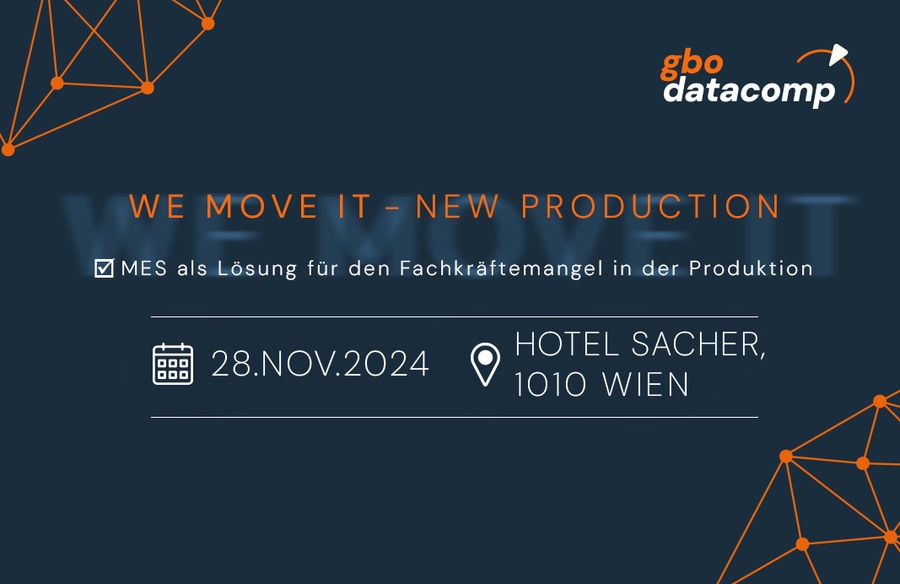
#Industry News
Compensating for a lack of skilled workers with MES
In industry, the shortage of skilled workers is threatening the future of many manufacturing companies. Manufacturing Execution Systems (MES) show ways to overcome the shortage of skilled workers with the help of digitalization and increase productivity.
The weakening economy really doesn't have many advantages. However, it does mean that the demand for skilled workers is declining, as can be seen from the current KfW-ifo Skilled Workers Barometer. However, this is little consolation, as the KfW-ifo figures also show that the shortage of skilled workers remains at a high level.
35% of the approximately 9,000 companies surveyed, around 7,500 of which were SMEs, stated that they were hampered in their business activities by a lack of skilled staff in the second quarter of 2024. At 25%, the manufacturing sector is below the average value, but this still affects almost three times as many industrial companies as the long-term average. So where is the shortage of skilled workers in industry?
Shortage in technical professions
According to the study “Skills shortage in industry”, compiled by Heinrich Heine University Düsseldorf and the “Future through Industry” alliance, manufacturing companies are primarily lacking skilled workers in production and technical professions. Around 40 industrial companies, 130 management students and 40 young professionals from North Rhine-Westphalia were surveyed for the study. Almost a third of the industrial companies stated that they have a need in the area of production/technical professions that cannot currently be met. Almost one in five companies also have a shortage of skilled workers in management and administration. This is particularly true for smaller industrial companies.
The study differentiates between companies with an annual turnover of more and less than 20 million euros. For both large and small companies, cost pressure and inflation are the main challenges. However, the shortage of skilled workers is the second biggest challenge, ahead of the tasks that need to be solved in the areas of digitalization or sustainability. Although the shortage of skilled workers is in third place for companies with a higher turnover, in the group of industrial companies with an annual turnover of less than 20 million euros, the shortage of skilled workers ranks far ahead of the other challenges.
The forecasts on the shortage of skilled workers do not point to a turnaround: The ageing population, the “mismatch” between the content of school education and the skills and knowledge that manufacturing companies need today and a migration policy that has come under populist pressure will exacerbate the shortage of skilled workers in the coming years, according to the prevailing opinion of many labor market experts.
Relief from routine tasks
Manufacturing companies embarking on the path to Industry 4.0 are responding to the shortage of skilled workers by investing more in new technologies and adapting their production processes. The degree of automation and digitalization is increasing and employees are being relieved of time-consuming routine tasks. Manufacturing Execution Systems play a central role as data hubs. The MES collects machine and operating data, consolidates it into a homogeneous data set and visualizes it in the form of key performance indicators (KPIs) for efficient digital production planning. This data is not only used in production, but also in ERP right up to management level in the company (horizontal and vertical data integration).
For example, the MES provides the production control center with information on how long a work process takes, to what extent it meets or exceeds tolerance values or how often it needs to be repeated. Many repetitive or manual tasks can be digitized with the help of an MES. Employees are relieved by this digitalization and can devote themselves to their core tasks. Qualified personnel are used less for simple tasks.
Independence through knowledge transfer
The relief provided by digitalized work processes has been gaining in importance for some time now. In order to meet individual customer requirements, companies are producing in ever smaller batch sizes. As a result, machines have to be retooled more frequently. Production planning is becoming more complex - as are the demands on employees. Their workload is reduced by transferring their experience and expertise to the MES. Employees no longer need to know the different characteristics of different machines. The MES takes care of that.
In addition to reducing the workload, the industrial company benefits from this knowledge transfer, as the know-how remains in the company even when experienced employees leave. The MES is the first step towards in-depth knowledge management, which of course also enables industrial companies to reduce their dependence on labor. Ultimately, the end result of Industry 4.0 is the autonomous component that finds its own optimal route across the fully automated store floor. The increase in production efficiency inevitably results in a reduced need for human labor.
Process monitoring and quality management
Digitalization using MES solutions enables continuous monitoring and adjustment of production processes in real time, as the MES used identifies potential for optimisation. Once implemented, this increases the efficiency of production processes. As a result, the industrial company can handle a larger production volume with fewer personnel.
Real-time process monitoring and quality management enable employees to react immediately to deviations in production processes or material bottlenecks. On the one hand, this minimizes rejects and downtimes. On the other hand, production management can work more efficiently because less rescheduling is necessary, even if only a few experienced specialists are available.
It is particularly important to relieve these experienced specialists when know-how and responsibility are spread over a few shoulders. The quality management of an MES reduces the error rate of employees, taking the pressure off them and reducing their stress. Personnel time recording integrated into an MES leads to a more efficient use of available manpower in order to avoid overloads, stress and the associated consequences, such as sick leave. Ultimately, the industrial company can also offer flexible working time models and thus increase its attractiveness for skilled workers.
By analyzing historical data, MES solutions can also develop forecasts that can be used for maintenance and servicing, for example (predictive maintenance). In short: a machine is serviced in good time before it breaks down for an extended period of time. This increases the longevity and availability of the machines and reduces the need for repairs. As a result, fewer skilled personnel are required.
Modular MES for more flexibility
Even if the demand for skilled personnel is falling due to the current weak economy, this development will not be permanent. As soon as the economy picks up again, the demand for qualified workers will rise again. The shortage of skilled workers is here to stay. The effects of political measures taken now in areas such as education or migration will certainly be years in coming - if there are any positive effects at all.
No manufacturing company can wait that long if it wants to hold its own in the face of tough global competition. Many industrial companies are therefore focusing on digitalization and the advantages outlined here, which technologies such as MES solutions bring with them. Modular solutions that can be flexibly adapted to the individual needs of each company are particularly in demand. If these needs change, the MES also changes without having to start from scratch again. This deepens horizontal and vertical data integration within the company, mitigates the consequences of the shortage of skilled workers and successively implements the vision of Industry 4.0 at the company's own pace of digitalization.