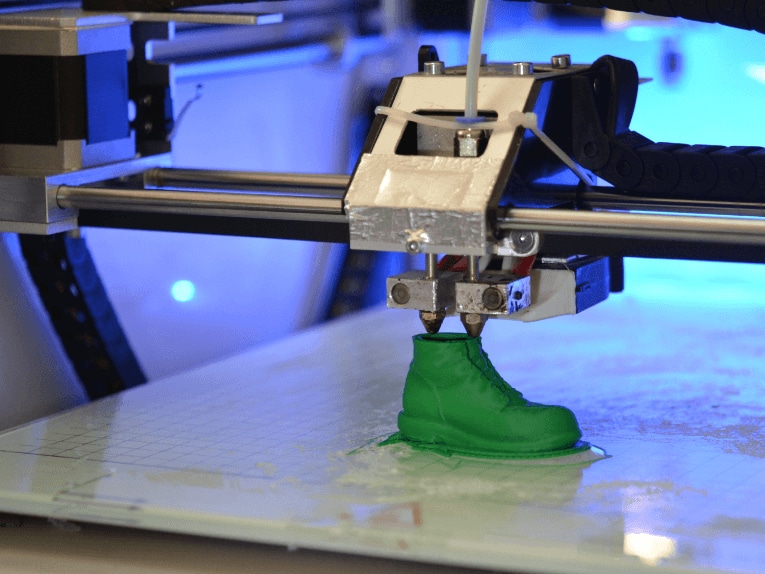
#Industry News
What Are the Different Types of Gantry Systems for 3D Printing?
Advantages and Disadvantages for your solutions.
1. Cartesian-XY-Head
A Cartesian-XY-head gantry system is a type of motion control system commonly used in 3D printers (and a wide variety of other classes of CNC machines). This construction approach moves the printhead or extruder along the X-axis of the gantry and moves the Y-axis by moving the entire gantry. This can involve moving a high mass on the Y-axis and may result in a greater risk of machine vibrations, especially during high acceleration maneuvers.
In such a gantry system, the print bed is fixed and the printhead or extruder moves along two perpendicular axes, typically running on ground shafts with recirculating ball linear bearings. Higher-priced versions often use V rails with externally V-grooved roller bearings as guides, resulting in reduced bearing wear. The X axis is usually defined as across the machine, while the Y axis is oriented backward/forwards relative to the device. The Z axis positions the vertical height of the printhead or extruder and is carried on the X motion of the gantry.
Cartesian-XY gantry systems are simple and easy to construct and operate. They also provide good precision and repeatability, allowing high-precision positioning of the printhead. However, they have limitations in terms of speed and acceleration and may lack stiffness in some respects.
2. Ultimaker-Style Crossed
The Ultimaker-style crossed gantry system is a mechanical structure and axis motion system less commonly used in 3D printing. It features two parallel gantries that position the printhead or extruder along the X and Y axes. The gantries are connected by a crossbar, which is intended to stabilize movement along both axes by sharing stiffness. The Z-axis motion is usually carried on these two axes, rather than delegated to a rising and falling print bed.
In this system, the print bed is typically fixed and stable. The printhead or extruder moves along both the X and Y axes. They are driven by stepper motors transmitting motion through toothed belts. The two gantries are able to move simultaneously. This allows for smooth curvature and jerk-free motion between print operations, as sudden directional changes are minimized. The approach also offers good stability during printing, benefitting the quality of printed outcomes.
This design approach is more complex and requires more effort in setup and calibration than simpler designs. This is particularly affected by the belt drives requiring very good alignment to ensure accurate and repeatable motion. Some users also report difficulty in accessing the print bed to make adjustments during printing, as the two gantries can block access at times during printing.
3. CoreXY
A CoreXY gantry system is a structure used in 3D printer design that has stationary stepper motors to drive the X and Y axes. This reduces the mass in motion in the gantry during Y-axis movements, as the Y-axis drive remains fixed in place. This enables higher acceleration and more precise movements of the printhead, providing higher-quality printed outcomes.
The CoreXY system works by using a series of pulleys and recirculating (loop) belts arranged so that the drive belts cross over each other at the core or center of the system. Driving the toothed belts moves the printhead in both the X and Y directions with lower inertia.
Moving less mass allows for a lighter gantry structure. There is less moving mass to resist at high acceleration moments. This approach is more sensitive to belt tension and slide condition than other systems and can be complex to set up and calibrate. The acceleration capacity is considered enough of an advantage to outweigh the setup issues, so this system is popular among some users in the more advanced category.
4. i3-Style Cartesian-XZ-Head
The i3-style Cartesian-XZ-Head is very widely used in 3D printer design. In this approach, the print platform itself is lifted and lowered (Z-axis motion), while the printhead is separately transported on the gantry for the X and Y axes. The extruder is mounted on a carriage that moves along the X and Y axes on precision-ground shafts, using recirculating ball bushes. On larger and higher-priced machines, the rails can be in V form, with roller bearings running on these rails.
This design is simple and easy to construct, making it a popular choice for home/hobby 3D printers. It delivers good accuracy and precision in smaller machines, but generally, it require moderation in acceleration and direction changes due to relatively low stiffness and high inertia.
The primary drawback to this design is that it can be very difficult to maintain a level bed and achieve consistent layer thicknesses. The poor rigidity, compared with other, higher-price 3D printer designs can have very significant effects at higher axis speeds/accelerations.
5. H-Bot
The H-bot is a gantry system employed in some 3D printers. It uses belt drives and linear rails in a layout that, similar to the CoreXY system, has stationary motors to drive the X and Y axes.
The two belts for X and Y form the shape of an “H.” One belt is attached to the printhead and moves along the Y-axis. The other belt is attached to the other end of the gantry and moves along the X-axis. The printhead is carried on a Z drive that moves along the two main axis rails.
The H-bot layout can be more stable and rigid than other 3D printer designs, providing higher-quality printed outcomes. Stationary motors reduce the system inertia, allowing higher accelerations and requiring less stiffness for good stability.
The H-bot design is complicated to set up and hard to calibrate and is reported as requiring more maintenance. Any slight slack that develops in the belts will disrupt X-Y precision significantly, which is a particular issue in maintenance as belts can stretch. However, when well maintained, the H-bot is an effective gantry system that is capable of delivering high quality and high speed.