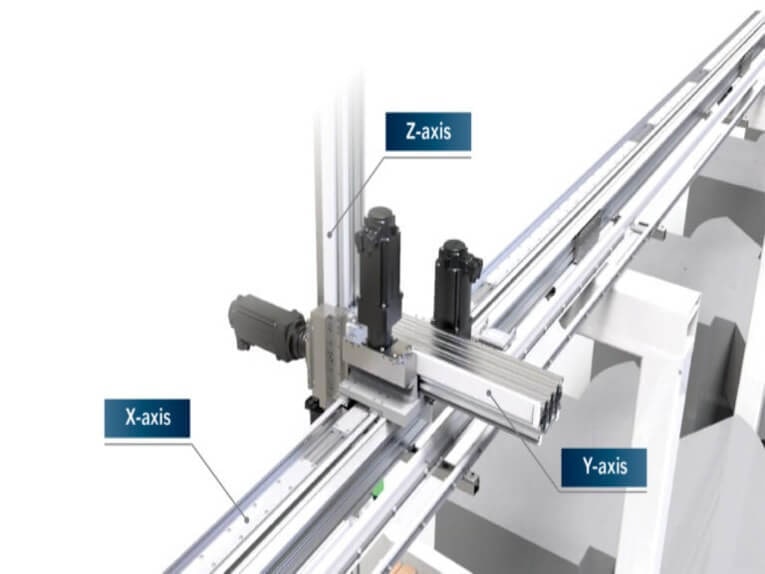
#Product Trends
Simplifying overhead machine tending with long-travel automation
Cartesian robots are a suitable choice for depalletizing applications.
Manufacturing and packaging operations using manual material or parts handling operations can reap immediate benefits from automation with long-travel Cartesian robots having custom end-of-arm tooling (EoAT) and advanced sensing capabilities. These robots can support a variety of machines to perform otherwise manual tasks such as machine tending or transferring in-process parts.
Cartesian robots consist of two or more coordinated linear positioning stages … so may not be the first thing that comes to mind if a design engineer is new to automation. Many equate robots with the six-axis articulated-arm robotics that industry increasingly applies on factory floors. Even experienced automation engineers may give Cartesian robots short shrift … focusing attention on six-axis models. Yet ignoring the benefits of a long-travel Cartesian system can be a costly mistake — especially in applications requiring the robot to:
1. Tend multiple machines
2. Reach long lengths
3. Perform simple and repetitive operations.
The problem with six-axis robots
For good reason, articulated arm robots are prominent in myriad automated manufacturing and packaging facilities … especially in electronics assembly and the medical industry. When properly sized such robotic arms can handle large payloads with the flexibility to perform many different automated tasks commanded by programming (and complemented by end-of-arm tooling changes). But six-axis robots can be expensive and require high robot density. The latter is a term that indicates a facility will likely need a separate robot for every one or two packaging machines. Of course, there exist larger and more expensive six-axis robots with reaches to serve more than a couple machines, but even these are suboptimal solutions because they force plant engineers to position machines around one very large robot. Articulated arm robots also necessitate safety guarding; consume valuable floor space; and programming and maintenance by skilled employees.
The case for long-travel Cartesian linear systems
Cartesian robots outperform six-axis robotic options in large part because they reduce the required robot density. After all, one long-travel Cartesian transfer robot can tend multiple machines sans the need for rearranging machines around the robot.
Transfer robots installed above the machines they tend consume no floor space … which in turn reduces safety-guarding requirements as well. Plus Cartesian robots require little programming and maintenance after initial setup.
One caveat is that the capabilities of Cartesian robotics systems widely vary. In fact, if engineers research Cartesian robots online, they’ll find many smaller systems optimized for pick-and-place operations on production or assembly machinery. These are essentially linear stages built into off-the-shelf Cartesian solutions — very different than the transfer robots useful in larger operations and needing to satisfy the following parameters.
