in modern manufacturing and automation, offering increased precision, flexibility, and efficiency in a range of applications.
Introduction
A robot gantry is an industrial robot with a robotic arm mounted on an overhead rail system or frame. The gantry structure comprises a series of beams or struts that provide the robot with stability and precision to move along the X, Y, and Z axes. Robot gantries are commonly used in applications where heavy payloads must be lifted and moved over large working areas. The robots can be configured to operate in various environments, including clean rooms, hazardous environments, and other specialized applications.
Components of Robot Gantry
Gantry robot systems consist of several components that work together to achieve precise and accurate movements. Here are the primary components of a robot gantry:
Gantry Structure
The gantry structure is the framework that supports the robot arm and the end effector module. It consists of two or more parallel beams that move along the X and Y axes and a vertical column that moves along the Z-axis. The structure must be rigid and stable to ensure accuracy and repeatability in the robot’s movements.
The gantry structure can be made of different materials, including aluminum, steel, and carbon fiber, depending on the application requirements. The material used must be strong enough to support the weight of the robot arm and the end effector while also being lightweight to reduce the overall weight of the gantry.
Robot Arm
The robot arm is part of the gantry that holds the end effector and moves along the X, Y, and Z axes. The robot arm’s design and specifications depend on the application requirements, such as the reach, payload capacity, and speed.
The robot arm can be equipped with different types of end effectors, such as grippers, suction cups, and welding guns, to perform specific tasks.
End Effector
The end effector is the tool or device that is attached to the robot arm to perform a specific task. The end effector can be a gripper, a suction cup, a welding gun, a cutting tool, or any other device that can manipulate the part or material being processed.
The end effector must be designed to match the application requirements, such as the shape and size of the part, the weight, and the material being processed. The end effector’s design can also impact the overall accuracy and repeatability of the robot’s movements.
Drive System
The drive system consists of motors and actuators that control the movement of the gantry structure and the robot arm. Depending on the application requirements, the drive system can be either hydraulic, pneumatic, or electric.
The drive system’s specifications depend on the application requirements, such as speed, torque, and precision. The drive system must also be designed to work with the control system to achieve accurate and precise movements.
Control System
The control system is the brain of the robot gantry, responsible for controlling the movement of the gantry structure and the robot arm.
The control system’s software must be programmed to match the application requirements, such as the motion profile, the acceleration and deceleration rates, and the path planning. The control system must also integrate with other sensors and equipment to achieve accurate and precise movements.
Overall, the design and specifications of each component of a robot gantry must be carefully considered to achieve accurate and precise movements, ensuring the gantry’s reliability and efficiency in performing its intended task.