Long travels: Any robot purchased to tend multiple large machines must have strokes to 50 feet or more.
Multiple carriage and custom end-of-arm tooling: Long transfer robots are maximally effective when fitted with multiple independently acting carriages to travel the main axis … allowing a given Cartesian robot the ability to do the work of many. Magnifying this productivity is purpose-built tooling to handle goods more effectively than off-the-shelf EoAT such as vacuum or finger grippers. In many cases, custom EoAT can also simplify the designs of material handling systems working in conjunction with the Cartesian robot.
Simplified control architecture: Some newer Cartesian robots eschew traditional control architectures based on separate motors, drives, and controllers for integrated servomotors (complete with servodrives) to nix the need for a control cabinet. The most complex Cartesian-robot applications may still demand a traditional architecture … but integrated servomotors deftly handle the point-to-point motion control requirements of most Cartesian robots. When a design engineer can use integrated servomotors, the latter can help maximize the cost advantage of a Cartesian-based automation.
Selective use: Because Cartesian robots mount above or behind the machines they tend, they also allow users to run the machines manually when needed — for example, for a short run of a special size. This selective use is difficult with floor-mounted six-axis robots that can block access to machines.
Specific Cartesian-robot example
Some Cartesian robots offer strokes exceeding 50 ft even while delivering speeds to 4 m/sec. Standard carriages might include a dual-belt drive technology; some other carriages contain an upper drive belt that continuously loops within. The latter prevents belt sag in inverted or cantilevered arrangements and allows multiple independent carriages to concurrently operate on an axis.
Long belts complicate Cartesian robot design, as they degrade driveline stiffness (which in turn degrades performance). That’s because maintaining a given tension value on long belts is challenging … and (making matters worse) belt tension is asymmetrical and variable. The issue renders long recirculating belts an underperforming, finicky, and costly choice for accurate positioning.
In contrast, moving-motor linear stages keep belt lengths short and tight and housed within the carriage so that they can respond to encoder-informed controls. Accuracy is maintained regardless of Cartesian transfer-system length … whether 4 m or 40 m.
Application example in the packaging industry
Long-travel Cartesian robot transfer units work in feeding, cartoning, and tray-forming applications and can handle palletizing and depalletizing operations.
Consider produce packaging. In a recent application for an agricultural packaging company in California’s Central Valley, one manufacturer supplied long-travel transfer robots to seamlessly integrate with the existing IPAK tray-former system. Each robot tends up to four machines at a time, filling them with stacked sheets of corrugated cardboard. The three-axis gantry robots are based on heavy-duty belt-driven linear servomotor stages for limitless travel lengths, independently moving carriages, and the ability to mount the stage in any orientation. The longest axis on one such robot runs over the bank of tray formers with a stroke exceeding 50 feet.
To deliver sheets of corrugated cardboard into the four tray-forming machines, a robot first picks a load of cardboard from a custom-built dock holds corrugated cardboard-sheet pallets. The robot then delivers a cardboard load to each tray former. Thanks its speed (to 4 m/sec) the robot can easily pace four tray formers — even at an output to 35 trays per minute.
Safety guarding uses overhead sliding gates and sensors that rise from tended machines to fence the robot as needed for a solution that’s less costly than that for floor-mounted six-axis robots.
Also included in this system are all the controls and custom EoAT capable of working with stacks of corrugated sheets that vary unpredictably in height and weight. The tooling can handle payloads to 50 kg sans issue. The solution relieves operators who once had to lift cardboard bundles from pallets and lean over to put them into the forming machines. Automating these tasks has freed personnel to focus on less grueling work.Large transfer robots are just one example of what’s possible with Cartesian robot systems in packaging settings. Some suppliers have also developed palletizing and depalletizing systems based on similar Cartesian approaches. All such robots employ three linear stages fitted with sensors, controls, and end-of-arm tooling for maximally effective and efficient packaging automation.